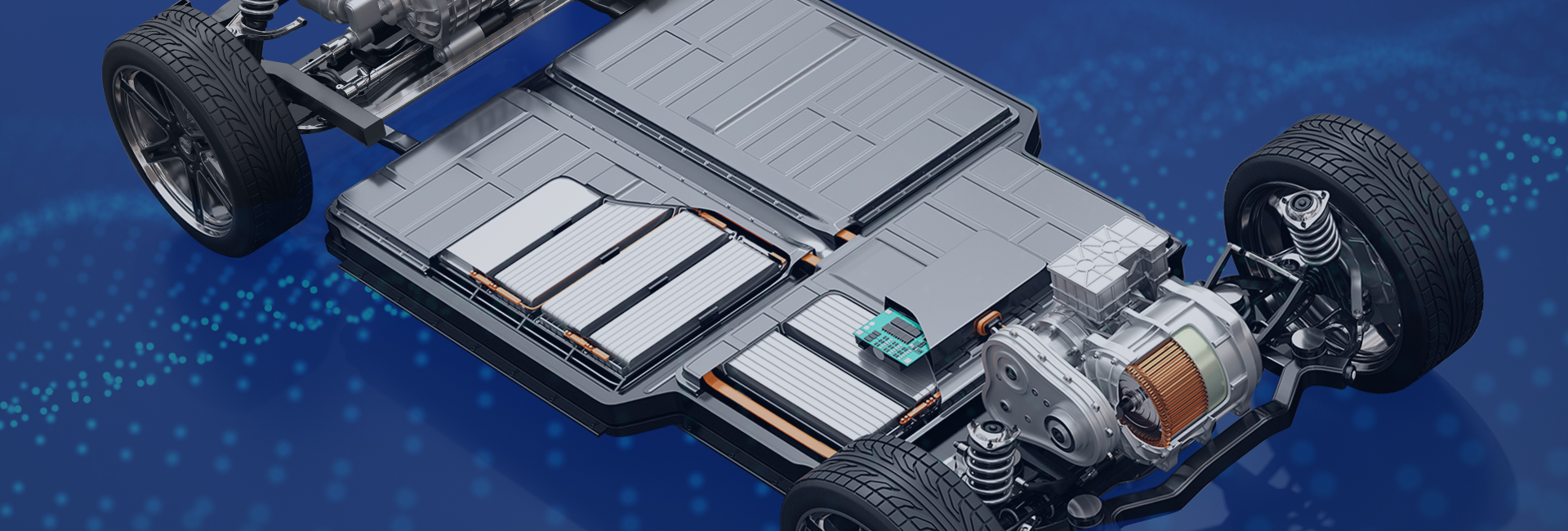
EMPOWER EVS WITH PRECISION
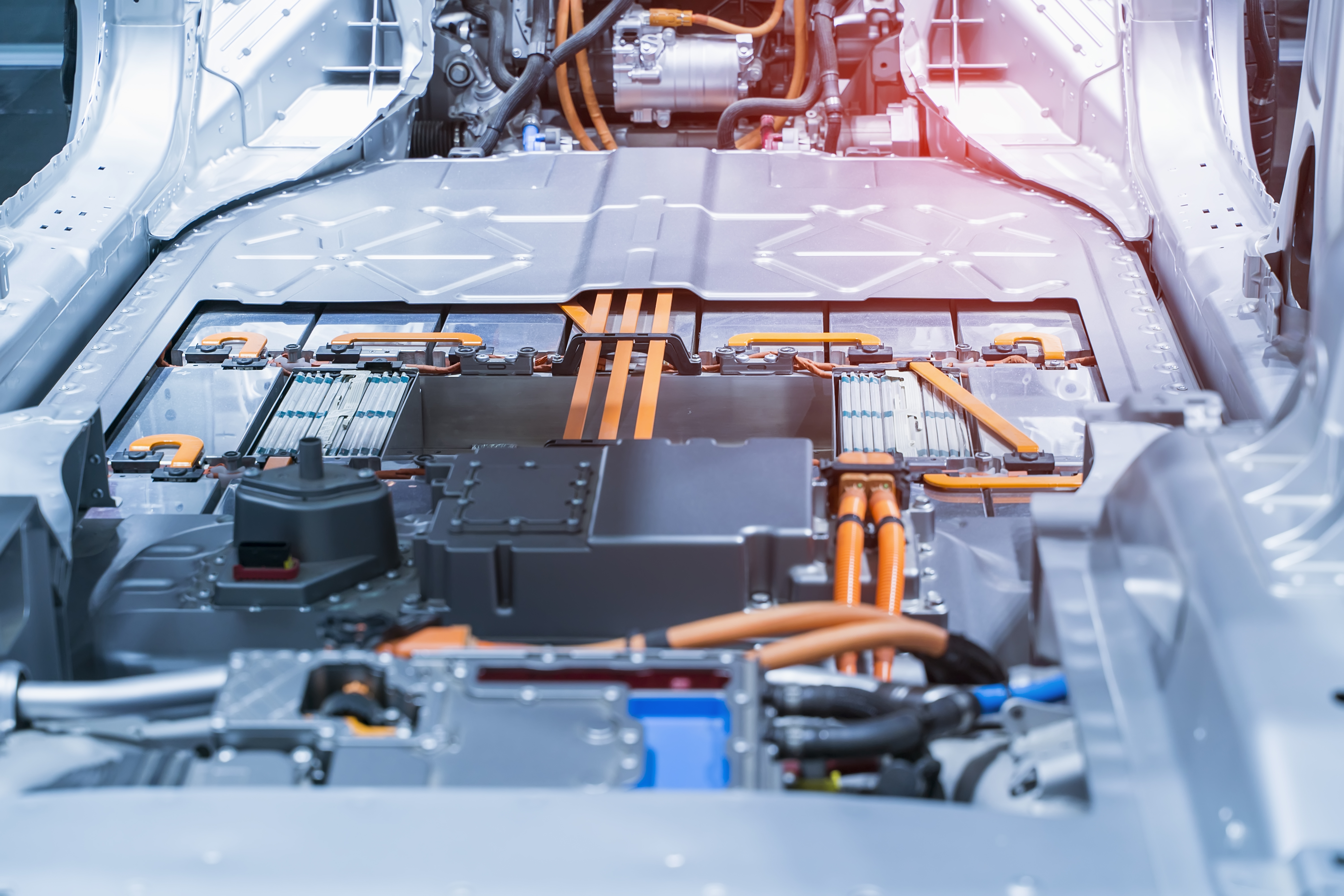

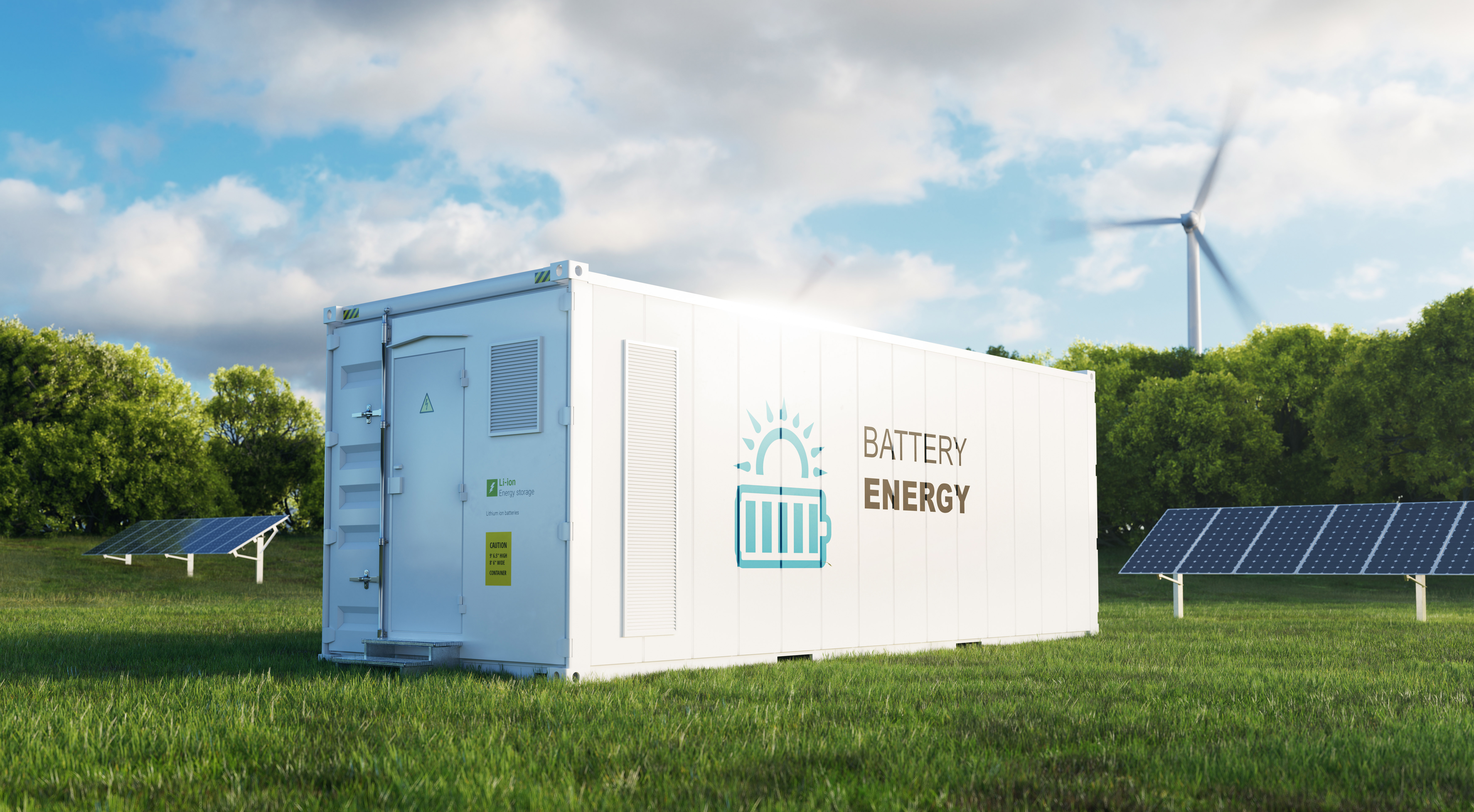

RHI offers a wide range of premium copper busbar products, including rigid, flexible, insulated, and nickel/tin-plated options.
Each product undergoes stringent quality control and testing to ensure performance that surpasses industry standards. For high-performance and dependable solutions, RHI busbars are your top choice.
