

Injection Molded Busbar: A Comprehensive Guide to Advanced Power Distribution
Delve into the concept of injection molded busbars, their advantages, manufacturing process, applications, and future trends.
Introduction
In modern electrical and electronic systems, efficient power distribution is critical to performance, reliability, and safety. The injection molded busbar has emerged as a revolutionary technology in power distribution, offering superior insulation, compact design, and enhanced durability compared to traditional busbars. This article delves into the concept of injection molded busbars, their advantages, manufacturing process, applications, and future trends.
What is an Injection Molded Busbar?
An injection molded busbar is a power distribution component that combines a conductive metal busbar with a molded insulating layer, typically made from high-performance thermoplastics or thermosetting materials. Unlike conventional busbars that rely on external insulation materials such as heat-shrink tubing, epoxy coatings, or rigid plastic covers, injection molding allows for precise encapsulation of the conductive elements, providing uniform protection and mechanical stability. This technology improves safety, reliability, and efficiency in electrical power systems, making it a preferred choice in various industries.
Advantages of Injection Molded Busbars
The adoption of injection molded busbars in various industries is driven by several key benefits:
1. Enhanced Electrical Insulation
Injection molding enables the use of high-dielectric strength materials, reducing the risk of electrical arcing and short circuits. The uniform insulation layer eliminates weak points found in traditional insulation methods, ensuring consistent and reliable protection in high-voltage applications.
2. Compact and Lightweight Design
By integrating insulation directly into the busbar, the overall footprint is minimized, allowing for space-saving designs in electrical enclosures and battery systems. This is particularly beneficial in electric vehicles (EVs), aerospace applications, and compact industrial machinery where space is limited.
3. Improved Thermal Management
Injection molded materials can be engineered for superior heat dissipation, helping maintain optimal operating temperatures and reducing the likelihood of overheating in high-current applications. This enhances the longevity and performance of electrical systems.
4. Increased Mechanical Durability
The molded insulation provides mechanical reinforcement, making the busbar resistant to vibrations, mechanical shocks, and environmental factors like moisture, dust, and corrosive elements. This is particularly valuable in harsh industrial and automotive environments.
5. Cost Efficiency in Mass Production
Once the mold is created, injection molding allows for rapid, consistent, and scalable production, reducing labor costs associated with manual insulation techniques. The automation of the process ensures minimal material waste and high production efficiency.
The Injection Molding Process for Busbars
The manufacturing process of an injection molded busbar involves several key steps:
Step 1: Design and Material Selection
- Conductive Material: Typically, copper or aluminum is used due to its high conductivity, lightweight nature, and corrosion resistance.
- Insulation Material: Advanced thermoplastics (e.g., polyamide, PBT, PPS) or thermosets (e.g., epoxy resins) are selected based on dielectric strength, heat resistance, and environmental durability.
- Design Considerations: Engineers optimize busbar shape, insulation thickness, and electrical clearance to meet specific application requirements.
Step 2: Busbar Fabrication
The conductive metal is shaped through processes such as stamping, bending, or CNC machining to meet electrical and mechanical specifications.
Surface treatment and plating (e.g., tin, silver, or nickel) are applied to enhance corrosion resistance, conductivity, and longevity.
Step 3: Injection Molding Process
The pre-formed busbar is placed inside a mold cavity designed to encapsulate the conductive structure.
Molten plastic or resin is injected into the mold under high pressure, ensuring full encapsulation and adhesion to the busbar.
The part is cooled, solidified, and ejected from the mold.
Step 4: Post-Processing and Quality Control
Excess material is trimmed, and surface finishing is performed to ensure smooth insulation coverage.
Electrical and mechanical testing is conducted to verify insulation integrity, dielectric strength, thermal performance, and dimensional accuracy.
Additional protective coatings or labeling may be applied for identification and durability enhancement.
Applications of Injection Molded Busbars
Injection molded busbars are used in various industries where reliable and efficient power distribution is essential:
1. Electric Vehicles (EVs) and Hybrid Cars
Utilized in high-voltage battery modules, power distribution units (PDUs), and inverters.
Reduces overall vehicle weight while enhancing energy efficiency and safety.
Provides reliable insulation in demanding automotive environments.
2. Renewable Energy Systems
Applied in solar inverters, wind turbine power electronics, and battery energy storage systems.
Enhances durability in outdoor environments exposed to extreme temperatures, humidity, and UV radiation.
Contributes to higher efficiency and longevity of renewable energy infrastructure.
3. Industrial Power Systems
Deployed in switchgear, motor control centers (MCCs), and uninterruptible power supplies (UPS).
