

Optimized Busbar Solutions: Preventing EV Thermal Runaway
As electric vehicles rapidly expand in global markets, battery safety has become a focal point of industry concern. Thermal runaway, in particular, poses a significant challenge to the safety of electric vehicles. As a leading busbar manufacturer, RHI provides reliable solutions through a series of optimized production technologies designed to prevent battery thermal runaway and ensure vehicle safety under extreme conditions.
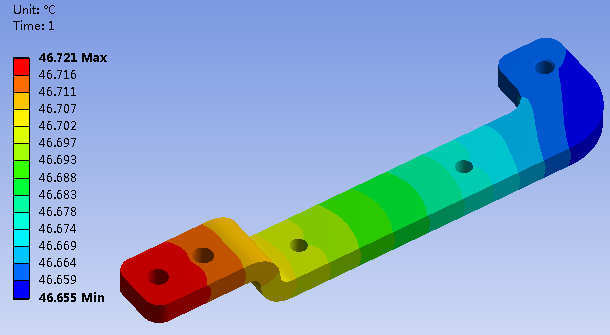
Thermal Runaway Prevention Design Overview
Thermal runaway is a chain reaction caused by internal short circuits, overcharging, or mechanical damage to battery cells, leading to a sudden spike in temperature. This process can cause battery materials to decompose, generating large amounts of heat and gas, potentially resulting in fires or explosions. Effective thermal runaway prevention in battery packs is crucial, focusing on inhibiting its occurrence and quickly dissipating heat when necessary to prevent catastrophic spread.
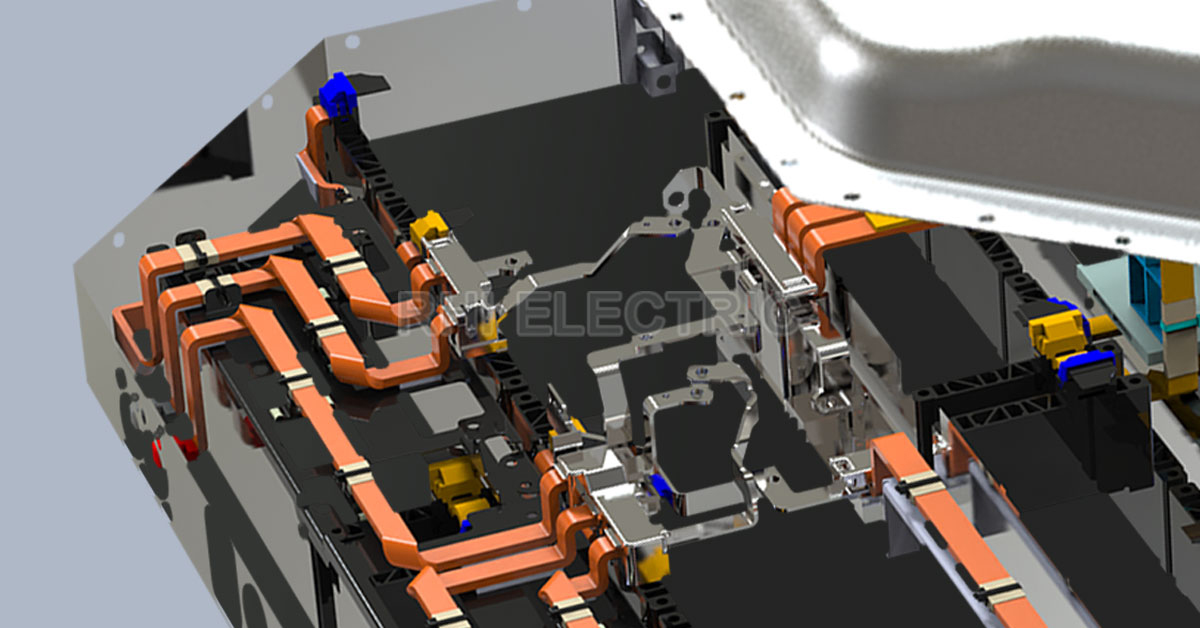
Busbars' Critical Role in Thermal Runaway Prevention
Copper or aluminium busbars are not only core conductive components within EV battery packs but also play a vital role in thermal management. With efficient current transmission and excellent thermal conductivity, electrical busbars are tasked with rapidly dissipating heat and conducting it away from battery cells, making them a key safeguard against thermal runaway.
