

Insulation Solutions for Busbar Electrical
RHI masters the manufacturing process of every step. With fully equipped facilities and a professional R&D team, RHI strictly controls the technical requirements for the insulation layer of the busbar throughout the production process to ensure excellent product quality.
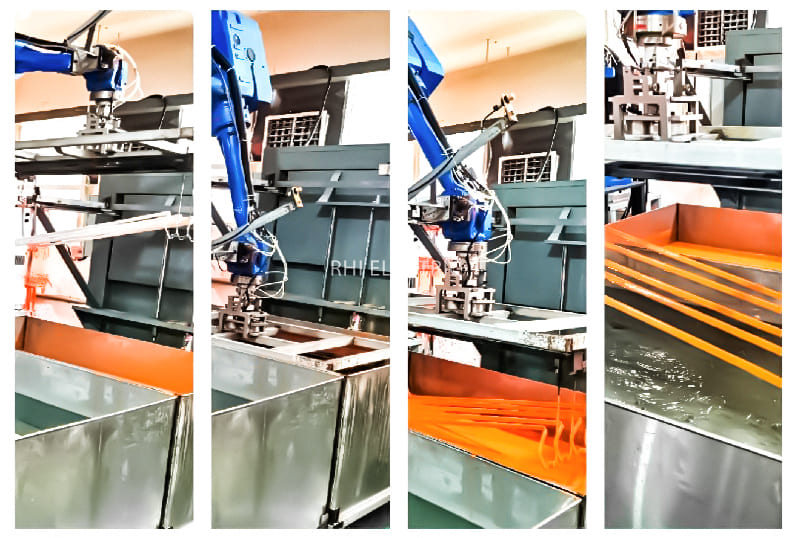
PVC Dipping Insulation Process
The PVC-dipped copper/aluminium busbars can be customized according to customer requirements, including position, color, and voltage resistance. This process can address the issue of insulating unconventional bus bar connectors that cannot be achieved with heat shrink tubing.
The PVC dipping process uses special PVC materials that are heated to a liquid state. A copper busbar is then immersed in this liquid, forming a smooth, uniform insulating layer with strong adhesion.