Offers reliable insulation and space-saving designs in high-voltage industrial applications.
Provides enhanced mechanical stability for long-term performance.
4. Aerospace and Defense
Utilized in aircraft power distribution networks and military-grade electronic systems.
Lightweight and high-reliability solutions designed to withstand extreme environmental conditions.
Provides robust electrical insulation for mission-critical applications.
5. Consumer Electronics and Data Centers
Used in high-efficiency power supplies, server racks, and compact electronic devices.
Helps manage power distribution while minimizing space usage and weight.
Enhances energy efficiency and thermal performance in compact electronic enclosures.
Future Trends in Injection Molded Busbars
The evolution of injection molded busbars is being shaped by advancements in materials, automation, and emerging applications:
1. Smart and IoT-Enabled Busbars
Integration of embedded sensors for real-time temperature, voltage, and current monitoring.
Enables predictive maintenance, optimizing performance and reducing downtime in industrial applications.
2. Advanced Insulation Materials
Development of high-temperature, flame-retardant, and self-healing polymers for improved safety and longevity.
Introduction of eco-friendly, recyclable materials to support sustainable manufacturing initiatives.
3. 3D Printing and Additive Manufacturing
Exploration of 3D printing for rapid prototyping and customized busbar geometries.
Reduces tooling costs and enables flexible, small-batch production for specialized applications.
4. Increased Adoption in High-Voltage Applications
Expansion into high-voltage DC (HVDC) power transmission systems and grid-scale battery storage.
Enhanced insulation techniques to support higher energy densities and power demands.
Conclusion
The injection molded busbar represents a major leap forward in electrical power distribution, offering enhanced insulation, compact design, and superior reliability. Its applications in EVs, renewable energy, and industrial power systems continue to grow, driven by advancements in material science and manufacturing techniques. As the demand for efficient and compact power distribution solutions increases, injection molded busbars are poised to play a crucial role in the future of electrical engineering.
By understanding the benefits and evolving trends of this technology, industries can leverage injection molded busbars to achieve safer, more efficient, and cost-effective power solutions.
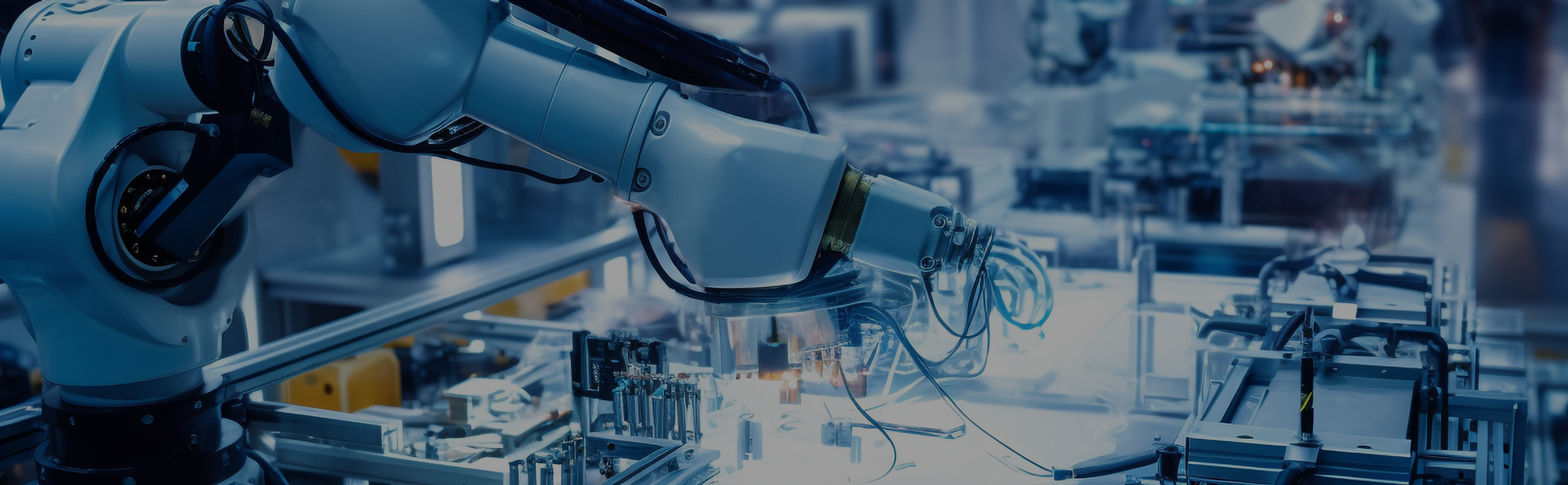