Optimized Production Techniques for Busbars
To further enhance the performance of copper or aluminium busbars, RHI implements the following optimized techniques in production, aimed at improving both conductivity and thermal management to ensure stable operation even under extreme conditions.
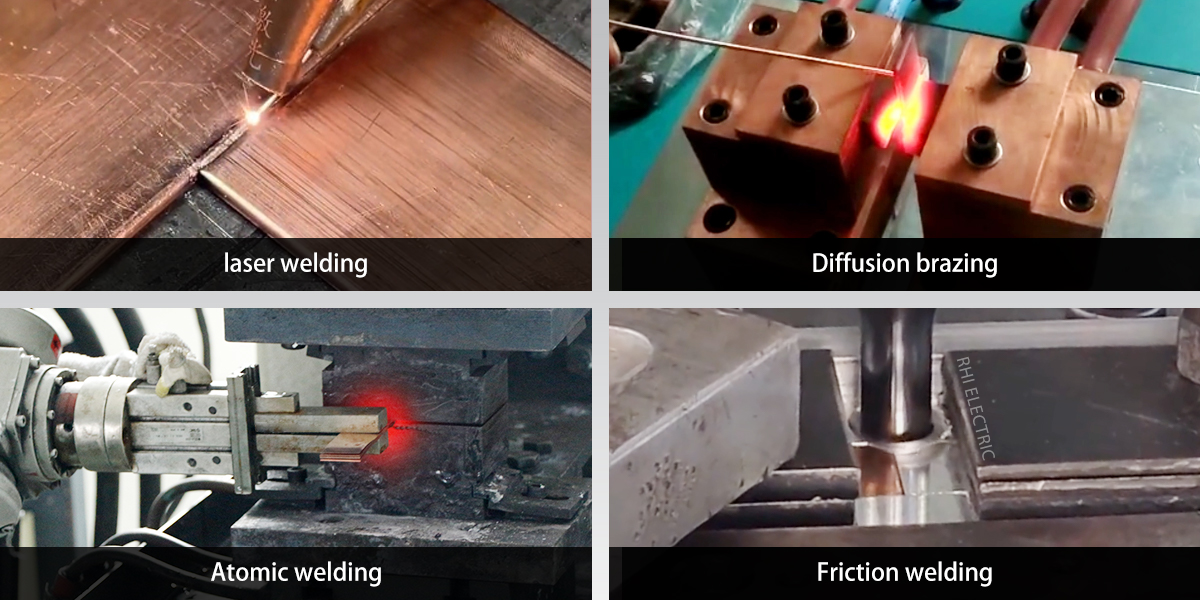
Precision Welding: Optimizing Busbar Connections
In busbar production, the precision of welding techniques is critical. RHI employs laser welding and diffusion welding technologies to ensure uniform and robust connections at busbar interfaces. This precision welding enhances both the electrical conductivity and thermal performance of the busbars, effectively preventing overheating caused by excessive localized resistance.
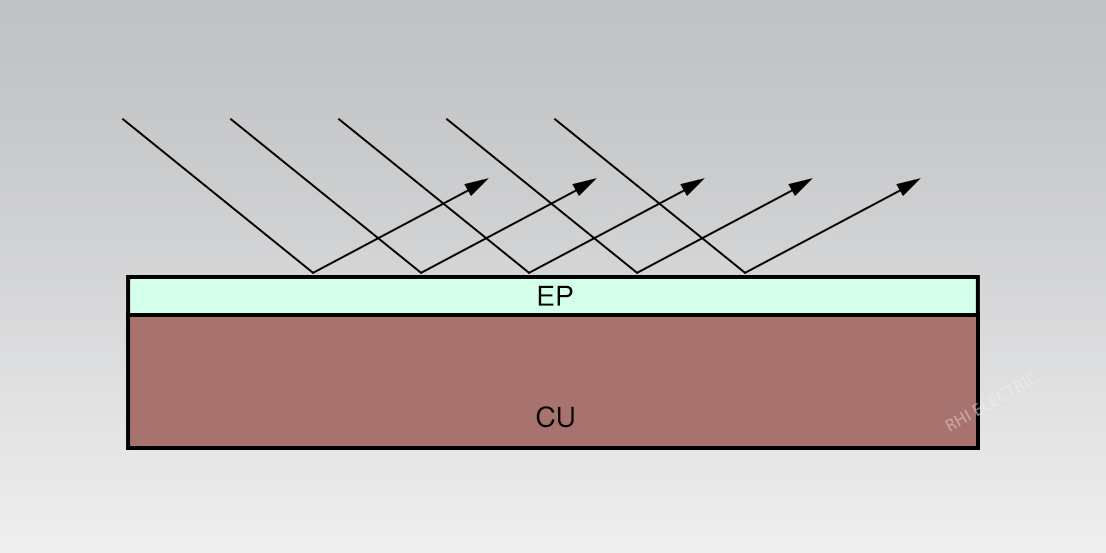
Surface Treatment & Insulation: Enhancing Oxidation and Heat Resistance
The surface treatment of battery busbars directly impacts their stability in high-temperature environments. RHI utilizes anodizing and electroplating processes to improve oxidation resistance and extend the lifespan of the busbars. Additionally, high-temperature-resistant insulation materials are applied to the busbars to prevent short circuits and thermal leakage, ensuring safe and reliable performance in high-temperature conditions.
