

Why Electrical Grade Aluminum Bus Bars Are Essential
Introduction
In the modern era of electrical and power systems, achieving efficiency, reliability, and cost-effectiveness is crucial. Among the components that have become fundamental to meeting these goals is the electrical grade aluminum bus bar. These essential elements play a pivotal role in ensuring seamless power distribution in various sectors, from industrial plants to renewable energy systems and transportation infrastructure.
The significance of electrical grade aluminum bus bars stems from their unique combination of properties, including high conductivity, lightweight design, and resistance to corrosion. This blog will provide a comprehensive look at why these bus bars are indispensable, exploring their features, advantages, applications, and maintenance requirements, as well as comparing them to traditional materials like copper.
What is an Electrical Grade Aluminum Bus Bar?
An electrical grade aluminum bus bar is a flat, rectangular piece of aluminum that serves as a conductor for electrical power. Its primary function is to carry and distribute current in electrical systems efficiently. Made from high-purity aluminum or specific aluminum alloys, these bus bars are engineered to meet the demanding requirements of modern power systems.
The term "electrical grade" refers to the high-quality aluminum used in their production. This grade ensures superior conductivity, strength, and durability. The design and composition of these bus bars make them ideal for handling high currents with minimal energy loss, a crucial feature in both large-scale power grids and smaller industrial setups.
Key characteristics of electrical grade aluminum bus bars include their flat design, which facilitates efficient heat dissipation, and their ability to be customized for specific applications. These attributes make them a versatile choice for engineers and system designers.
Features of Electrical Grade Aluminum Bus Bars
1. High Conductivity
Although aluminum has slightly lower electrical conductivity than copper, it remains an excellent conductor of electricity. The high purity of the aluminum used in electrical grade bus bars ensures minimal resistance, allowing them to efficiently carry large currents without significant energy loss.
2. Lightweight Design
Aluminum’s low density makes it a lightweight material, approximately one-third the weight of copper. This feature simplifies transportation, installation, and handling, reducing labor and logistics costs. Additionally, its lightweight nature reduces the load on supporting structures, further contributing to cost savings.
3. Corrosion Resistance
Aluminum naturally forms a thin oxide layer on its surface when exposed to air. This layer acts as a protective barrier against environmental factors like moisture, chemicals, and extreme temperatures. This corrosion resistance is particularly beneficial in outdoor and marine environments where exposure to harsh conditions is common.
4. Thermal Efficiency
Efficient heat dissipation is vital in electrical systems to prevent overheating. Aluminum’s excellent thermal conductivity ensures that heat generated by electrical currents is evenly distributed and dissipated, enhancing the safety and longevity of the system.
Advantages of Electrical Grade Aluminum Bus Bars
1. Cost-Effectiveness
One of the most compelling reasons to choose aluminum over copper is its affordability. Aluminum is more abundant and less expensive to mine and refine, making it a cost-effective solution for projects requiring extensive electrical infrastructure. This cost advantage is especially significant in large-scale applications like substations and industrial plants.
2. Sustainability
In an era of increasing environmental awareness, the recyclability of aluminum stands out. Aluminum can be recycled indefinitely without losing its properties, making it an environmentally friendly choice. This sustainability aligns with the goals of industries striving to reduce their carbon footprint.
3. High Strength-to-Weight Ratio
Despite being lightweight, aluminum is remarkably strong. This high strength-to-weight ratio allows aluminum bus bars to withstand mechanical stress while being easy to handle and install.
4. Customizability
Electrical grade aluminum bus bars can be manufactured in various sizes, shapes, and thicknesses to meet specific project requirements. This customizability ensures that they can be tailored to fit diverse applications, from compact electronic devices to massive power distribution systems.
Applications of Electrical Grade Aluminum Bus Bars
1. Power Distribution Systems
Electrical grade aluminum bus bars are extensively used in power distribution systems, including substations and electrical panels. They serve as the backbone of these systems, efficiently transmitting electricity between components while minimizing energy loss.
2. Industrial Equipment
In industrial settings, aluminum bus bars distribute power to machinery and equipment. Their ability to handle high currents ensures consistent performance and reduces downtime caused by electrical inefficiencies.
3. Renewable Energy Systems
Solar and wind energy systems rely on aluminum bus bars for their lightweight and corrosion-resistant properties. These bus bars are used to connect solar panels or wind turbines to inverters and power grids, ensuring efficient energy transfer.
4. Transportation
Aluminum bus bars are commonly found in transportation applications, including railways, ships, and electric vehicles. Their lightweight nature and excellent conductivity make them ideal for reducing energy consumption and improving system efficiency in these sectors.
Comparing Aluminum to Copper Bus Bars
1. Cost Comparison
Copper is significantly more expensive than aluminum, making aluminum a more viable option for budget-conscious projects. This cost difference becomes especially apparent in large-scale installations where the use of copper would drastically increase overall expenses.
2. Weight Differences
The lightweight nature of aluminum gives it a clear advantage over copper in terms of handling and installation. Aluminum’s reduced weight also lowers transportation costs and structural support requirements.
3. Corrosion and Oxidation
While copper has excellent resistance to corrosion, aluminum’s natural oxide layer provides adequate protection in most environments. Additionally, aluminum can be treated with coatings or anodized to enhance its corrosion resistance further.
