Optimized Copper-to-Aluminium Busbar Solutions
As a manufacturer specializing in busbars for the new energy sector, RHI understands the importance of transitioning from copper to aluminium busbars for lightweight and cost-effective solutions. Recognizing the unique challenges posed by the differing properties of copper and aluminium, we have developed a comprehensive optimization plan to ensure our copper-to-aluminum busbars meet the highest standards of performance and reliability.
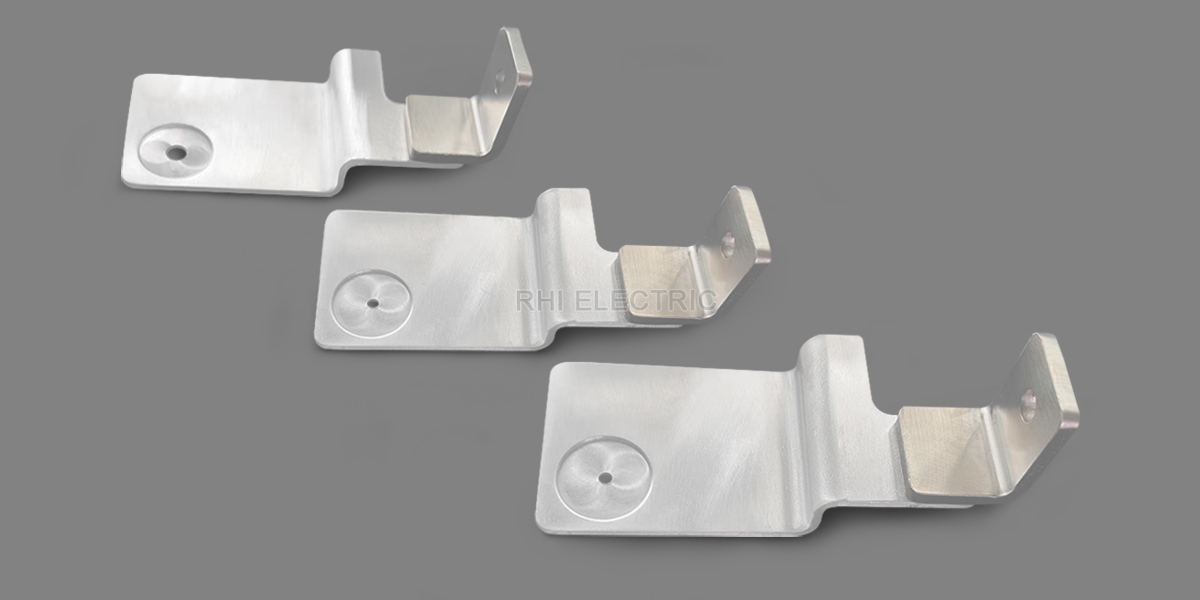
Material Properties and Selection
RHI optimizes material selection by employing advanced copper-to-aluminium techniques and composite materials that integrate both copper and aluminium. This method reduces weight while maintaining excellent busbar conductivity and fatigue resistance, meeting the new energy sector's demand for cost optimization solution. Additionally, RHI utilizes surface treatments such as tinning and nickel plating to prevent electrochemical corrosion, ensuring the stability and durability of busbars in harsh environments.
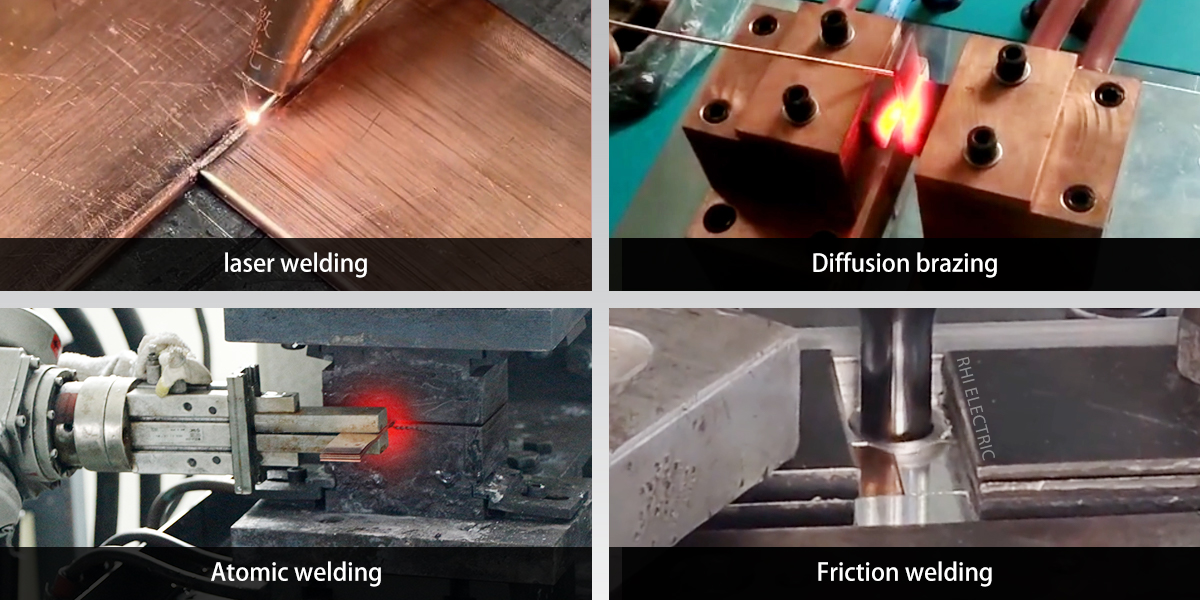
Welding Techniques
Welding copper to aluminium presents challenges due to their differing melting points. To address this, RHI employs advanced methods including laser welding, diffusion brazing, atomic welding, and friction welding. These techniques resolve issues such as brittle interfaces, porosity, and electrochemical corrosion by optimizing parameters, adding intermediate layers, and refining processes. This ensures strong welds, good electrical conductivity, and long-term stability for copper-to-aluminum busbars, thereby enhancing product quality and reliability while reducing costs and weight.
