

RHI specializes in manufacturing high-quality busbars for the new energy sector using industrial-grade copper with at least 99.9% purity. Our integrated production process and advanced welding techniques, including butt welding, overlap welding, and friction welding, ensure reliable connections for copper-to-aluminium busbars. We provide superior busbar solutions for power transmission and distribution, meeting stringent performance and reliability standards.
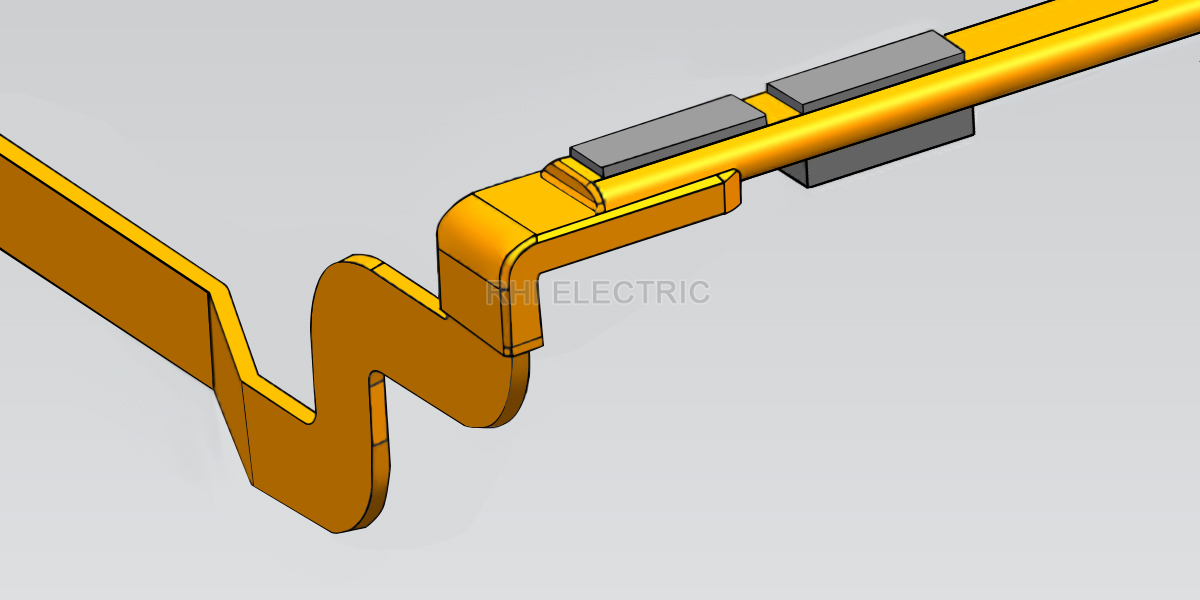
Laser Butt Welding (Butt Welding)
Laser butt welding uses a high-energy laser beam to join materials, offering the following advantages:
- High Precision and Minimal HAZ: The focused laser beam enables precise welding for complex shapes and fine components, minimizing distortion and reducing post-weld treatment.
- High Strength and Speed: Laser welding creates welds stronger than the base material, ideal for high-strength components. Its speed boosts production efficiency, supporting mass production and automation.
- No Filler Material Needed: Typically, no filler material is required, reducing costs and waste while maintaining weld purity and high conductivity.
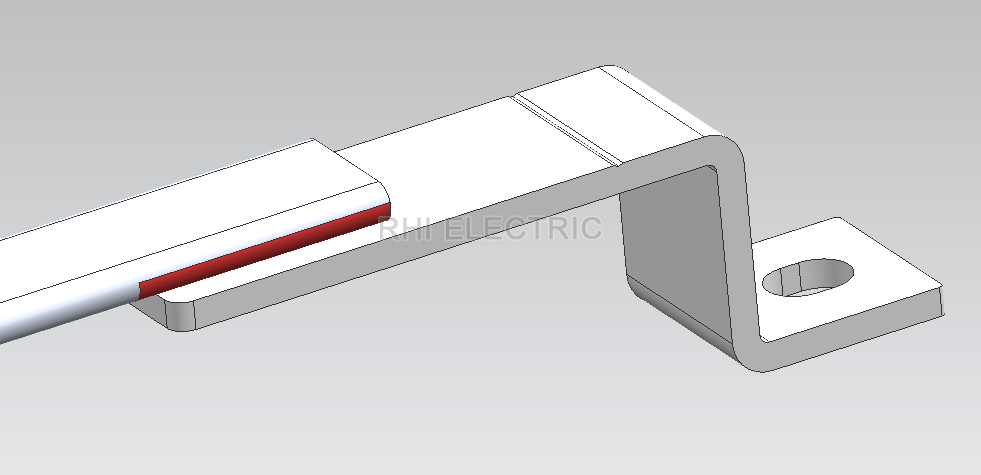
Diffusion Brazing (Overlap Welding)
Diffusion brazing is a high-temperature welding process that bonds materials through diffusion, ideal for joining dissimilar materials. Key advantages include:
- Strong Metallurgical Bonding: Forms a robust bond with strength and toughness comparable to the base material, suitable for demanding mechanical and electrical connections.
