

Rigid Aluminium Busbar: The Ultimate Guide to Applications, Advantages, and Design Tips
Help you fully understand the ins and outs of rigid aluminium busbars, their applications, design considerations, installation tips, challenges, and why they are becoming the go-to solution for engineers and power system designers worldwide.
Introduction
In today’s rapidly advancing world of electrical power distribution, efficiency, cost, and reliability are more critical than ever. Power systems must meet the rising demands of industries, renewable energy facilities, commercial buildings, and transportation networks. Among the components shaping modern power systems, the Rigid Aluminium Busbar has emerged as a key player. This component offers a combination of lightweight design, excellent conductivity, and cost-effectiveness compared to its traditional copper counterpart. Rigid aluminium busbars are now widely accepted and integrated into both new and retrofit electrical systems, offering engineers flexibility and performance without compromising quality.
Whether you are dealing with industrial electrical installations, renewable energy systems, or large-scale commercial projects, rigid aluminium busbars are gaining traction due to their impressive versatility and ability to meet stringent electrical and mechanical requirements. This comprehensive guide will help you fully understand the ins and outs of rigid aluminium busbars, their applications, design considerations, installation tips, challenges, and why they are becoming the go-to solution for engineers and power system designers worldwide.
What is a Rigid Aluminium Busbar?
A rigid aluminium busbar is a solid, flat or shaped conductor made primarily from aluminium, designed to carry substantial electrical currents safely and efficiently in power distribution systems. Unlike flexible conductors, rigid busbars maintain their shape and structure under mechanical stress, ensuring reliability and reducing maintenance over time. They are available in various sizes and shapes to suit different installation environments and electrical load requirements.
Composition and Types
Rigid aluminium busbars are primarily manufactured using high-purity aluminium (99.7% or higher), ensuring good electrical conductivity and excellent mechanical properties. Depending on project requirements, they can be produced in different shapes such as:
- Flat bars: Common for general applications
- T-shaped: Used in space-saving or stacked busbar configurations
- L-shaped: For corner or compact installations
- Custom profiles: Designed specifically for specialized equipment
Coating Types:
- Bare aluminium: Standard choice for indoor installations
- Tin-plated: Offers enhanced protection against oxidation and galvanic corrosion
- Anodized: Provides an additional oxide layer, improving corrosion resistance and insulation properties
Rigid Aluminium vs Copper Busbar
Copper busbars have traditionally been preferred due to their superior conductivity, but aluminium busbars offer about 61% of copper's conductivity at less than one-third of its weight and approximately half the cost. For projects where weight reduction, cost savings, and sustainability are important, aluminium is the ideal alternative. When properly sized, aluminium busbars can perform comparably to copper while offering long-term cost and environmental benefits.
Manufacturing Standards
Rigid aluminium busbars are produced according to international and regional standards such as ASTM B317, IEC 61089, and GB/T 5585. Compliance with these standards guarantees consistent conductivity, mechanical strength, and corrosion resistance, providing engineers confidence in long-term system reliability.
Applications of Rigid Aluminium Busbars
Rigid aluminium busbars are used in a variety of critical applications due to their ability to efficiently carry large electrical currents and withstand mechanical stress. Some of the most common areas where rigid aluminium busbars are indispensable include:
1. Power Distribution Systems
In traditional power distribution systems, rigid aluminium busbars are used to interconnect switchgear, transformers, and distribution boards. They are the backbone of:
Switchgear assemblies
Medium and high-voltage substations
Low-voltage distribution panels Their mechanical rigidity and ability to carry high currents make them suitable for both indoor and outdoor installations.
2. Renewable Energy Systems
As the world shifts towards sustainable energy, aluminium busbars have become vital in renewable installations:
Solar photovoltaic plants: Used in inverter stations, DC/AC cabinets, and power transmission lines
Wind power systems: Employed in wind turbine towers, nacelles, and substations Their lightweight and corrosion-resistant properties are especially advantageous in outdoor and remote renewable energy projects.
