

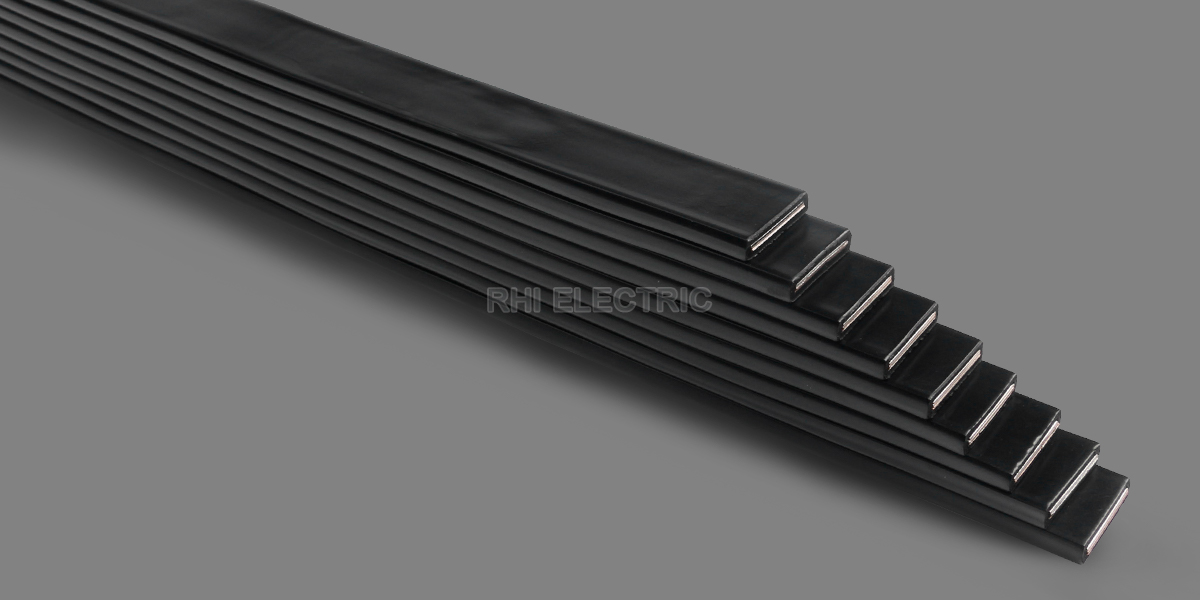
Extrusion Process
The extrusion molding process plays a key role in producing busbars for new energy applications, applying an insulating layer to exposed copper or aluminum busbars to enhance safety and performance. As battery busbars are used more widely in electric vehicles and energy storage systems, choosing suitable insulation materials and extrusion techniques becomes essential.
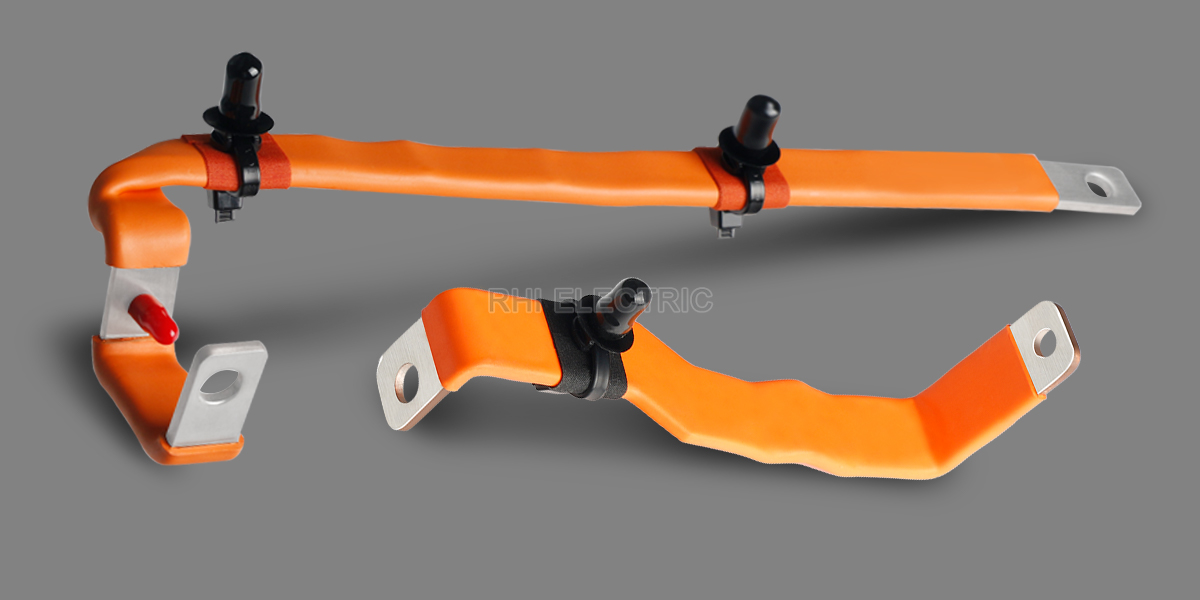
Insulation Process
The insulation process is crucial in busbar manufacturing, ensuring safe isolation to prevent electrical