- Adaptable for Large Areas and Multilayer Structures: Provides uniform welding for large components, enhancing consistency and stability, especially in multilayer composites.
- Low Residual Stress: The gradual heating and cooling minimize residual stress, improving the welded structure's stability and durability.
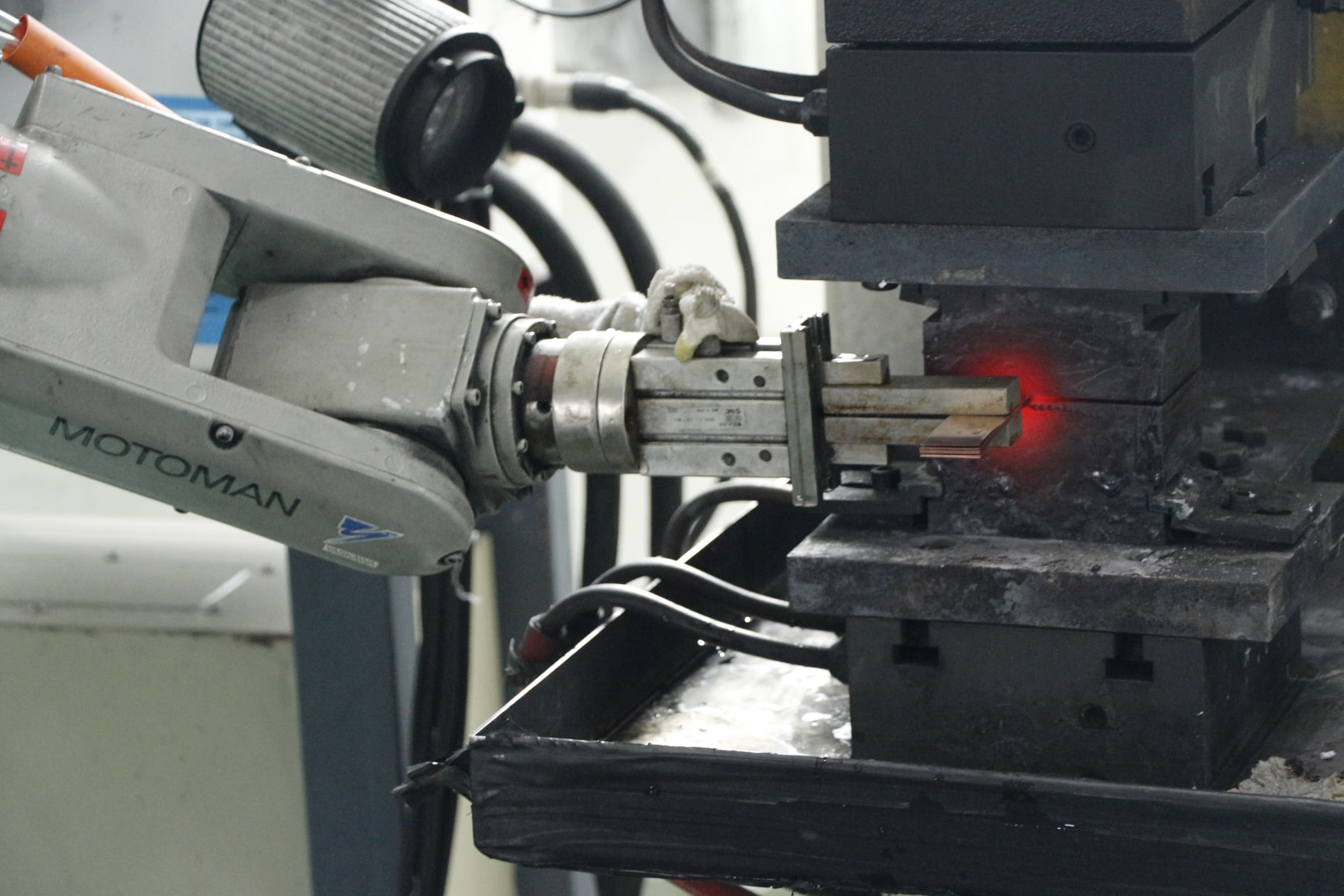
Polymer Diffusion Welding (Overlap Welding)
Polymer Diffusion Welding, or atomic welding, is a solid-state method that bonds materials through atomic diffusion by heating parts below their melting point and applying pressure to form strong metal bonds across the interface.