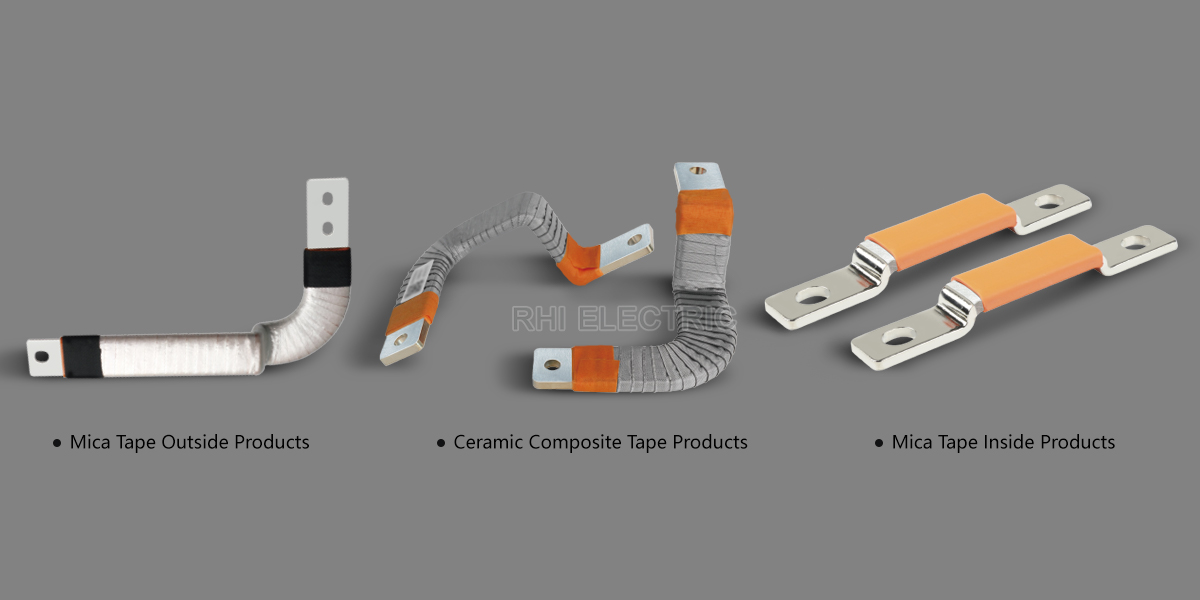
Mica and Busbar Integration
In modern battery pack design, mica materials, known for their excellent insulation and high-temperature resistance, are widely used in vehicles such as the Model S Plaid, Ningde's second-generation CTP, and BYD Seal's CTB models. The integration of mica tapes with electrical busbars not only enhances thermal runaway prevention but also ensures the safety and conductivity of busbars in high-temperature environments.
