

High-Temperature Busbar Solutions for the New Energy Sector
In the new energy sector, including applications such as electric vehicles and energy storage systems, busbars are crucial for reliable performance under high temperatures and voltages. RHI has developed advanced high-temperature insulation solutions for power busbars, offering full support for high-temperature busbar production and expert technical assistance.
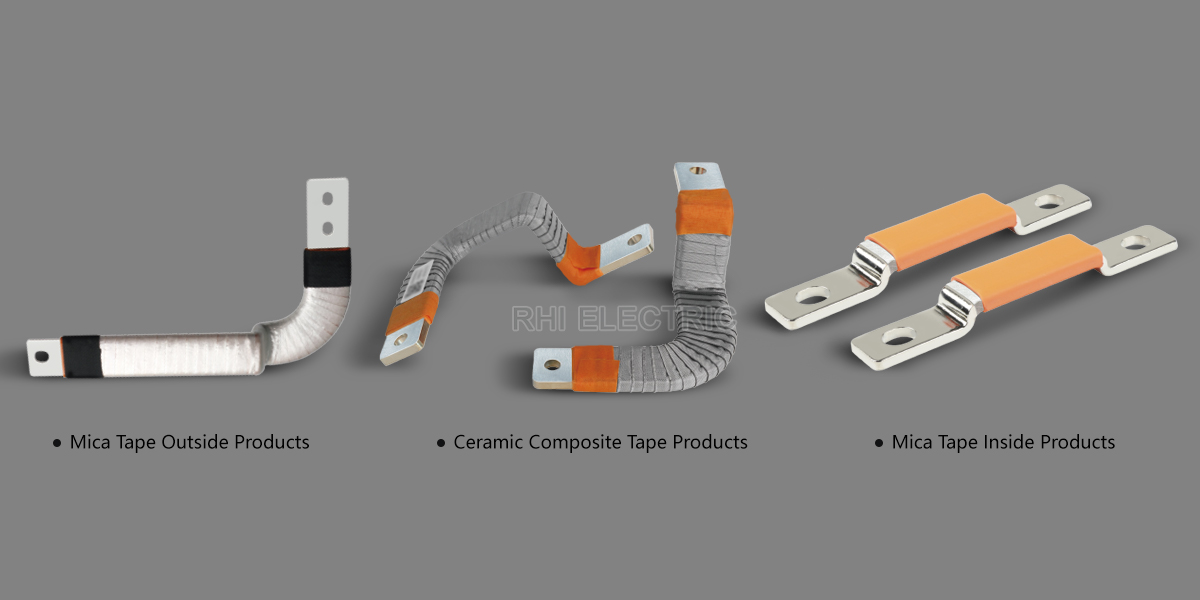
Material Selection & Design
Busbars in new energy systems must withstand high currents and extreme environmental conditions. Essential materials for high-temperature performance include:
- Mica Tape: Known for its excellent heat resistance and electrical insulation up to 1000°C. Key properties include:
- Voltage Withstanding: 3500V DC, with leakage current <1mA.
- Insulation Resistance: ≥500MΩ at 1000V DC for 60 seconds.
- Ceramic Composite Tape: Provides high thermal stability and maintains structural integrity and insulation at elevated temperatures.
- Ceramic-Enhanced Silicone Rubber Tape: Forms a durable ceramic layer under high temperatures, ensuring superior conductivity, insulation, and mechanical strength.
