

Understanding Thermal Runaway Prevention in Electrical Systems
Explore thermal runaway, its potential risks, and how electrical busbars contribute to its prevention, providing valuable insights for engineers, safety officers, and anyone working with high-voltage systems.
Thermal runaway is a phenomenon that can have catastrophic consequences in electrical systems, especially in high-power applications such as batteries, electric vehicles, and large-scale electrical equipment. One of the crucial components that help mitigate thermal runaway is the electrical busbar, which plays a significant role in ensuring the safety and efficiency of electrical systems. In this comprehensive guide, we will explore thermal runaway, its potential risks, and how electrical busbars contribute to its prevention, providing valuable insights for engineers, safety officers, and anyone working with high-voltage systems.
What is Thermal Runaway?
Thermal runaway occurs when an increase in temperature leads to a chain reaction that further accelerates temperature rise, creating an uncontrollable feedback loop. In electrical systems, this can happen when excessive current or power causes components like batteries, capacitors, or resistors to overheat. The overheating can cause a breakdown in insulation materials, further increasing resistance and leading to even more heat generation. This positive feedback cycle can eventually lead to fires, explosions, or permanent damage to electrical components.
Thermal runaway is most commonly associated with batteries, particularly lithium-ion batteries. However, it can affect any electrical system where overheating becomes a risk. This is why understanding thermal runaway prevention is essential for safeguarding both the equipment and the environment.
How Does Thermal Runaway Occur?
Thermal runaway typically starts with an external factor, such as excessive voltage, high current, or poor ventilation, leading to an increase in temperature. This heat can then cause damage to the components, often starting with the insulation material. As the temperature continues to rise, the materials in the system may begin to break down, releasing energy that further accelerates the temperature increase.
In the case of lithium-ion batteries, for example, thermal runaway can start when the battery is overcharged or exposed to high temperatures. The chemical reactions inside the battery can become uncontrollable, leading to the release of gases and, in extreme cases, fire or explosion.
Thermal Runaway Prevention: Key Strategies
To mitigate the risks associated with thermal runaway, a combination of strategies should be employed. These strategies include designing systems that dissipate heat effectively, monitoring temperatures continuously, and using materials that can withstand high temperatures. Let's take a closer look at how these approaches work in practice.
1. Efficient Heat Management
Proper heat dissipation is one of the most important strategies for preventing thermal runaway. High-power electrical systems generate significant amounts of heat, which must be managed to prevent overheating. This can be achieved through:
Active cooling systems: Fans, liquid cooling, and heat sinks can help regulate temperature in components like batteries and electric motors.
Thermal insulation: Heat-resistant materials can protect sensitive components from excessive temperatures. In electrical systems, these materials help keep heat from spreading to surrounding areas.
Temperature sensors: These sensors continuously monitor the temperature of critical components and allow for real-time adjustments to cooling mechanisms. They are a key part of modern thermal runaway prevention systems.
2. Monitoring and Control Systems
In addition to heat management, monitoring the system’s performance in real-time is essential for preventing thermal runaway. This includes:
Thermal management software: Many advanced systems use software that constantly monitors temperature, current, and voltage. These systems can alert operators if conditions are approaching dangerous levels, enabling them to take preventative action.
Current limiters and fuses: These devices automatically shut down or limit current flow if the system detects an overload, preventing the components from overheating. This is particularly important in battery management systems (BMS) for electric vehicles.
Safety cutoffs: Automated shutoff mechanisms that disconnect power when temperatures exceed a certain threshold can prevent thermal runaway from escalating into a catastrophic event.
3. Material Selection and Component Design
The materials used in electrical systems play a crucial role in preventing thermal runaway. Components like capacitors, resistors, and batteries should be designed with temperature tolerance in mind. For instance, lithium-ion batteries may include built-in safety features, such as thermal fuses or vents to release pressure if the temperature rises too high.
Moreover, component manufacturers are developing advanced materials that offer better heat resistance, reducing the chances of a system failure due to thermal runaway.
The Role of Electrical Busbars in Thermal Runaway Prevention
One critical element in thermal runaway prevention is the electrical busbar. A busbar is a metallic strip or conductor used to distribute electrical power across multiple circuits or components in electrical systems. They are found in various applications, including power distribution panels, switchboards, and large-scale electrical systems.
1. Conductive Material Selection
The material used in electrical busbars plays a key role in preventing overheating and thermal runaway. Busbars are typically made from copper, aluminum, or a combination of both, chosen for their excellent conductivity and heat dissipation properties. Copper busbars, in particular, are preferred in high-power systems due to their lower resistance and better thermal performance.
By selecting the right materials, busbars can effectively conduct and distribute power without generating excessive heat. This is critical in high-load systems, where poor heat management could lead to thermal runaway in other components.
2. Temperature Monitoring and Busbar Design
Advanced busbar systems are designed to allow for optimal airflow and heat dissipation. Modern busbars are equipped with temperature sensors that monitor the heat levels in real-time. If the temperature rises beyond safe limits, the busbar system can trigger an automatic shutdown or activate cooling mechanisms.