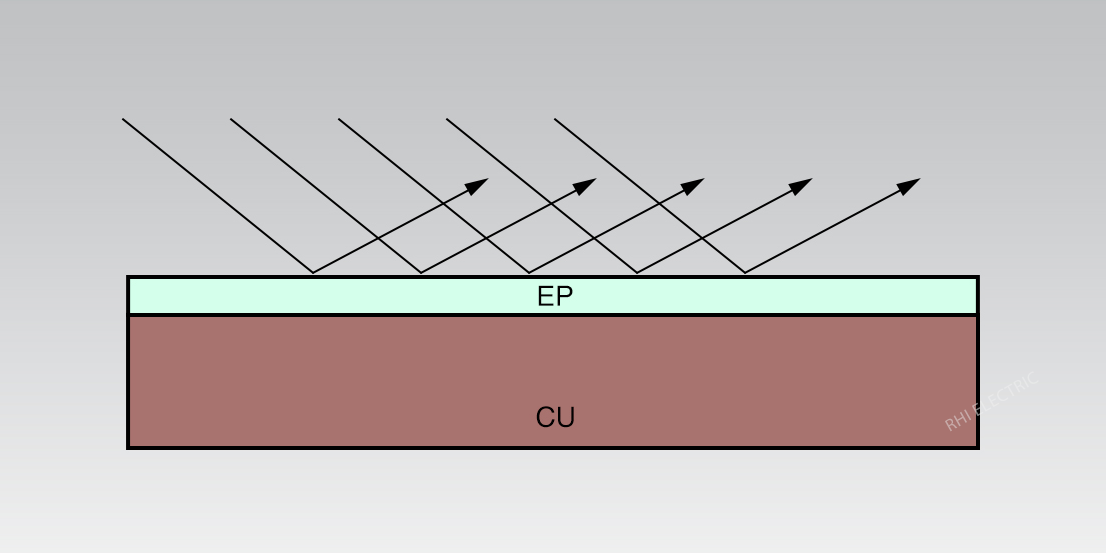
Interface Connection and Surface Treatment
RHI employs a variety of surface treatment processes to enhance the interface connections of copper-to-aluminium busbars. These include tin plating, nickel plating, nickel laminate, and special coating treatments. These methods increase connection strength at the copper-aluminium interface and effectively prevent electrochemical reactions, protecting the busbars from corrosion in humid environments and extending their service life.
