

Extrusion Process Enhances Busbar Performance
The Extrusion Molding Process is vital in producing busbars for new energy applications, primarily by applying an insulating layer to bare copper or aluminium busbars, ensuring safety and optimal performance. With battery busbars increasingly used in electric vehicles and energy storage systems, selecting the right extrusion insulation materials and techniques is crucial.
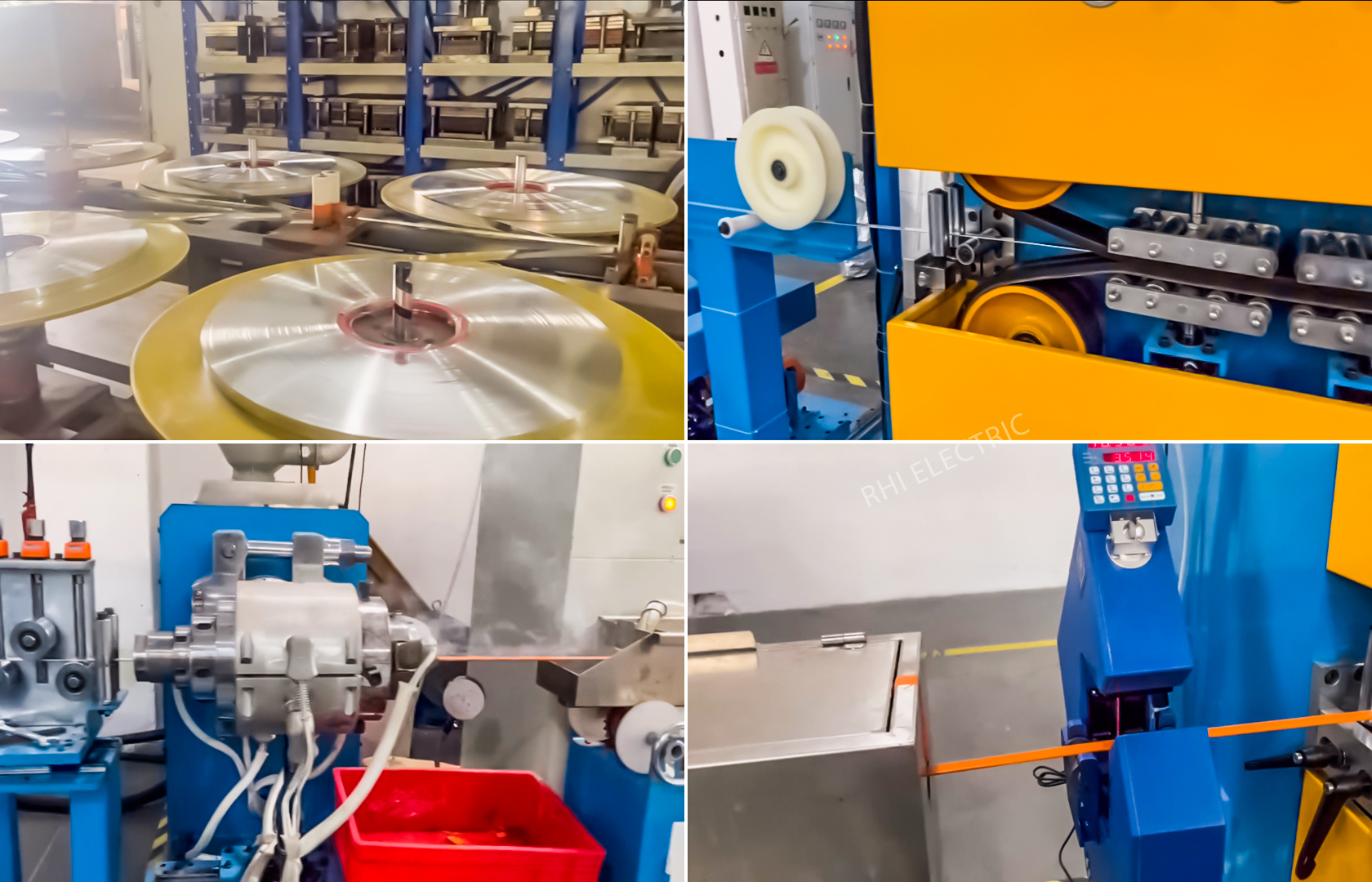
Process Characteristics
The extrusion process uses pressure equipment to coat electroplated bare copper busbars with insulating materials like PVC or PA12, creating a smooth, even layer. This method enables the efficient production of continuously formed busbar products.
