

High-Temperature Solutions and Electrical Busbars: Essential Components for Efficient Power Distribution
Delve deep into the relationship between high-temperature solutions and electrical busbars, exploring how these two critical elements work together to ensure safe, reliable, and efficient electrical systems.
In the rapidly advancing world of electrical engineering, the importance of maintaining optimal efficiency, safety, and longevity in power distribution systems cannot be overstated. Electrical systems, from the largest industrial setups to everyday consumer appliances, require components that can withstand demanding conditions. Among these critical components, electrical busbars play an essential role in the effective transmission of electrical power. However, the growing demand for high-performance systems, especially in industrial and commercial environments, necessitates the development of high-temperature solutions to address the ever-evolving challenges posed by heat in electrical infrastructure.
In this comprehensive guide, we will delve deep into the relationship between high-temperature solutions and electrical busbars, exploring how these two critical elements work together to ensure safe, reliable, and efficient electrical systems. From understanding the basics of busbars and their role in electrical circuits to examining the innovative materials and technologies that support high-temperature environments, this article provides a detailed examination of how engineers and manufacturers are developing more resilient electrical solutions.
Understanding Electrical Busbars: A Key Element in Power Distribution
An electrical busbar is a metal bar or conductor that serves as a common connection point for multiple circuits. Its primary function is to distribute electrical power to various parts of an electrical system. Busbars are typically made of copper, aluminum, or a combination of both materials, and are designed to carry large currents with minimal resistance. They can be found in a wide variety of applications, including switchboards, distribution panels, and electrical panels within substations.
Types of Electrical Busbars
- Copper Busbars: Copper is a popular material for busbars due to its excellent conductivity and high resistance to corrosion. Copper busbars are ideal for situations where high current-carrying capacity is required in a compact design.
- Aluminum Busbars: Aluminum busbars are lighter and less expensive than copper alternatives, making them suitable for applications where weight and cost are significant factors. They are often used in large-scale industrial applications and power distribution networks.
- Hybrid Busbars: Combining copper and aluminum can offer a balance between cost, weight, and performance, especially in high-current applications.
Challenges Posed by High Temperatures in Electrical Systems
High temperatures can have detrimental effects on electrical systems, including busbars. When electrical components such as busbars carry current, they generate heat as a byproduct due to electrical resistance. This heat can cause various problems, including:
- Thermal Expansion and Contraction: As busbars heat up, they expand, and when they cool down, they contract. This constant expansion and contraction can lead to mechanical stress, loosening of connections, and, over time, damage to the busbar and surrounding components.
- Degradation of Insulation: High temperatures can cause insulation materials around the busbars and other electrical components to break down or degrade. This can result in short circuits, arcing, or even fires.
- Reduced Conductivity: As busbars heat up, their electrical conductivity may decrease, leading to less efficient power distribution and potential overheating.
To address these challenges, engineers and manufacturers rely on high-temperature solutions that can mitigate the risks associated with heat in electrical systems.
High-Temperature Solutions for Electrical Busbars
High-temperature solutions are specifically designed materials, technologies, and systems that can withstand elevated temperatures without compromising the safety, performance, or integrity of electrical systems. These solutions are crucial for maintaining the functionality of busbars, which are typically exposed to high temperatures in industrial settings, data centers, and electrical substations.
Here are some of the primary high-temperature solutions used to enhance the performance and durability of electrical busbars:
1. High-Temperature Materials
The selection of materials used for electrical busbars plays a significant role in ensuring that they can operate efficiently in high-temperature environments. Materials with high thermal conductivity, resistance to oxidation, and the ability to maintain mechanical integrity at elevated temperatures are essential.
Ceramic-Coated Busbars: Ceramic coatings can be applied to busbars to provide an insulating layer that can withstand high temperatures. These coatings offer electrical insulation properties and help prevent thermal degradation of the underlying material. Additionally, ceramic coatings can enhance the mechanical strength of busbars, preventing bending or warping under extreme heat.
High-Temperature Alloys: In addition to copper and aluminum, some high-temperature alloys are designed to handle extreme environments. These alloys offer improved heat resistance, mechanical strength, and durability, making them ideal for use in industrial and power transmission systems that are subjected to high temperatures.
Thermally Conductive Polymers: In some applications, thermally conductive polymers are used to improve the heat dissipation properties of busbars. These materials combine the insulating properties of polymers with the ability to conduct heat away from critical components, preventing the buildup of excessive temperatures.
2. Thermal Management Systems
In many high-temperature environments, thermal management systems are essential for preventing overheating. These systems are designed to control the temperature of electrical busbars and other critical components by dissipating heat effectively.
Heat Sinks: Heat sinks are used to increase the surface area available for heat dissipation. By attaching a heat sink to a busbar, engineers can significantly improve its ability to transfer heat away from the component, ensuring it stays within safe operating temperatures.
Cooling Systems: Active cooling systems, such as forced-air or liquid cooling, can be used to regulate the temperature of electrical systems. For example, liquid cooling systems can circulate coolant through pipes or channels around the busbar to absorb heat and maintain optimal temperatures.
Thermal Insulation: Insulating materials that are resistant to high temperatures can be applied around electrical busbars to minimize heat transfer to surrounding components. These materials can help maintain the temperature of the busbar within acceptable limits, preventing overheating and thermal damage.