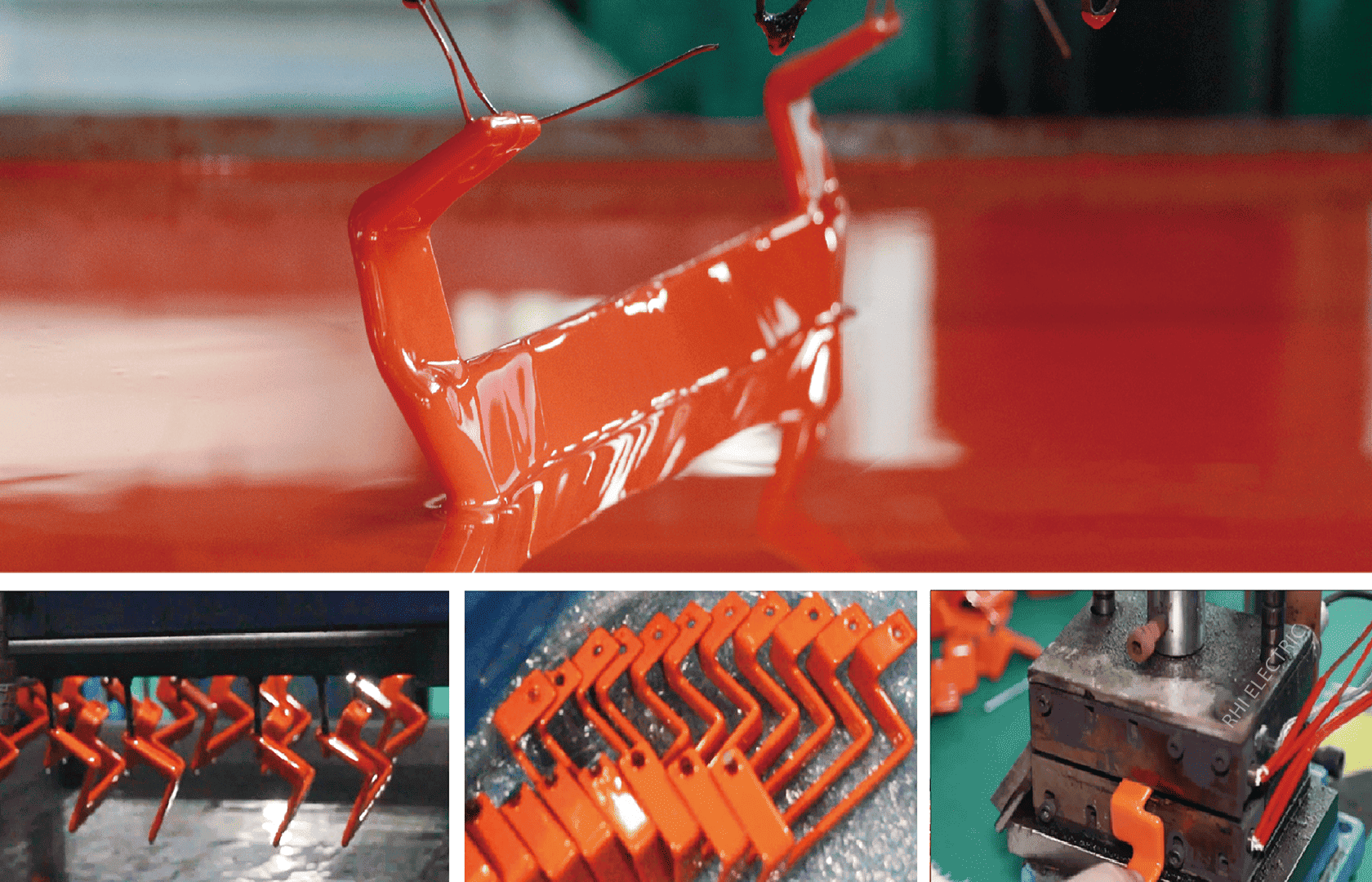
The PVC insulation offers excellent resistance to corrosion, acids, alkalis, salt spray, and is flame retardant. The process allows for customization of the busbar's thickness, color, and voltage resistance according to customer requirements, and the materials used are eco-friendly and available in various colors.
This process is suitable for rigid busbars, and especially for irregularly shaped rigid busbars. Due to its high efficiency, low cost, and ability to enhance the electrical performance of busbars, it is widely used in busbar insulation treatment and facilitates automated production.
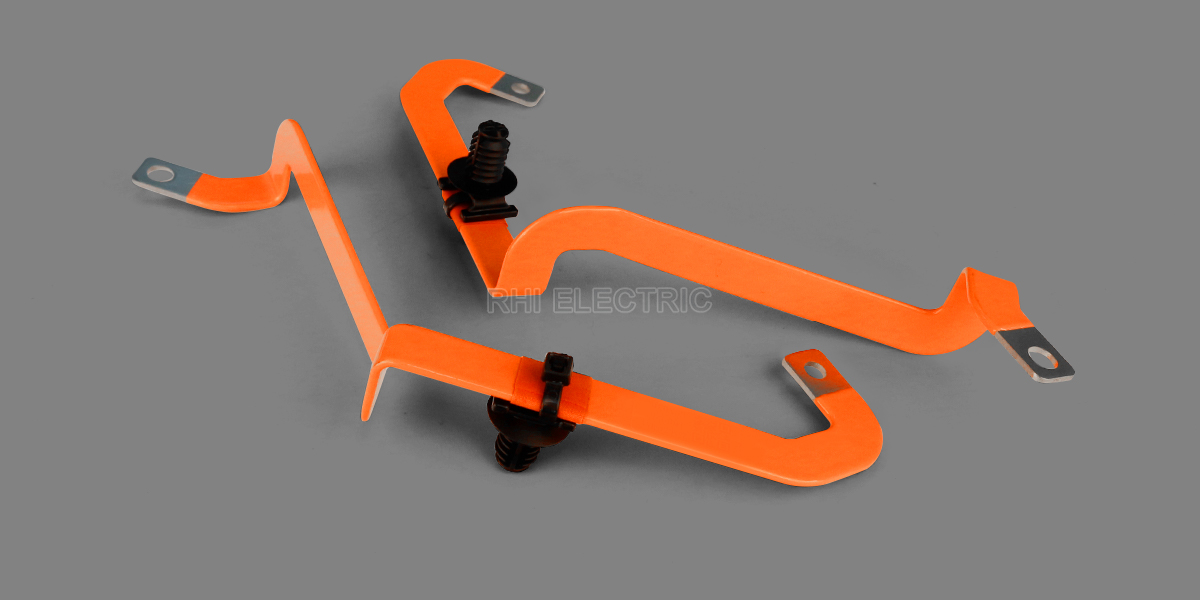
Powder Coating Insulation Process
Advantages:
- Excellent coating adhesion for a smooth, attractive surface