- Integrated molding ensures flatness and stability
- Continuous production for high efficiency
- Suitable for long-length, high-volume products with diverse materials
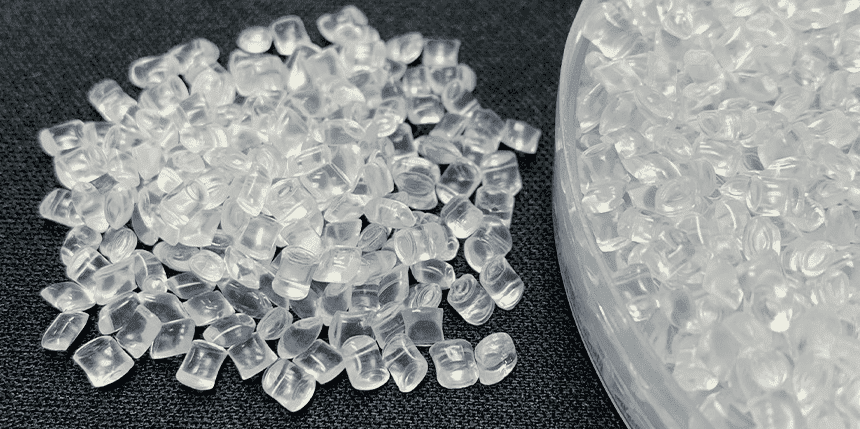
Material Characteristics & Advantages
In our extrusion process, we primarily use Polyamide 12 (PA12) and Polyvinyl Chloride (PVC) as insulating materials, chosen based on the busbar's application environment and performance needs.
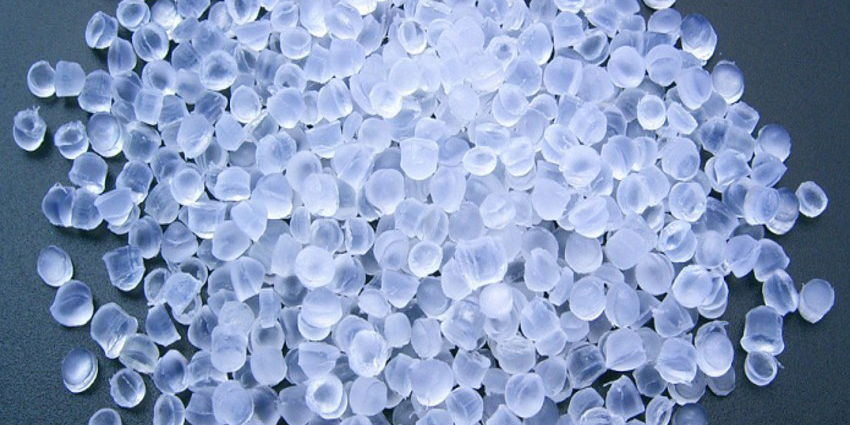
- PA12 Insulation: PA12 is a high-performance plastic with excellent wear and chemical resistance, low moisture absorption, and high-temperature stability, making it ideal for extrusion insulation to enhance busbar durability in EVs and high-voltage equipment.
- PVC Insulation: PVC is a cost-effective, easily processed insulator with good chemical resistance. Though its high-temperature performance is lower than PA12, it provides reliable insulation at standard temperatures. Customizable hardness and thickness make it suitable for both flexible and rigid busbars.