3. Industrial Electrical Installations
In industrial environments where reliability and durability are crucial, rigid aluminium busbars provide safe and efficient current distribution for:
Manufacturing plants
Heavy-duty machinery
Automated production lines They are preferred for environments where ease of installation and maintenance reduces downtime.
4. Electric Vehicles (EVs) and Charging Infrastructure
The rapid growth of the EV market has fueled the need for reliable power distribution within:
EV battery modules
High-speed EV charging stations Aluminium busbars help reduce vehicle weight and improve charging station efficiency without compromising performance.
Advantages of Rigid Aluminium Busbars
1. Lightweight and Cost-Effective
Aluminium's low density reduces weight by up to 66% compared to copper, simplifying transportation, handling, and installation. Lower raw material costs contribute significantly to overall budget savings.
2. Good Electrical Conductivity
While aluminium has lower conductivity than copper, its lighter weight allows larger cross-sections to be used to compensate for the difference, maintaining efficient current carrying capacity.
3. Corrosion Resistance
Aluminium forms a self-protecting oxide layer when exposed to air, which prevents deep corrosion and ensures longevity, even in outdoor or harsh environments.
4. Easy Fabrication and Installation
Aluminium is easier to work with compared to copper due to its softness and machinability. It can be cut, bent, drilled, and installed on-site with common fabrication tools, reducing labor costs and project timelines.
5. Recyclability
Aluminium is 100% recyclable without losing its physical and electrical properties. Its recycling process requires only about 5% of the energy needed for primary aluminium production, making it an environmentally friendly choice.
Design Considerations for Rigid Aluminium Busbars
Current Carrying Capacity
The cross-sectional area of a busbar must be carefully selected based on the current it will carry, ambient temperature, and installation method. Engineers follow standards like IEC 61439, NEC, or regional codes to ensure the system remains within safe temperature limits under full load.
Size and Shape Selection
Beyond flat bars, T and L shapes, or even custom extrusions, may be selected to accommodate space restrictions, mechanical strength requirements, or aesthetic considerations.
Insulation and Coatings
Depending on application and environmental exposure, different finishes can be applied:
- Bare Aluminium: Cost-effective for controlled environments
- Tin-Plated Aluminium: Prevents galvanic corrosion, particularly when used with copper terminations
- Epoxy-Coated Busbars: Provide insulation and environmental protection, eliminating the need for external insulation materials
Mechanical Strength and Rigidity
Busbars must endure mechanical stresses caused by short-circuit currents and electromechanical forces. Structural supports, clamps, and busbar spacing must be designed to prevent sagging or deformation.
Thermal Expansion
Aluminium expands approximately twice as much as copper when heated. Busbar systems must include expansion joints or flexible connections to accommodate temperature-induced length changes without damaging equipment.
Installation Guidelines
Cutting, Bending, and Drilling
Proper preparation is essential to maintain the busbar’s integrity. Sharp tools and correct techniques prevent micro-cracks and stress concentrations that could lead to failure during operation.
Mounting Methods
Rigid aluminium busbars are mounted using:
Insulated supports
Clamps
Custom-designed brackets
Proper spacing and secure clamping prevent movement during electrical faults or vibration.
Jointing and Connections
Bolted Joints: Most common due to ease of assembly and maintenance. Conductive grease is recommended to prevent oxidation at interfaces.
Welded Joints: Offer superior electrical performance but are less flexible for future modifications.
Compression Connectors: Used in high-vibration environments to ensure long-term joint integrity.
Safety Tips
Comply with local electrical codes and regulations
Use Personal Protective Equipment (PPE)
Verify torque settings for all bolted connections
Ensure proper ventilation and clearance during installation
Challenges and Solutions
Galvanic Corrosion
When aluminium contacts copper or other dissimilar metals, galvanic corrosion may occur. Solutions include:
- Using bi-metallic connectors
- Applying tin-plating to aluminium
- Using conductive grease
Oxidation Layer Handling
Aluminium naturally forms an oxide layer that can increase contact resistance. Before making electrical connections, surfaces should be cleaned mechanically and treated with conductive compounds to ensure good conductivity.