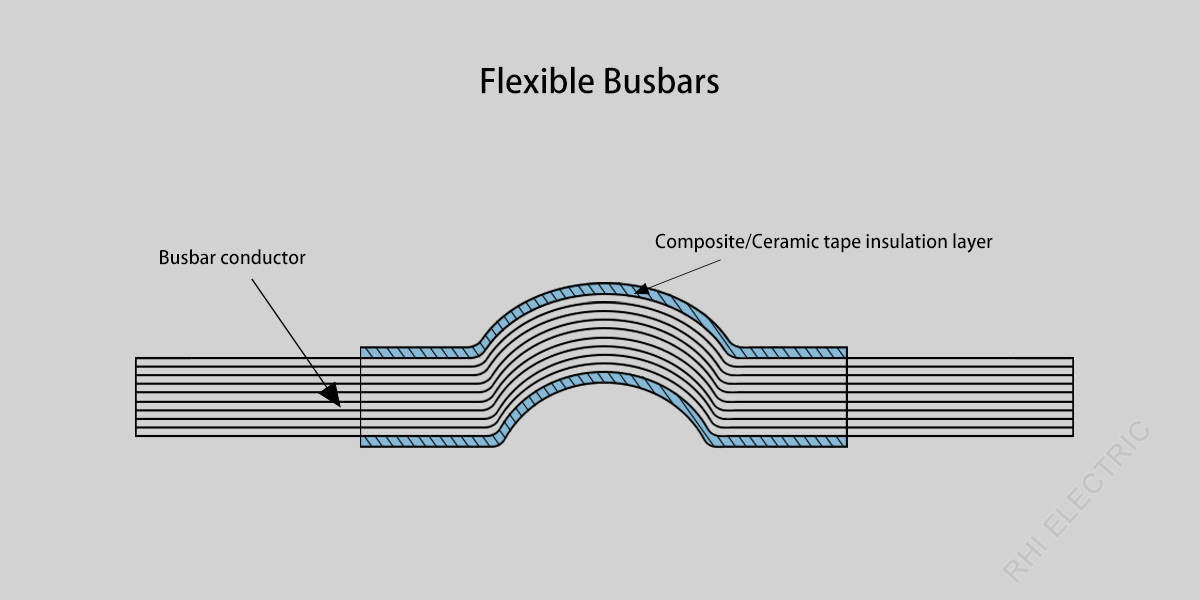
Busbar Forms
Electrical busbars can be designed as either rigid or flexible types, depending on the application and environmental requirements:
Flexible Busbars:
- Design: Including flexible busbars coated with composite/ceramic composite tapes, bonded through high-temperature hot pressing techniques.
- Applications: Suitable for confined spaces and complex wiring configurations in electric vehicles and energy storage systems, providing flexibility and ease of installation.
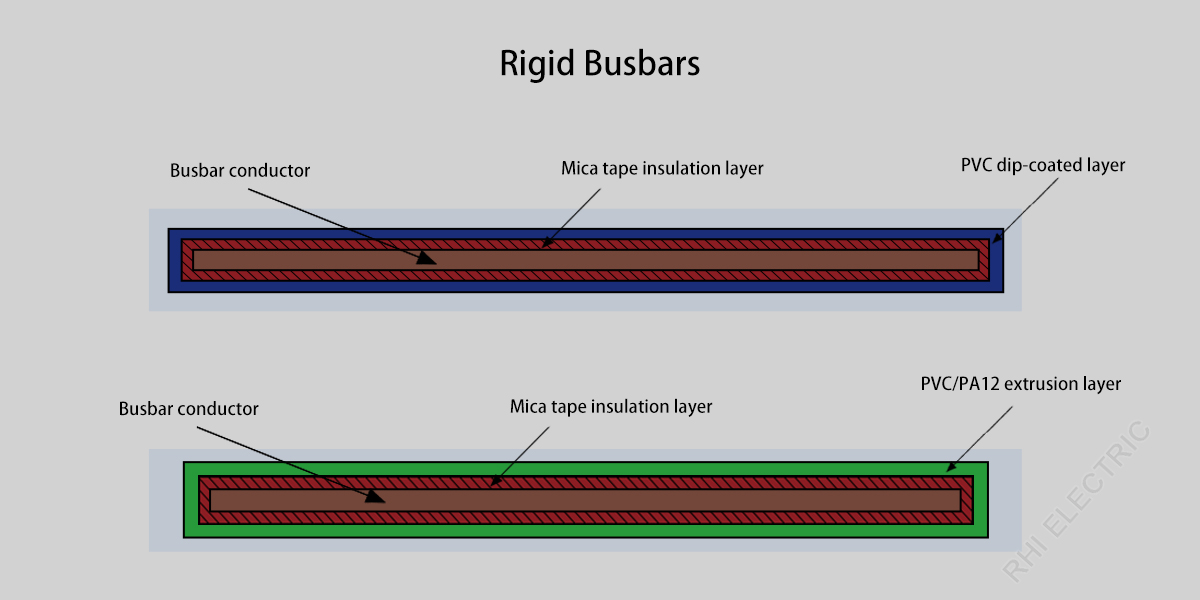
Rigid Busbars:
- Design: Typically made from copper or aluminium, and coated to enhance high-temperature protection.
Mica Tape + PVC
- Coating: The busbar is coated by immersing it in molten PVC to form a uniform insulation layer.
Mica Tape + PVC/PA12 - Extrusion: Uses extrusion to apply a layer of PVC or PA12 for added mechanical strength and insulation.
- Applications: Ideal for high-voltage circuits and main lines in energy storage systems, requiring high current capacity and long-term stability.

Manufacturing Processes
- Coating: Rigid busbars are coated with molten PVC to achieve uniform insulation and enhanced resistance to mechanical damage.
- Extrusion: Applies PVC or PA12 through extrusion to ensure a consistent insulation layer and increased mechanical strength.