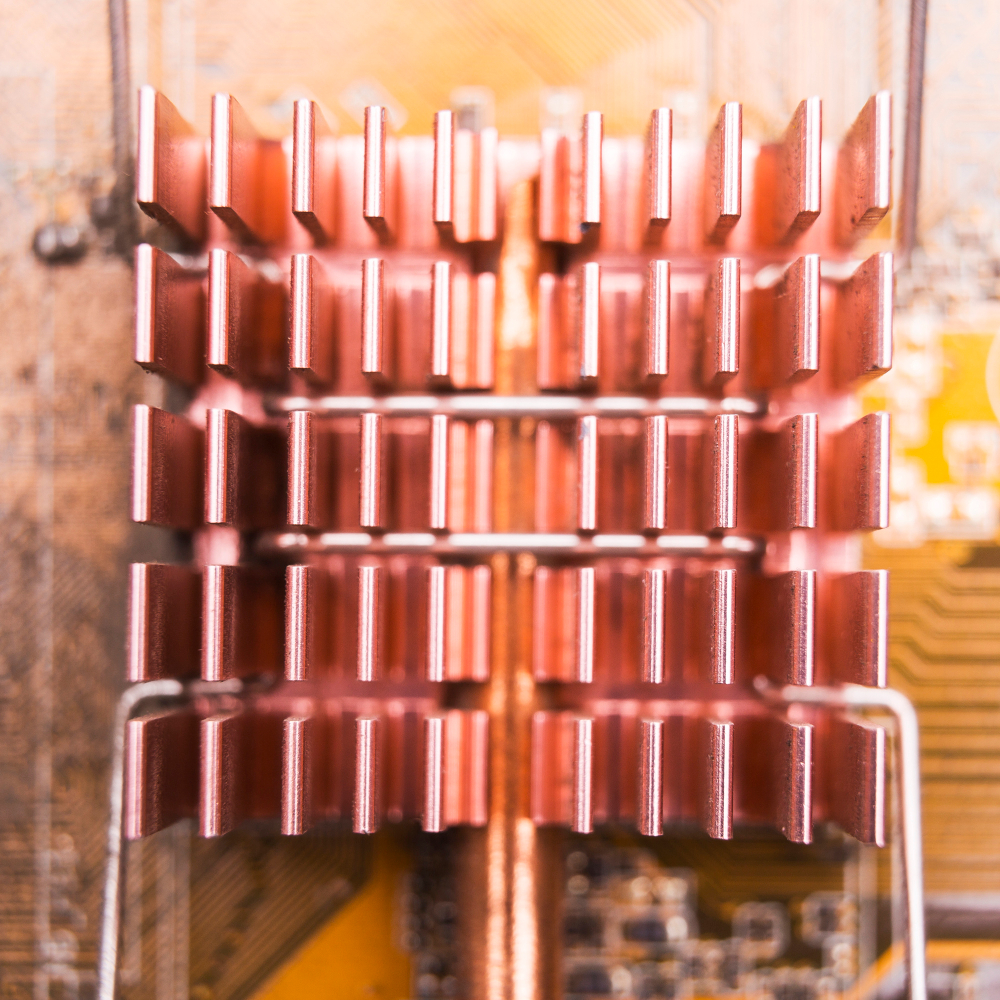
High-Purity Conductors: Enhancing Busbar Performance
High-purity copper and aluminium enhance busbar conductivity and reduce heat generation. RHI’s optimized conductor selection and lightweight copper-to-aluminium designs minimize thermal resistance, lowering the risk of thermal runaway and improving battery pack stability.
Custom Busbars: Solutions for Thermal Runaway Prevention
In the design of electric vehicles, the effective utilization of busbars for thermal management is crucial to preventing thermal runaway. Through scientific layout and design, RHI's custom busbars can rapidly dissipate heat generated by battery cells and work in coordination with other thermal management components to prevent dangerous heat concentration.