faults, enhance durability, and meet environmental and performance standards. RHI utilizes various insulation techniques to deliver optimal electrical insulation, thermal resistance, and protection against moisture, chemicals, and physical wear.
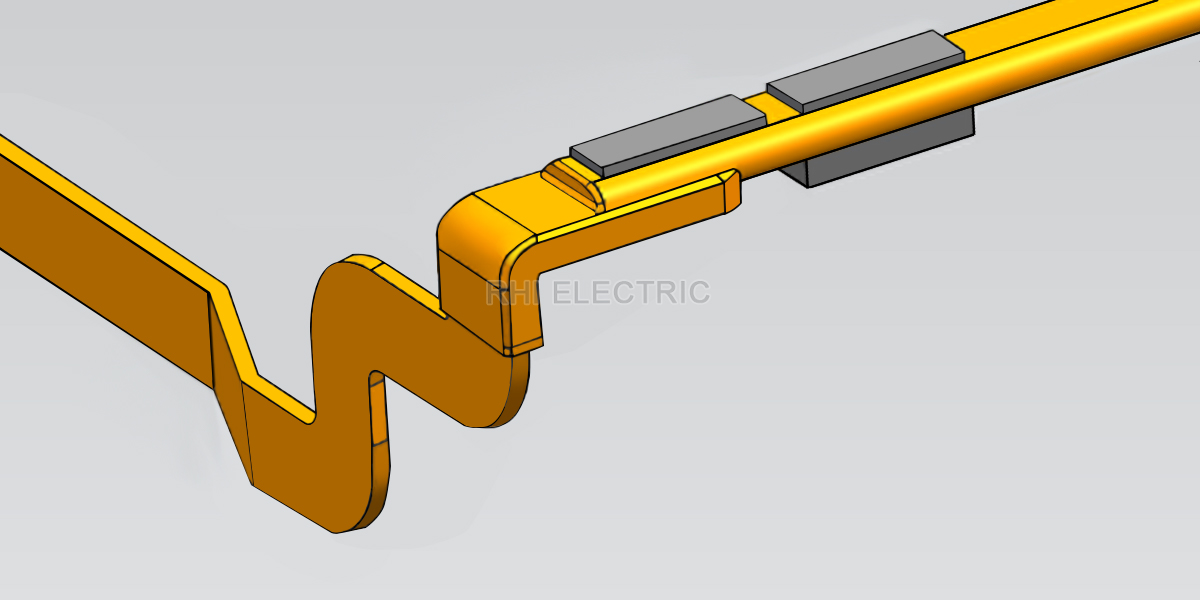
Welding Process
The welding process is essential in manufacturing busbars and electrical components, providing strong mechanical and electrical connections. RHI utilizes various welding techniques to create reliable joints between busbar components, enhancing their performance in electrical distribution systems.
