

Surface Treatment Solutions for New Energy Busbars
As a leading manufacturer of new energy busbars, RHI offers a range of high-quality surface treatment processes to meet diverse application needs. These include nickel plating, tin plating, silver plating, and nickel sheet application, each with its own unique benefits and characteristics.
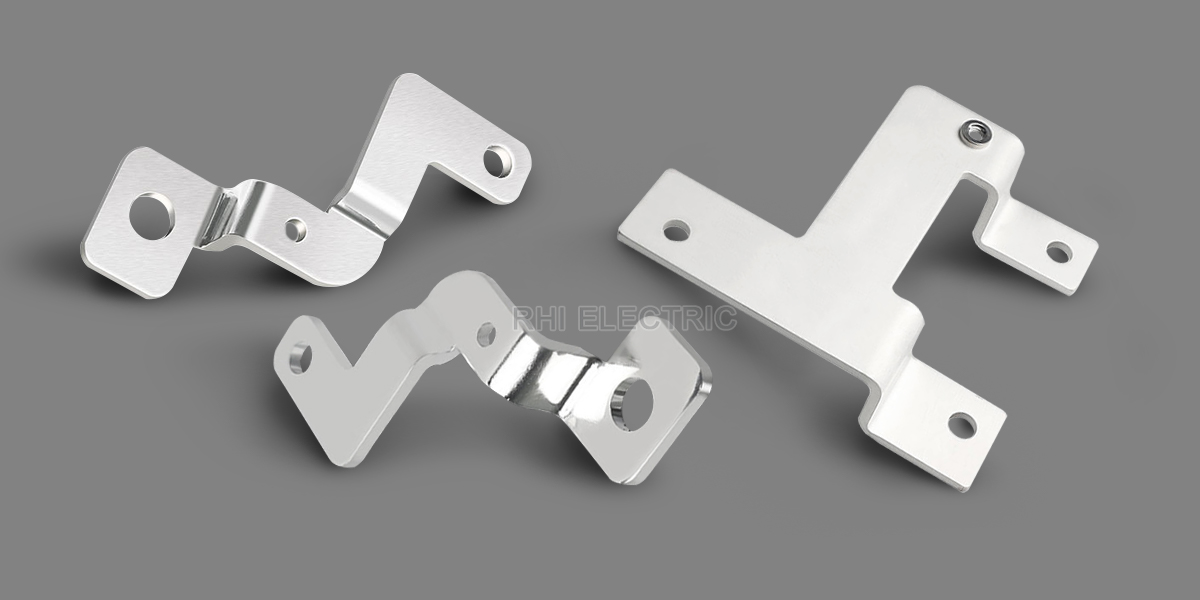
Nickel Plating Process
Nickel plating involves electroplating a uniform nickel layer onto a substrate to enhance corrosion resistance, wear resistance, and decorative appeal of busbars.
- Corrosion Resistance: Nickel plating offers excellent protection against oxidation and corrosion, especially in high-humidity or chemically corrosive environments.
- Wear Resistance: The high hardness of the nickel layer enhances wear resistance, extending the service life of electrical busbars exposed to mechanical friction or vibration.
- Decorative Appeal: Nickel plating provides a bright, attractive finish, improving the visual quality of busbars in applications with high aesthetic requirements.
- Electrical Conductivity: While nickel has slightly lower electrical conductivity than copper, its superior corrosion and wear resistance make it suitable for various applications.