4. Performance
Although copper has slightly better electrical conductivity than aluminum, the difference is negligible in many applications. Aluminum bus bars are often made thicker to compensate for this difference, ensuring comparable performance at a lower cost.
Key Considerations When Using Electrical Grade Aluminum Bus Bars
1. Sizing and Thickness
To ensure optimal performance, aluminum bus bars must be sized appropriately for the current load they will carry. This often involves increasing their thickness compared to copper bus bars to account for aluminum’s lower conductivity.
2. Joining and Connections
Proper techniques are essential when joining aluminum bus bars to prevent issues like corrosion and electrical resistance at the joints. Using anti-oxidizing compounds and compatible fittings helps maintain secure and efficient connections.
3. Coatings and Treatments
Applying protective coatings or anodizing aluminum bus bars can enhance their durability and resistance to environmental factors. These treatments are particularly beneficial in harsh conditions, such as marine or industrial environments.
Innovations in Electrical Grade Aluminum Bus Bars
Recent advancements in material science have led to the development of improved aluminum alloys with enhanced strength, conductivity, and corrosion resistance. These innovations have expanded the application scope of aluminum bus bars, making them suitable for more demanding environments.
Additionally, advancements in manufacturing processes, such as precision extrusion and machining, have enabled the production of highly customized aluminum bus bars tailored to specific project requirements.
The Role of Electrical Grade Aluminum Bus Bars in Renewable Energy
Renewable energy systems, such as solar and wind farms, rely heavily on electrical grade aluminum bus bars for efficient energy transmission. These systems often operate in remote or harsh environments, where the lightweight and corrosion-resistant properties of aluminum provide a significant advantage.
Aluminum bus bars are also more affordable, aligning with the cost-sensitive nature of many renewable energy projects. Their recyclability further supports the sustainability goals of these systems, making them an ideal choice for the renewable energy sector.
Maintenance Tips for Electrical Grade Aluminum Bus Bars
To ensure the longevity and performance of aluminum bus bars:
- Regular Inspections: Periodically check for signs of wear, damage, or oxidation.
- Cleaning: Remove dirt and debris to maintain efficient conductivity.
- Anti-Oxidizing Compounds: Apply these to connections to prevent oxidation and ensure secure joints.
- Proper Torque: Use the correct torque when fastening connections to avoid loosening or overtightening.
Conclusion
The electrical grade aluminum bus bar has become an essential component of modern electrical systems. Its unique combination of affordability, lightweight design, and excellent conductivity makes it a superior choice for a wide range of applications, including power distribution, industrial equipment, renewable energy systems, and transportation.
As industries prioritize efficiency, sustainability, and cost-effectiveness, the demand for aluminum bus bars is expected to grow. By investing in these versatile and durable components, engineers and project managers can ensure reliable performance while supporting eco-friendly practices.
Electrical grade aluminum bus bars are more than just conductors; they are the backbone of efficient and sustainable electrical systems.
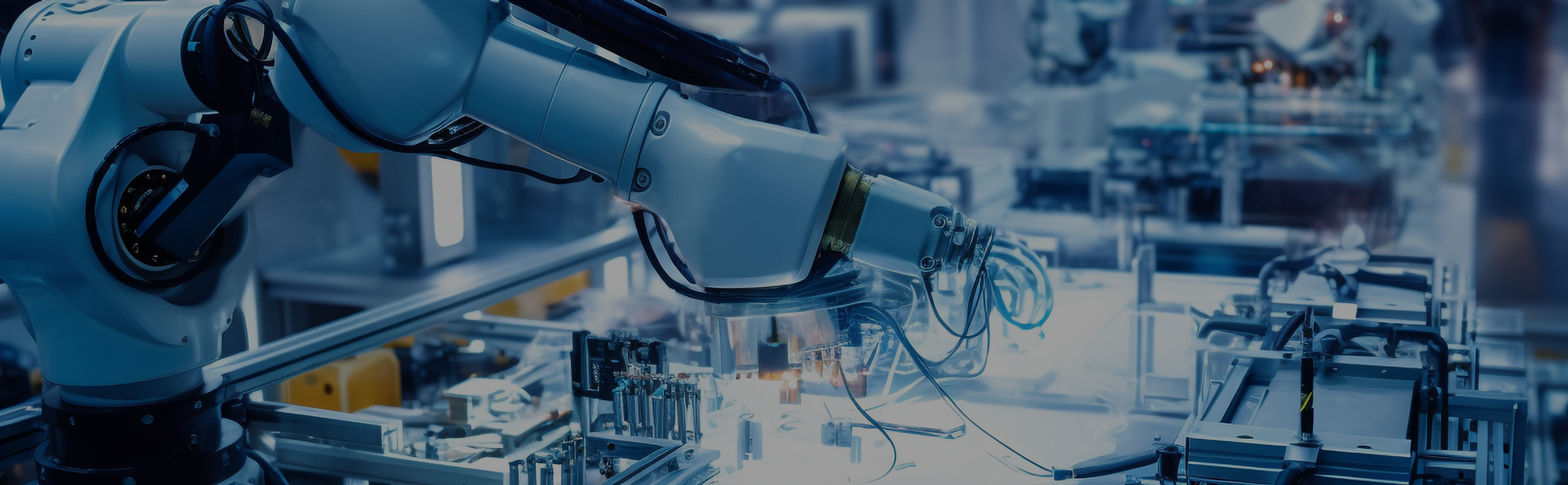