Structural Integrity in Harsh Environments
In marine, coastal, or industrial environments with high humidity or chemical exposure, additional epoxy or polyurethane coatings, or even fully enclosed busbar systems, may be required.
Future Trends
Lightweight Power Distribution
In sectors such as transportation, aerospace, and renewable energy, the shift towards lightweight designs is boosting aluminium busbar adoption.
Renewable Energy Integration
With the increasing installation of solar and wind power systems worldwide, aluminium busbars are preferred for their cost-effectiveness and resistance to environmental factors.
Smart Grids and Modern Power Systems
As intelligent power distribution and smart grids become the new standard, aluminium busbars will play a key role in improving energy efficiency, supporting dynamic load management, and integrating renewable generation sources.
Conclusion
The Rigid Aluminium Busbar is more than just a cost-effective alternative to copper; it is a modern solution aligned with the needs of today's electrical infrastructure. From commercial buildings and renewable energy facilities to industrial plants and EV charging networks, rigid aluminium busbars deliver exceptional performance, longevity, and sustainability.
By understanding their characteristics, applications, and design considerations, engineers can make informed decisions that lead to reliable, cost-effective, and environmentally friendly power distribution systems. As industries continue to evolve towards lightweight, sustainable, and high-efficiency solutions, rigid aluminium busbars are poised to remain a cornerstone of modern electrical engineering.
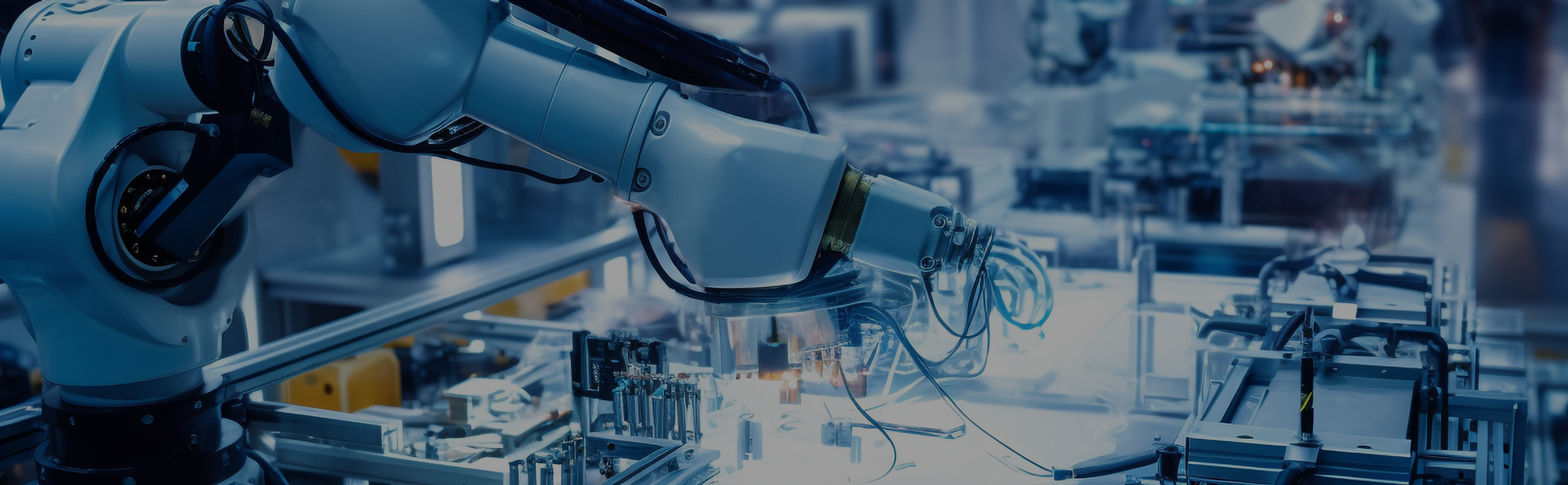