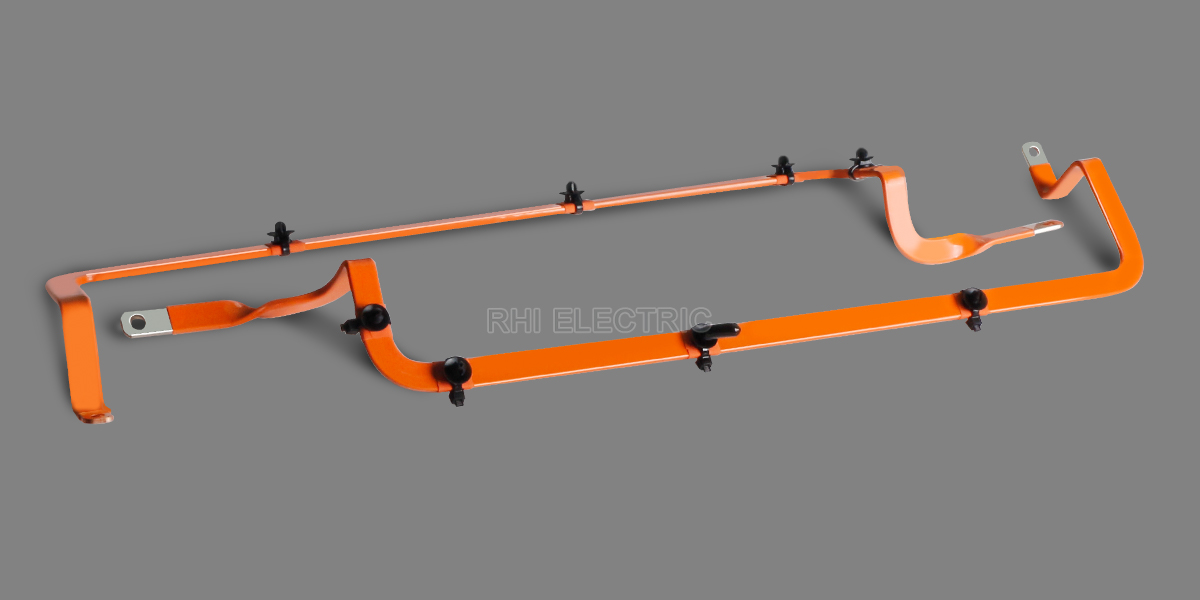
Types & Characteristics of Busbars
Depending on the insulation materials and conductor types used, Extruded Insulated Busbars can be categorized into flexible and rigid types, each with unique characteristics:
- Rigid Busbars: Typically insulated with PA12 or PVC, rigid busbars offer excellent high-temperature resistance and rigidity, making them suitable for fixed installations in high-voltage electrical connections, such as power distribution cabinets and stationary electrical equipment.
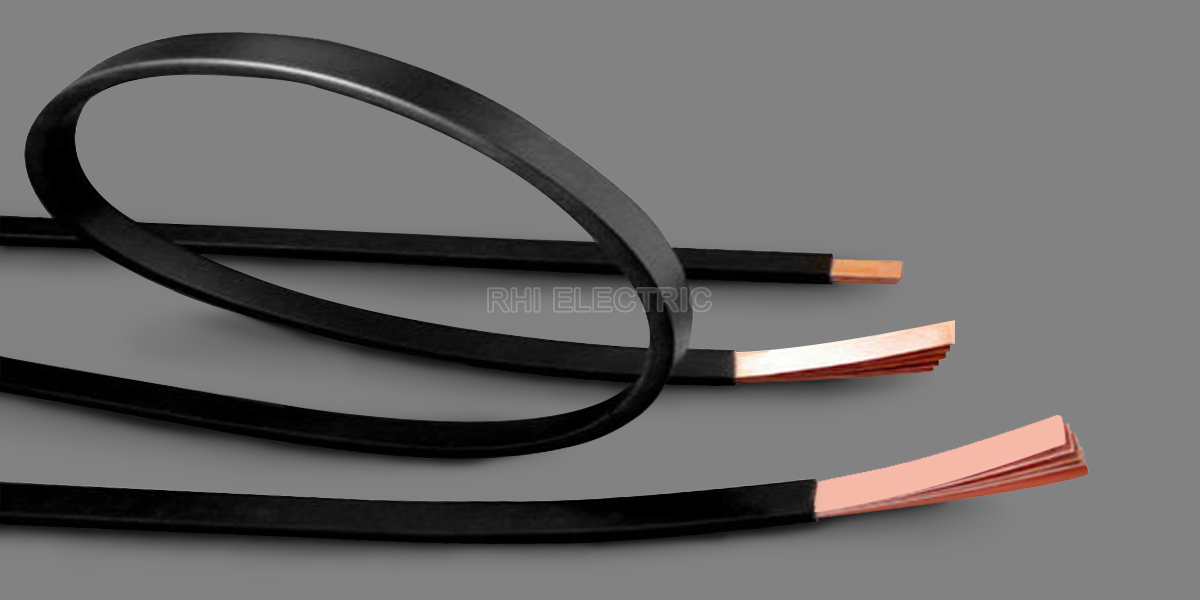
- Flexible Busbars: Our flexible busbars use PVC insulation and typically feature copper or aluminium sheet conductors. These busbars are ideal for applications requiring bending and shaping, such as in electric vehicle battery packs and distribution panels. They are easy to install, offer quick punching, and maintain excellent wear and chemical resistance, performing well even in harsh environments.