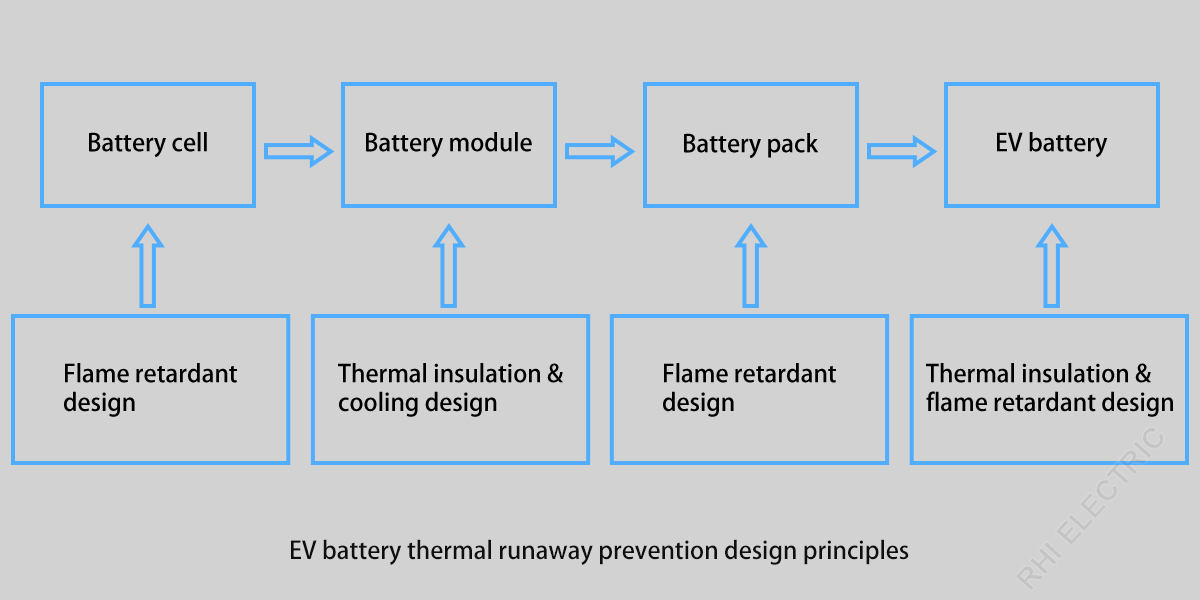
Thermal Isolation Design: Preventing Heat Spread
By combining with thermal resistance materials, electrical busbars can form effective thermal isolation structures within battery packs. When a battery cell exhibits abnormal temperature rises, this design prevents heat from spreading to adjacent cells, reducing the likelihood of a chain reaction and lowering the risk of thermal runaway.
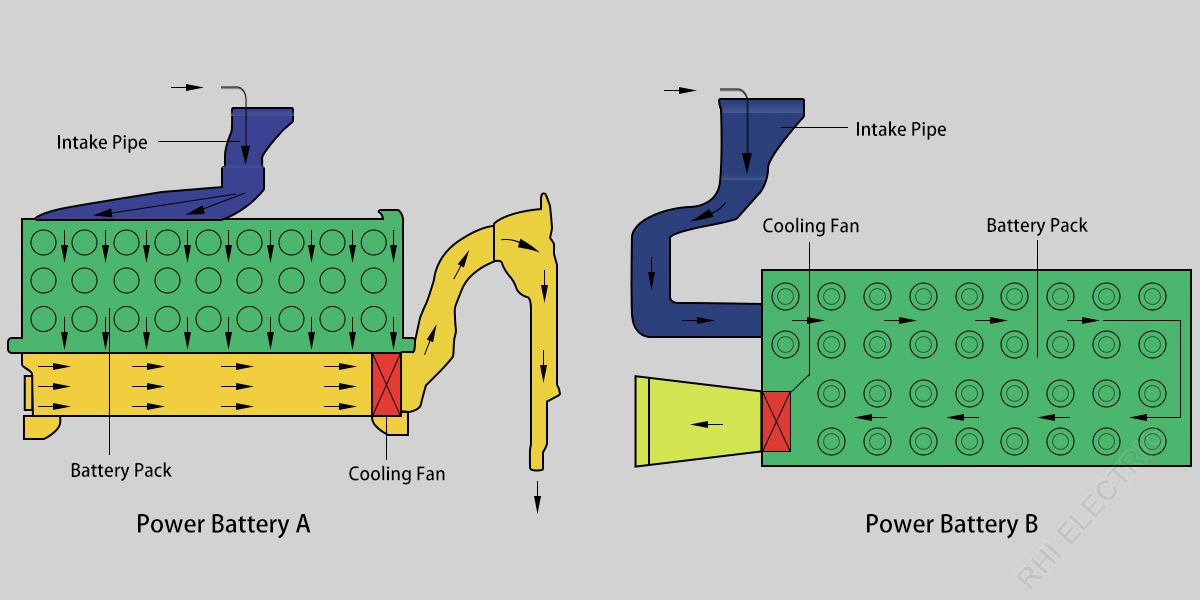
Cooling System Integration: Improving Thermal Management Efficiency
The close integration of busbars with the Battery Management System (BMS) and cooling devices is key to improving the safety of battery packs. RHI's busbar design seamlessly integrates with the BMS, facilitating precise heat conduction and dissipation, avoiding localized overheating, and aiding cooling systems in quickly reducing the overall temperature of the battery pack, ensuring the safe operation of electric vehicles.