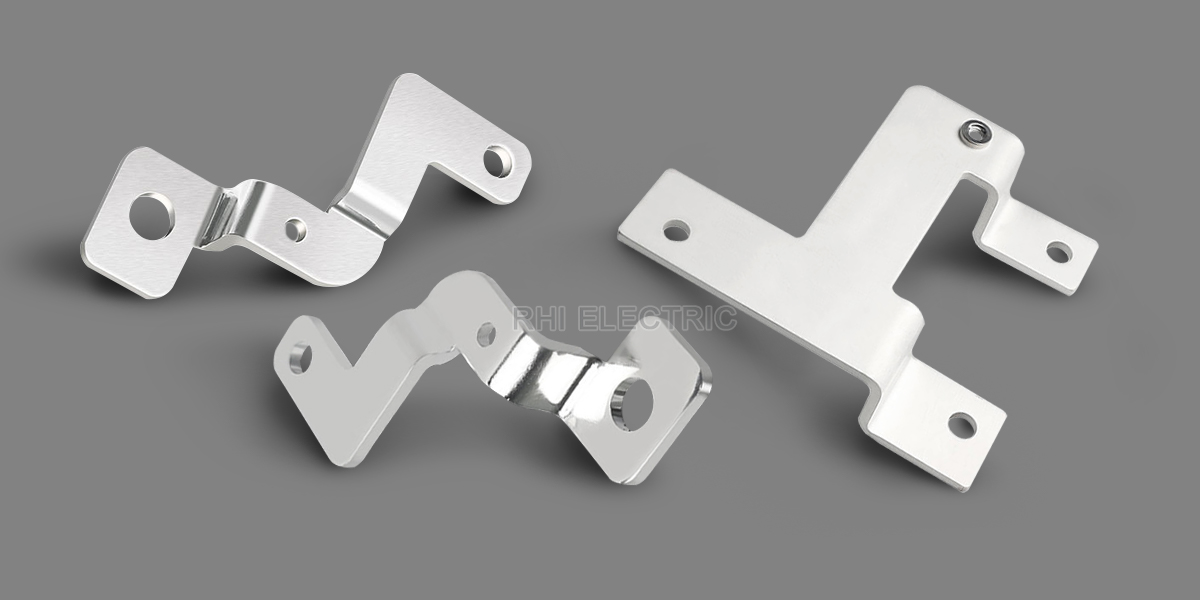
Electroplating Process
As a top manufacturer of new energy busbars, RHI provides a variety of premium surface treatment options to suit diverse application requirements. These treatments include nickel plating, tin plating, silver plating, and nickel sheet application—each offering distinct advantages and specialized properties.
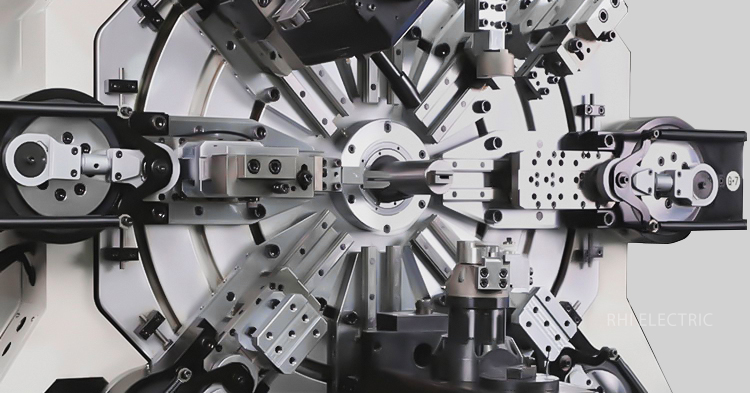
Bending Process
In the new energy sector, the bending process of busbars is vital to the quality and performance of the final product. As essential elements for electrical energy transmission, the precision in manufacturing battery busbars directly affects the electrical performance and reliability of the entire system. RHI employs cutting-edge bending technologies and equipment to ensure that every product complies with stringent industry standards.