- Material Versatility: Effectively bonds different polymers and polymers with metals, enhancing flexibility in busbar design and material selection.
- Corrosion Resistance: Weld joints offer superior sealing and chemical resistance, ideal for harsh environments and extended product life.
- High-Temperature and Insulation Properties: Welded polymers retain high-temperature resistance and insulation, ensuring stable busbar operation in demanding conditions.
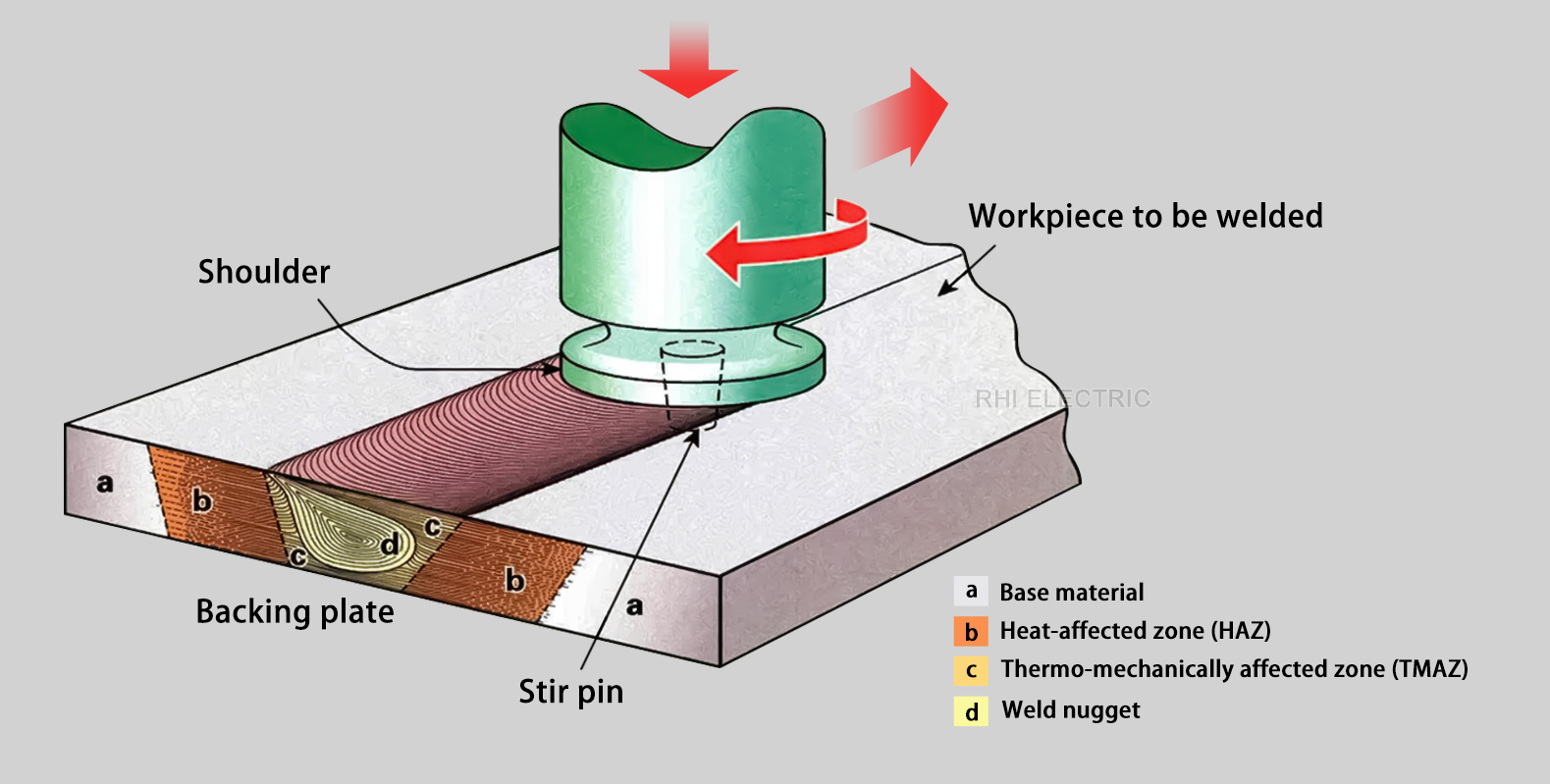
Friction Stir Welding (Butt Welding)
Friction stir welding (FSW) is a solid-state bonding technique that uses a rotating stirring head to penetrate the welded materials, generating frictional heat that softens the material. The stirring tool moves along the welding interface, transferring the softened material from the front to the back, achieving solid-state bonding between workpieces through mechanical forging. The key advantages of friction welding include:
.png)
- No Melting Process: As a solid-state welding process, friction stir welding does not melt the material, thus avoiding typical welding defects such as porosity and cracks, improving weld quality.