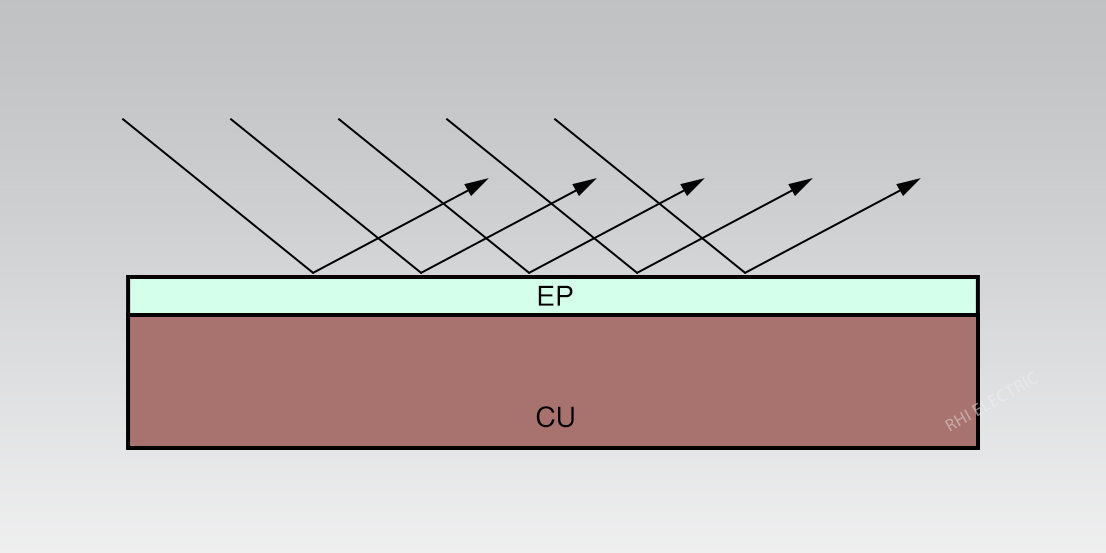
Tin Plating Process
Tin plating involves depositing a layer of tin onto a substrate to enhance the electrical contact performance and solderability of power busbars.
- Oxidation Prevention: Tin plating prevents oxidation and corrosion of busbar joints, ensuring stable electrical connections in long-term or high-temperature environments.
- Improved Contact and Adhesion: Tin’s low melting point allows the surface to bond tightly at contact points when heated, reducing resistance and improving conductivity.
- Solderability: Tin plating facilitates easy soldering, essential for electrical connections that require frequent maintenance.
- Softness & Ductility: The soft, ductile tin layer resists cracking, making it suitable for electric busbars that need mechanical flexibility.
- Cost-Effectiveness: Tin plating is an economical choice for applications needing good conductivity and solderability without high corrosion resistance.
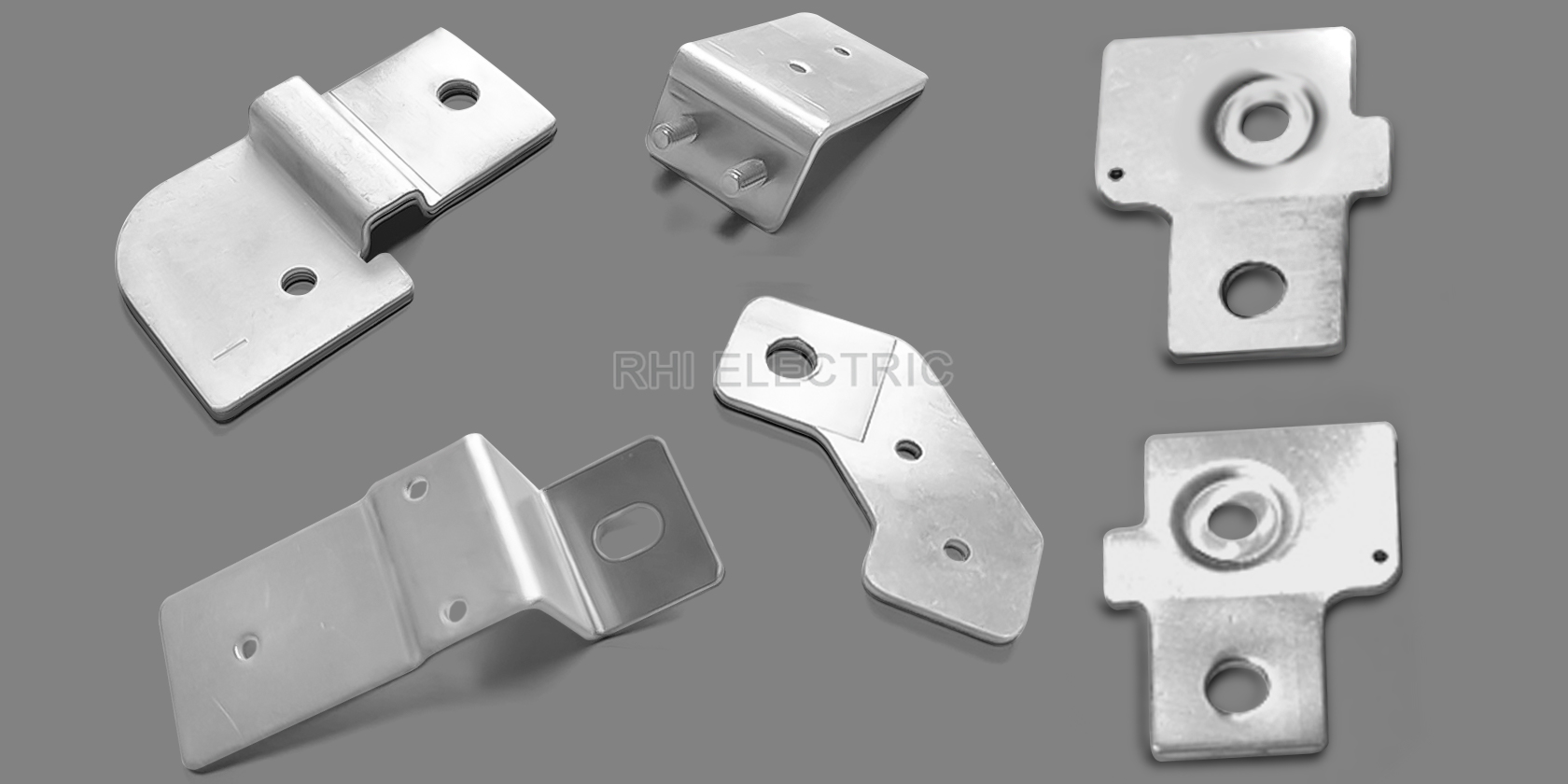
Nickel Laminate Process
Nickel laminate involves attaching a layer of nickel to the surface of copper or aluminium busbars. This method is ideal for aluminium and flexible busbars, commonly used in electric vehicles and energy storage systems.