- Strong insulation with excellent moisture-proof sealing
- Ideal for irregular and unconventional busbars, saving space
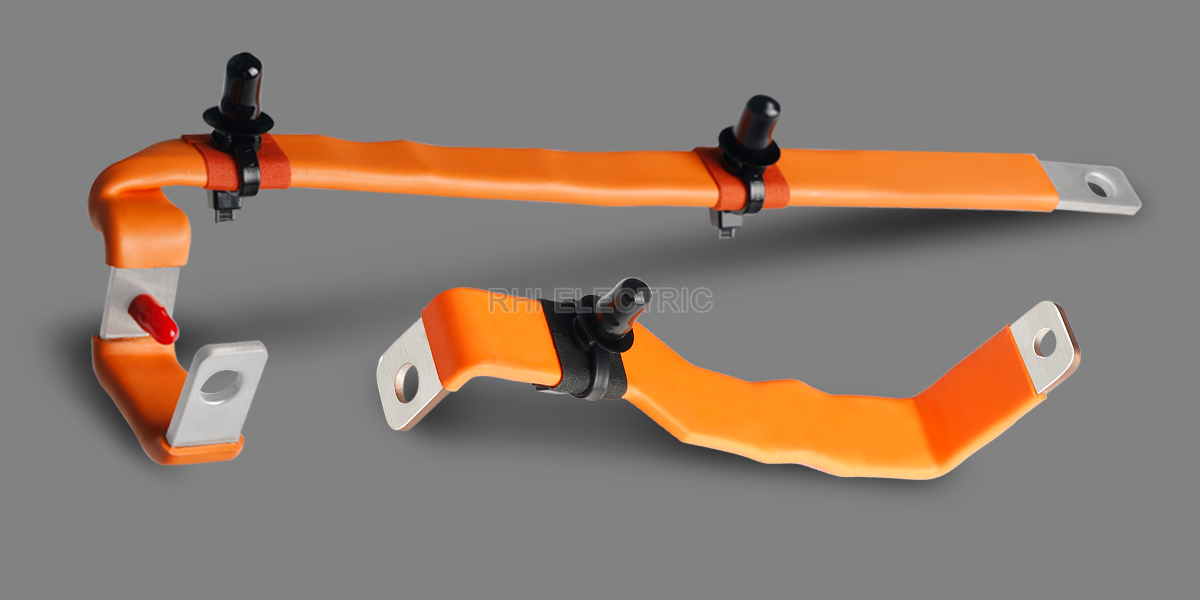
Heat Shrink Tubing Process
Heat shrink insulation tubes can provide excellent insulation, temperature resistance, enhance the mechanical strength of the electric bus bars, and improve their shock resistance.
Heat shrink tubing made of EVA/PE insulation material is applied to the electrical busbar by heating with a heat gun. It has the advantages of high-temperature shrinkage, flexibility, flame resistance, insulation, and corrosion resistance.
Due to its material properties, EVA insulation is generally suitable for low-voltage environments, while PE insulation, with its higher mechanical strength and hardness, is suitable for environments that need to withstand certain pressures or forces.
