Enhancing Busbar Quality and Efficiency with APQP & PPAP
As a busbar manufacturer for electric vehicles, RHI understands the critical role of APQP (Advanced Product Quality Planning) and PPAP (Production Part Approval Process) in ensuring quality and meeting customer needs. By applying these methods, we have significantly improved the quality and manufacturability of our busbars, achieving cost reduction and greater efficiency.
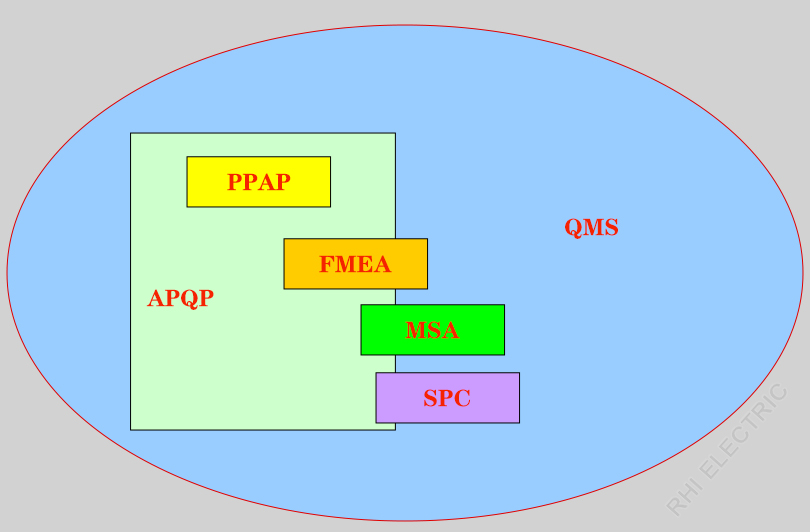
Identifying and Meeting Customer Needs
APQP covers the entire product design and development process, enabling us to identify customer needs and regulatory requirements early. This minimizes later production changes, reducing costs and delays.
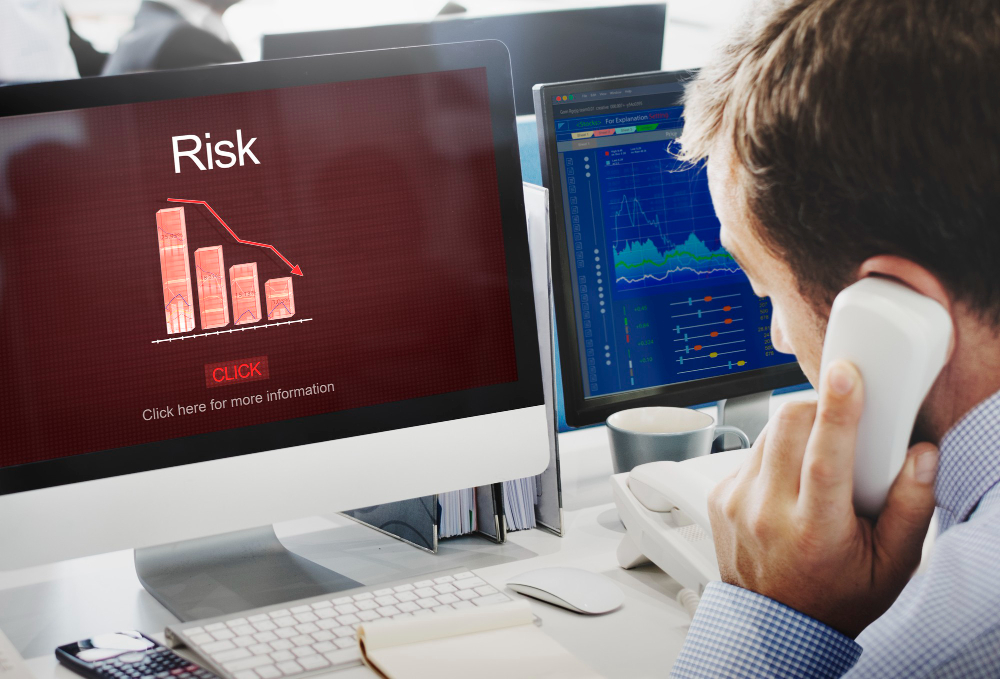
Risk Management
Using FMEA (Failure Mode and Effects Analysis), RHI identifies potential failure modes and implement preventive measures, ensuring high production standards and reducing defects and complaints.