- Hot Pressing: Bonds composite or ceramic composite tapes to flexible busbars, improving heat resistance and maintaining stable electrical performance.
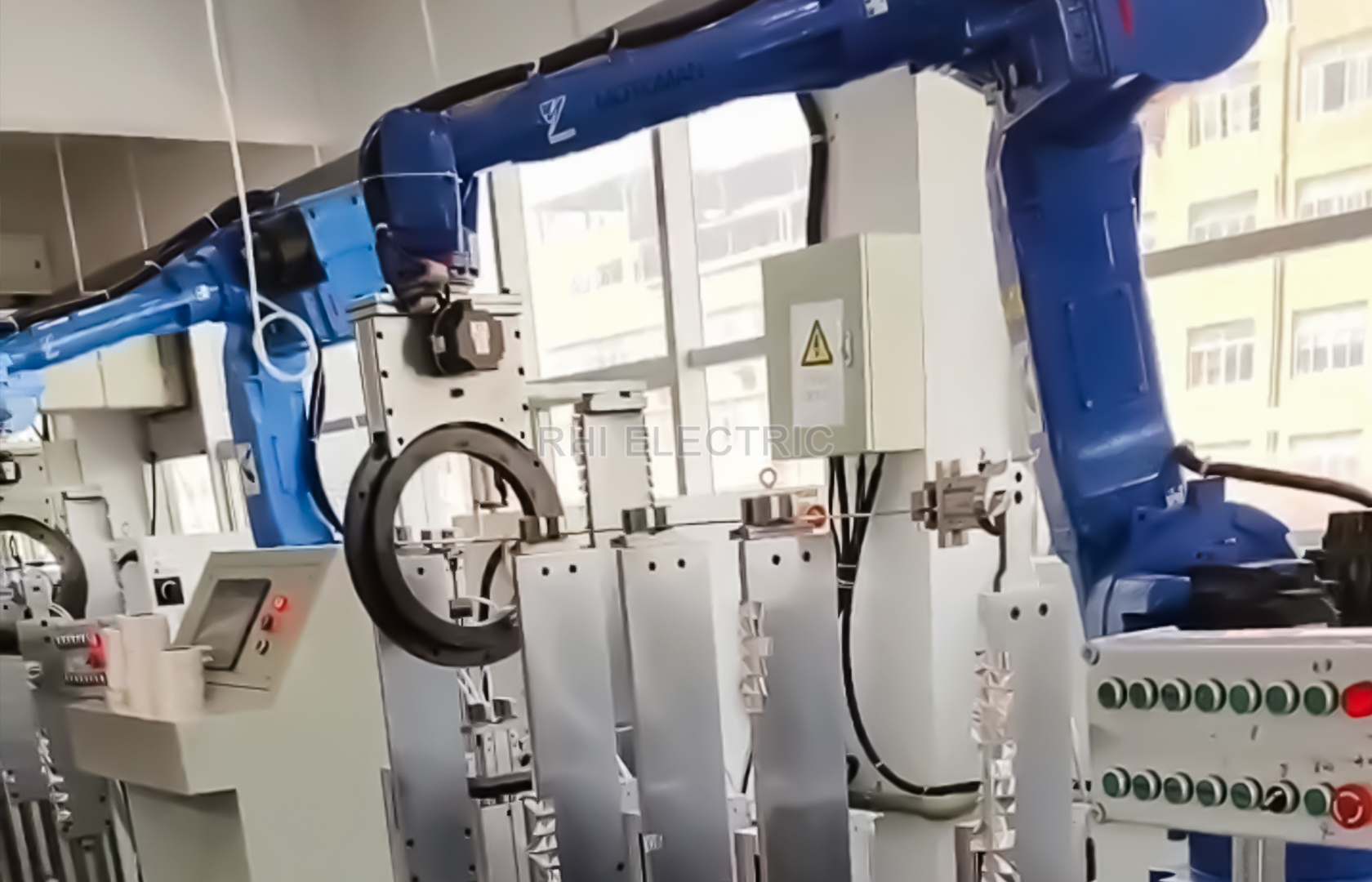
Advantages
Exceptional High-Temperature Performance: Mica, ceramic, and silicone rubber tapes deliver robust insulation and stability under extreme conditions.
- Versatility: Rigid busbars are suitable for high-current main lines, while flexible busbars excel in flexible, confined spaces.
- Reliable Manufacturing: Advanced processes such as coating, extrusion, and hot pressing ensure consistent quality and long-term reliability.
By carefully selecting materials and employing sophisticated manufacturing techniques, both rigid and flexible busbars can achieve superior performance and durability in the demanding environments of the new energy sector. Our state-of-the-art automated winding workshop further enhances production efficiency and quality.