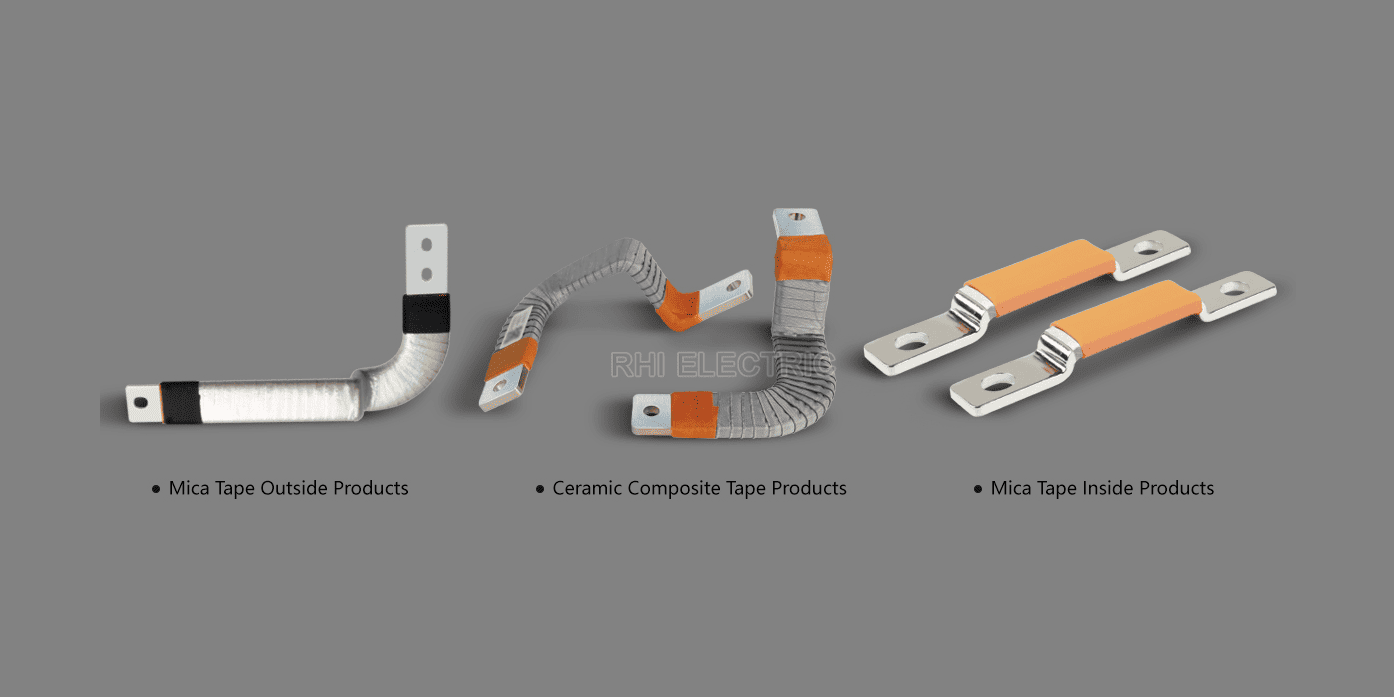
Mica Tape Winding Process
RHI offers advanced high-temperature insulation solutions for the new energy sector using composite mica tape, ceramic composite tape, and ceramic silicone rubber composite tape. These materials perform exceptionally well even after 10 minutes at 1000°C, meeting the 3500V DC withstand voltage requirement, with leakage current under 1mA and insulation resistance of at least 500MΩ at 1000V DC. We provide both flexible and rigid busbar configurations to fit diverse applications.

Our flexible busbars are paired with composite or ceramic composite tapes and processed using advanced automated winding technology, ensuring precise insulation layers and enhanced production efficiency. Our high-performance machinery guarantees consistent winding thickness and reliability.
For rigid busbars, we use mica tape combined with PVC dip coating, suitable for temperatures up to 1200°C. This approach ensures durability and reliability under extreme conditions. By integrating automated winding with high-temperature processing, we provide superior insulation solutions that meet stringent industry standards.