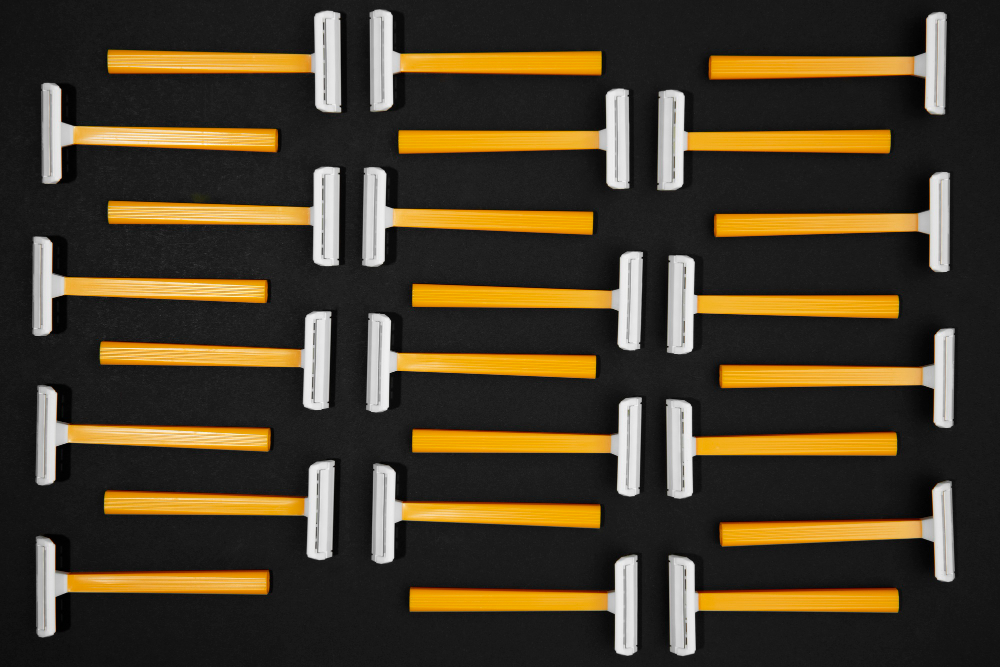
Coordinated Design with Safety Valves
Battery packs are typically equipped with different types of safety valves on the front and rear sides, such as membrane pin-type safety valves and spring-type safety valves, to handle thermal runaway pressures from different directions. In this process, the scientific layout of battery busbars ensures smooth heat and current flow, preventing the accumulation of heat in localized areas and enhancing the overall safety of the system.
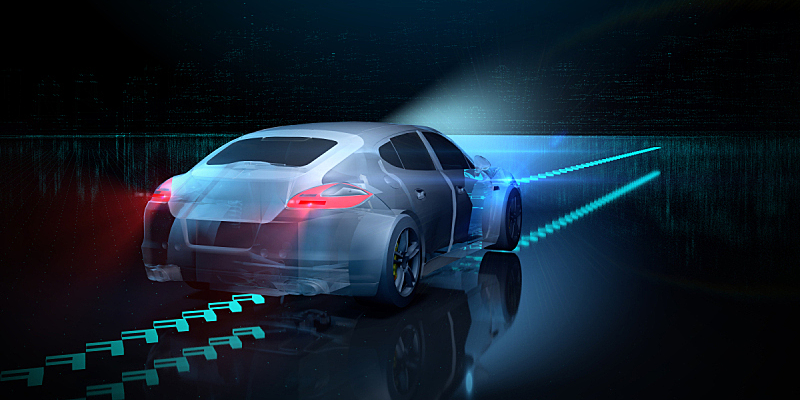
Future Outlook: Ongoing Optimization and Innovation
RHI is dedicated to advancing EV busbar technology through new materials and intelligent solutions. By continuously optimizing production and design, RHI aims to meet growing safety and performance demands, driving forward the electric vehicle industry's safety standards.