The design of the busbar itself can also affect its thermal performance. For example, busbars with larger surface areas or integrated cooling channels are better at dissipating heat, reducing the risk of overheating.
3. Integration with Safety Systems
Busbars are often integrated with safety features such as fuses and circuit breakers. These devices work together to cut off power to the system in the event of a thermal runaway situation. Fuses and circuit breakers can isolate a malfunctioning section of the busbar, preventing the problem from affecting the entire system.
Furthermore, busbars are often used in conjunction with other safety mechanisms, such as current limiters, which help to prevent excessive currents that can cause overheating in the first place.
Understanding Electrical Busbars in More Detail
Electrical busbars are fundamental components in electrical power systems. Their role is to distribute electrical power from a single source to multiple destinations in an organized and safe manner. Busbars are designed to handle high current and ensure efficient power distribution with minimal losses.
Key Components of Electrical Busbars
- Conductor: The main element that carries the electrical current. The conductor is typically made of copper or aluminum, as mentioned earlier.
- Insulation: Busbars are often insulated to prevent electrical shorts and to protect operators from accidental contact with the conductive parts.
- Mounting System: Busbars are usually mounted within a framework to hold them in place and allow for safe connection to other electrical components.
Applications of Electrical Busbars
Busbars are used in various industries, including:
- Power distribution systems: Busbars are used in substations and switchgear to distribute electrical power to different circuits and devices.
- Electric vehicles (EVs): In EVs, busbars are used to connect the battery pack to the rest of the electrical system. This is crucial in high-voltage battery systems where efficient and safe power distribution is essential.
- Industrial electrical systems: Busbars are used in factories and large industrial plants to manage the power needs of heavy machinery and equipment.
Conclusion
Thermal runaway prevention is a critical aspect of electrical system safety, and it requires a combination of strategies, including efficient heat management, real-time monitoring, and careful material selection. Electrical busbars play a vital role in this process, ensuring the safe and efficient distribution of electrical power. By using high-quality materials, integrating advanced safety features, and designing busbars with thermal management in mind, we can significantly reduce the risks of thermal runaway.
As electrical systems continue to evolve and become more complex, the role of components like busbars will only grow in importance. It is essential for engineers, safety officers, and designers to stay up to date with the latest technologies and best practices in thermal runaway prevention to ensure the safety and efficiency of their systems.
By understanding the intricate relationship between thermal runaway prevention and the use of electrical busbars, we can continue to build safer and more reliable electrical systems that power our homes, vehicles, and industries.
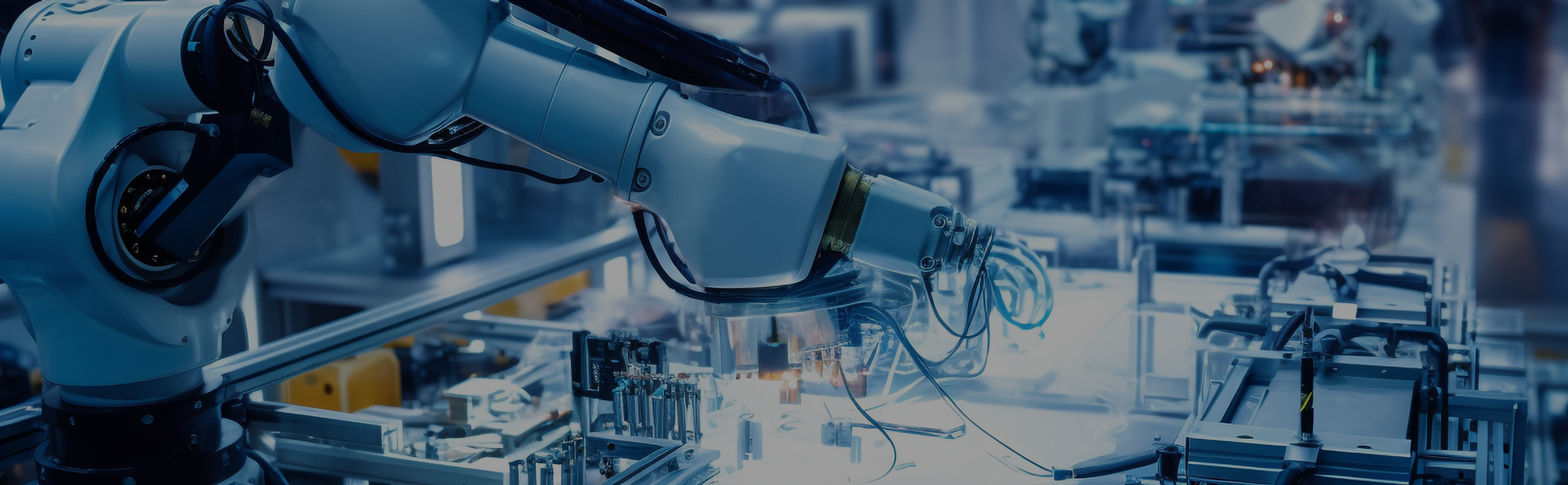