3. Advanced Monitoring and Control Systems
With the increasing complexity of modern electrical systems, it is essential to have advanced monitoring and control systems to detect and manage temperature fluctuations in real-time. These systems can provide crucial data about the thermal performance of busbars and allow engineers to make adjustments before temperatures reach dangerous levels.
Thermal Sensors: Thermal sensors embedded in or around electrical busbars can monitor their temperature in real-time. These sensors can trigger alarms or automatically adjust cooling systems to prevent overheating.
Smart Circuit Breakers: In some advanced systems, smart circuit breakers are used to automatically disconnect power in the event of excessive heat or other dangerous conditions. These circuit breakers can help prevent electrical fires or other catastrophic failures by cutting off the power before temperatures rise to unsafe levels.
4. Protective Coatings and Sealants
In high-temperature environments, the integrity of electrical busbars is paramount. Protective coatings and sealants are applied to busbars to prevent oxidation, corrosion, and other forms of damage caused by exposure to heat, moisture, and contaminants.
Anti-Corrosion Coatings: In industrial settings where electrical systems are exposed to harsh chemicals or humidity, anti-corrosion coatings are applied to busbars to protect them from rust and other forms of degradation. These coatings are particularly important in environments where the busbar operates at high temperatures and in aggressive atmospheres.
High-Temperature Sealants: High-temperature sealants are used to protect electrical connections and components from thermal stress, dirt, and moisture. These sealants ensure that the electrical integrity of the system is maintained even in the harshest conditions.
The Role of High-Temperature Solutions in Power Efficiency and Safety
By integrating high-temperature solutions into the design of electrical systems, especially with regard to busbars, engineers can ensure that electrical power distribution remains both efficient and safe. High-performance materials and thermal management systems reduce the risk of overheating, which can cause energy losses, equipment failure, and even safety hazards like fires. In addition, advanced monitoring systems provide critical data that allow for proactive management of electrical systems, ensuring that problems are detected and addressed before they lead to catastrophic failures.
Furthermore, as industrial and technological applications become more demanding, the need for high-temperature solutions is only expected to grow. With the development of more efficient, reliable, and sustainable technologies, the future of electrical power distribution looks promising, and high-temperature solutions will continue to be at the forefront of these advancements.
Conclusion
In conclusion, the combination of high-temperature solutions and electrical busbars is essential for maintaining the efficiency, reliability, and safety of electrical power distribution systems. The rise of industrial applications and the increasing demand for high-performance electrical systems has driven innovation in materials, thermal management, and monitoring technologies, ensuring that busbars can operate efficiently even in the most demanding environments.
As electrical systems continue to evolve, the role of high-temperature solutions will become increasingly critical in preventing failures, improving power distribution, and enhancing overall system performance. Engineers and manufacturers must remain vigilant in adopting these solutions to meet the growing demands of modern electrical infrastructure. By prioritizing the durability and heat resistance of key components like busbars, we can ensure that electrical systems continue to function reliably, safely, and efficiently for years to come.
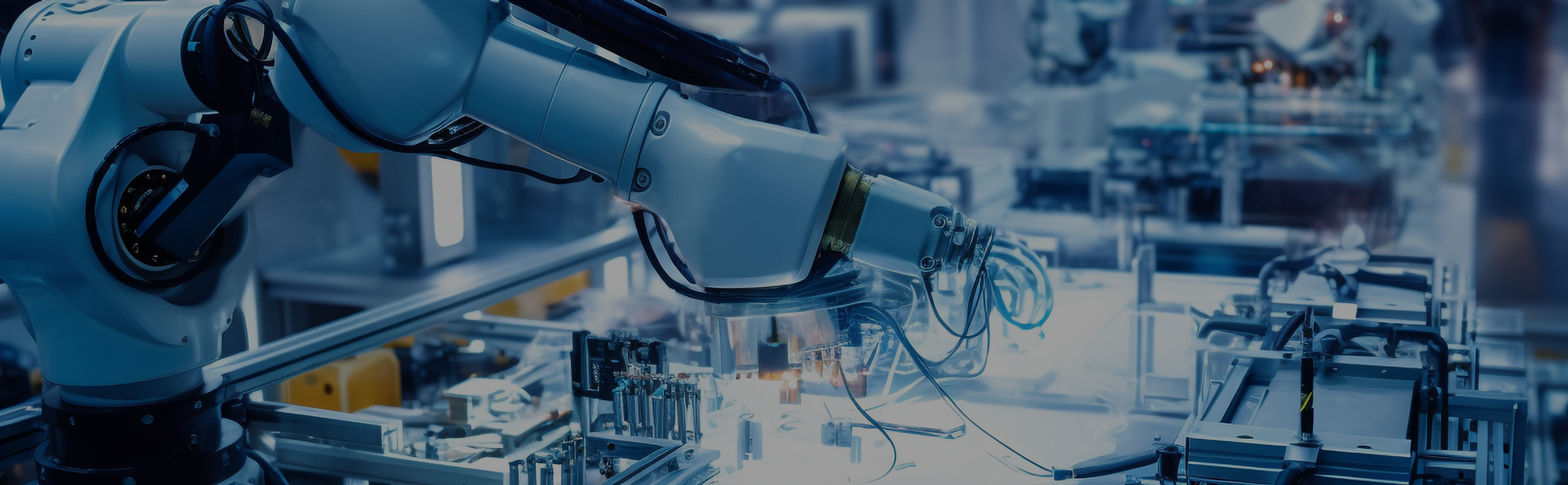