- Enhanced Corrosion Resistance: Nickel laminate improves corrosion resistance, making busbars suitable for harsh environments.
- Optimized Electrical Conductivity: RHI enhances electrical conductivity by removing oxide layers and optimizing welding parameters to ensure better nickel laminate adhesion.
- Improved Wear Resistance: The nickel laminate's hardness prevents surface damage from mechanical wear.
- Quality Control: RHI ensures high adhesion and surface quality through regular graphite replacement, surface roughness inspection, and precise welding control to avoid misalignment.
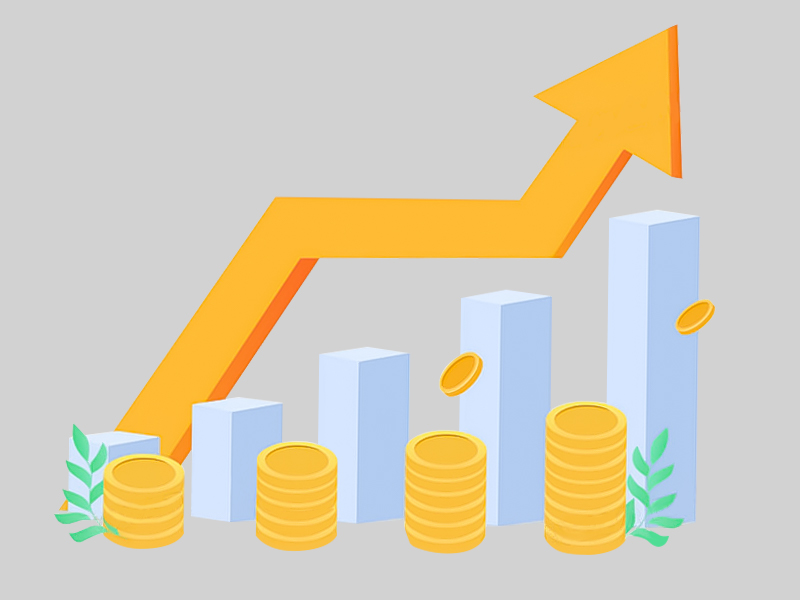
Silver Plating Process
Silver plating involves electroplating a layer of silver to enhance electrical and thermal conductivity.
- High Electrical Conductivity: Silver’s superior conductivity improves electrical transmission, making it ideal for high-performance equipment.
- High Thermal Conductivity: Silver efficiently dissipates heat, suitable for high-current or high-temperature applications.
- Decorative Appeal: Silver plating provides a bright, attractive finish, enhancing the visual quality of products.
- High Cost: Due to silver’s expense, silver plating is used primarily for critical components needing exceptional conductivity.