- High Welding Efficiency and Strength: This method produces no fumes or harmful gases during welding, and the weld joints exhibit high strength and toughness, meeting the dual requirements of lightweight and strength in new energy equipment.
- Suitable for Dissimilar Material Welding: Friction stir welding can effectively weld dissimilar metals, such as aluminium and copper, providing more possibilities for busbar design.
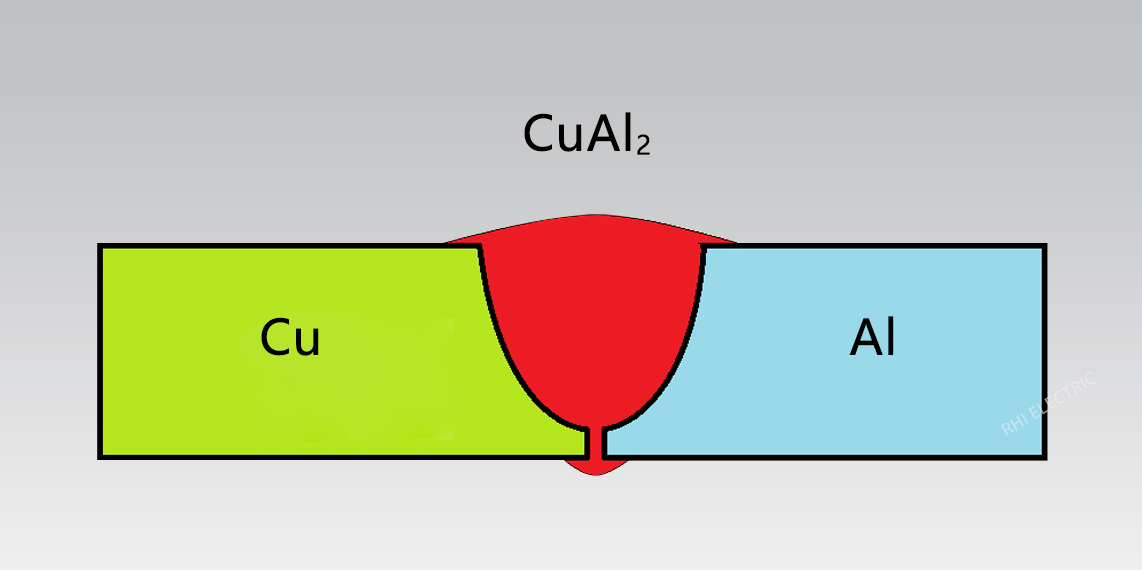
Challenges in Copper-Aluminium Welding
Welding copper-aluminium presents unique challenges due to the material differences and their distinct physical properties, making it more complex than welding identical metals.
1.Oxidation: Copper and aluminium easily oxidize during welding, forming high-melting-point oxides that compromise weld integrity and increase difficulty.
2.Brittleness & Cracking: Copper-aluminium joints are prone to brittleness, especially near the copper side, where fragile copper-aluminium compounds can form, leading to cracks.
3.Melting Point Disparity: The significant difference in melting points between copper and aluminium results in aluminium melting first while copper remains solid, complicating weld control.
4.High Thermal Conductivity: The high thermal conductivity of both metals causes rapid cooling of the weld, trapping gases and leading to porosity.
Solutions for Copper-Aluminium Welding
1. Prior to welding, a nickel coating is applied to the copper busbar to increase the nickel content at the joint, minimizing the formation of copper-aluminium intermetallic compounds. This effectively prevents material diffusion and improves joint reliability.
2. Precise Temperature and Time Control:
a. Avoid Eutectic Temperatures: Optimizing welding temperature reduces the risk of forming intermetallic compounds.
b. Advanced Temperature Control: Using precision equipment to control welding temperature and time limits copper-aluminium diffusion and intermetallic formation.
c. Rapid Heating Methods: High-efficiency heating techniques shorten weld time, reducing exposure to high temperatures and minimizing the thickness of intermetallic layers.
3. Surface Treatment Optimization: Cleaning the copper and aluminium surfaces, especially removing aluminium oxide layers, enhances weld flow and uniformity, improving overall weld quality.