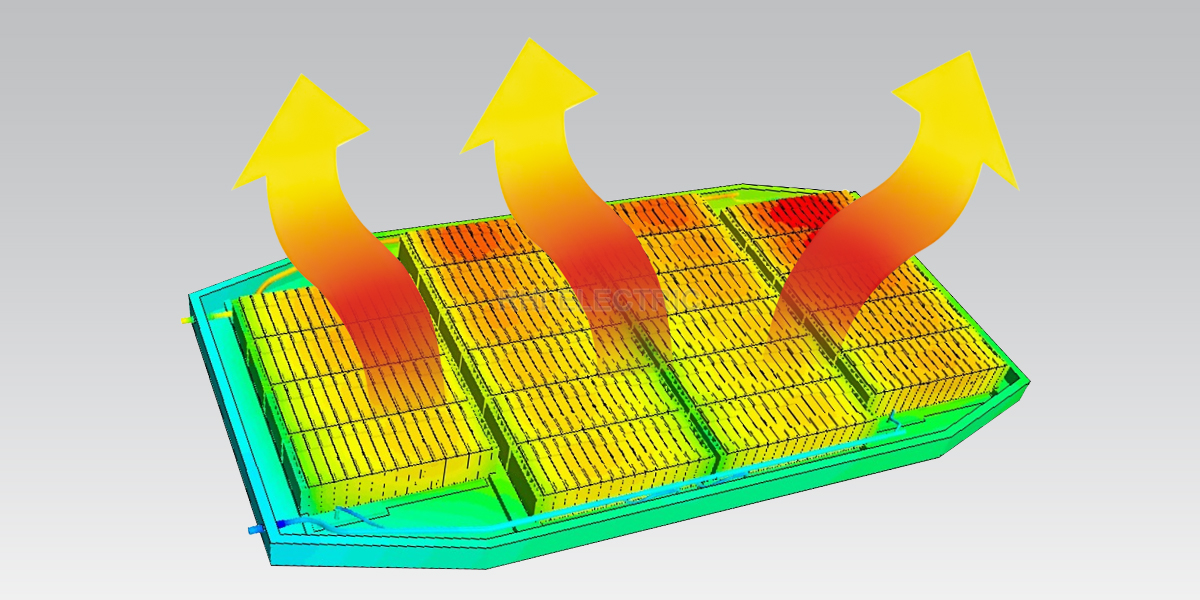
Thermal Management and Heat Dissipation Design
The differing thermal conductivities of copper and aluminium present challenges in thermal management. RHI addresses these issues by optimizing the heat dissipation design of the busbars. By refining structural shapes, using efficient thermal interface materials, and strategically arranging the busbars, RHI achieves uniform temperature distribution and effective heat dissipation. This optimization prevents overheating, enhancing the reliability and stability of busbars under high load conditions.
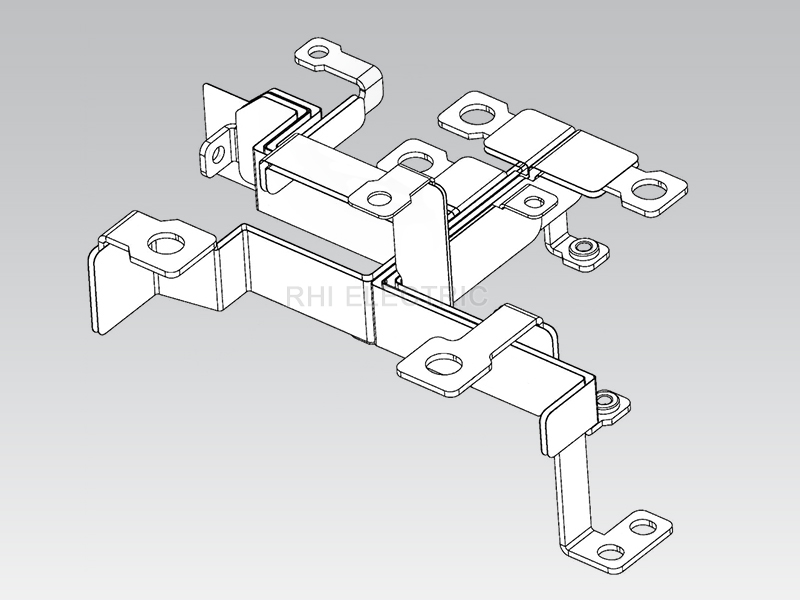
Structural Optimization Design
Our approach to structural optimization involves designing busbars with a hollow structure to reduce material waste and redundancy. This design minimizes overall weight while maintaining strength and conductivity. Additionally, by segmenting busbars into multiple modules, RHI simplifies production and assembly processes and allows for customization of module sizes and functions to meet specific requirements, thus optimizing overall performance and adaptability.
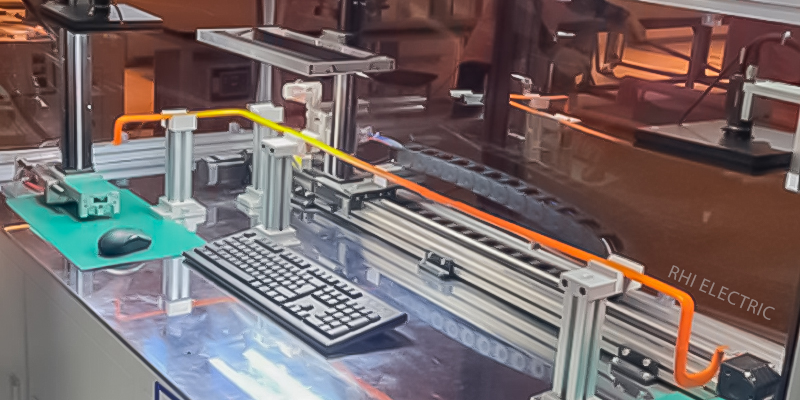
Quality Control and Testing
RHI has implemented rigorous quality control measures using advanced CCD detection equipment and automated quality inspection systems. These systems provide comprehensive monitoring of the production process, ensuring strict control over welding quality, surface treatment effects, and electrical performance. By conducting contact resistance and pull-off force tests, RHI ensures each batch of products meets stringent design standards and customer requirements, thereby enhancing product reliability and customer satisfaction.