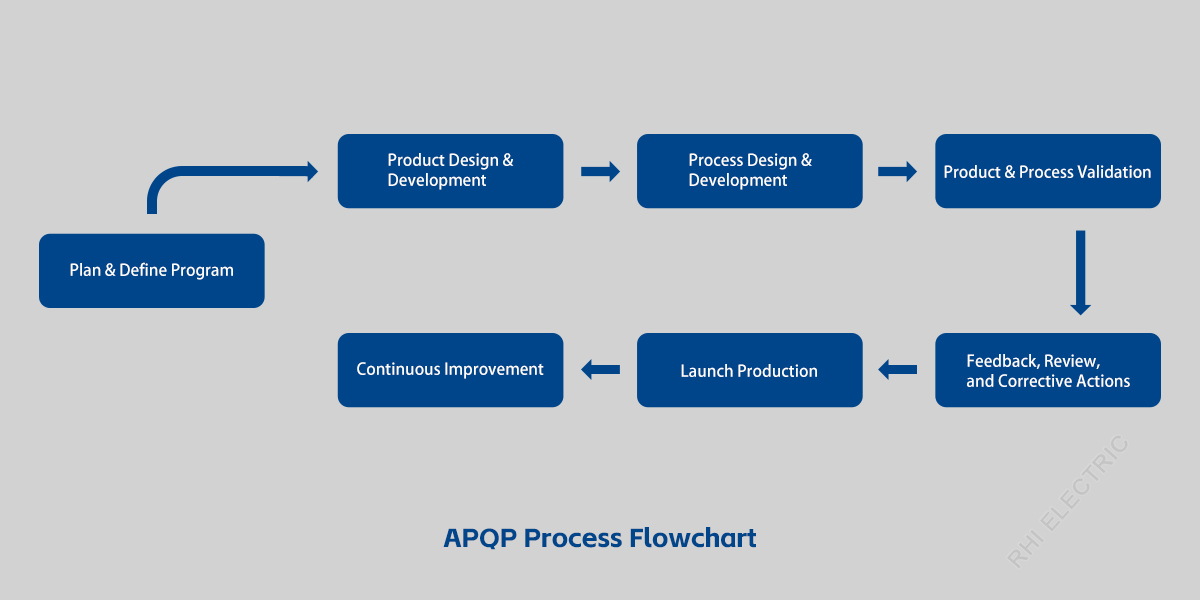
Integration of Quality Tools
APQP incorporates tools like SPC (Statistical Process Control) and MSA (Measurement System Analysis) for real-time monitoring, ensuring consistent product quality and maintaining high standards.
PPAP Application in Busbar Production
1.Ensuring Production Readiness
PPAP confirms our ability to consistently produce compliant products. By preparing detailed PPAP documentation, we demonstrate our risk control measures and ensure alignment with design specifications.
2.Submission and Feedback
RHI submits PPAP documents for customer review to validate production stability. Approval leads to mass production; if not approved, RHI will make necessary improvements and resubmit.
3.Continuous Improvement
APQP provides a framework for quality planning, while PPAP validates production readiness. Together, they enable continuous improvement, quick adaptation to customer needs, shortened development cycles, and reduced costs.
Strategies for Cost Reduction and Efficiency
Considering manufacturability during design improves production efficiency, reduces waste, ensures consistency, and shortens delivery times.
PPAP's strict requirements drive process optimization, waste reduction, and efficiency gains, resulting in lower costs and more competitive pricing.