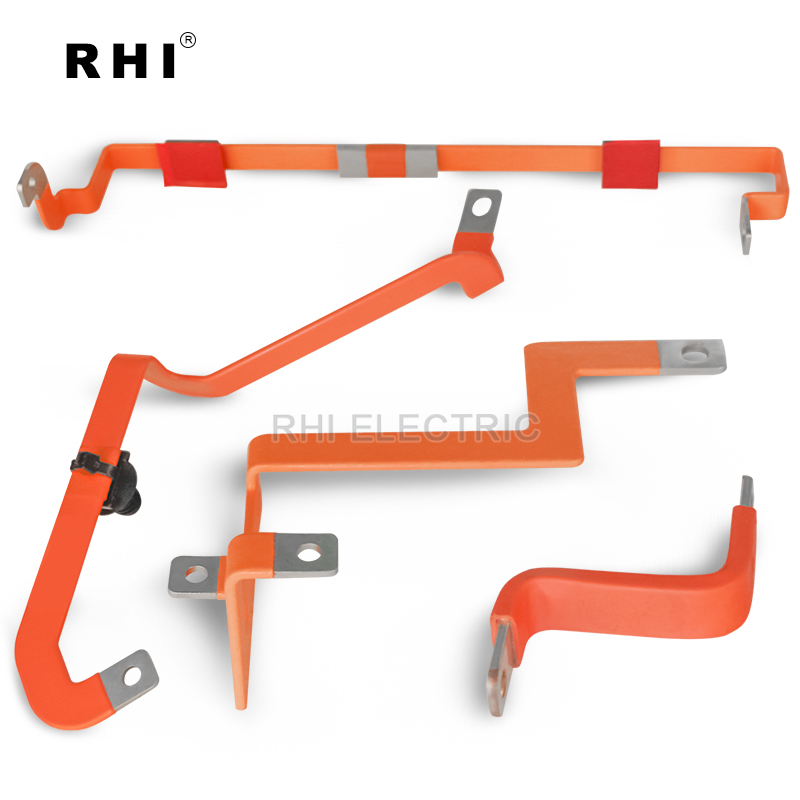
RHI manufactures lightweight aluminum busbar products, including stamped, dovetail, clinched, and copper-aluminum composite types.
These aluminium busbars serve as conductor connectors for cylindrical batteries, prismatic cells, and pouch batteries, offering notable advantages such as neat, efficient wiring and space-saving design.
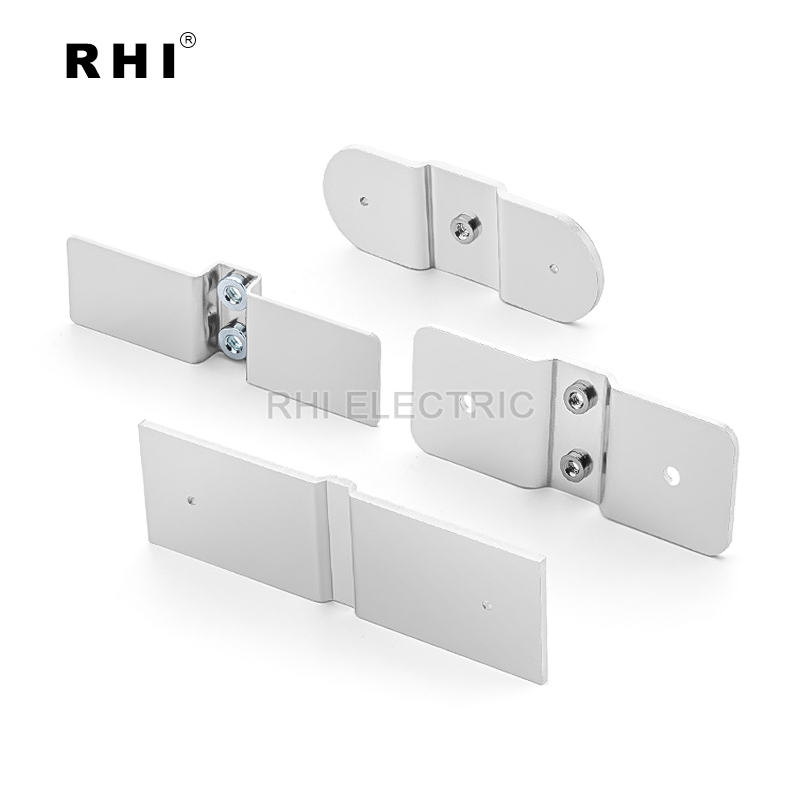
RHI manufactures flexible-rigid composite busbars that combine the features of flexible and rigid busbars to provide excellent conductivity and efficient power transmission. Compared to pure rigid busbars, composite designs reduce weight, while the flexibility of the busbars simplifies installation, making them ideal for complex spaces, especially in the new energy sector.
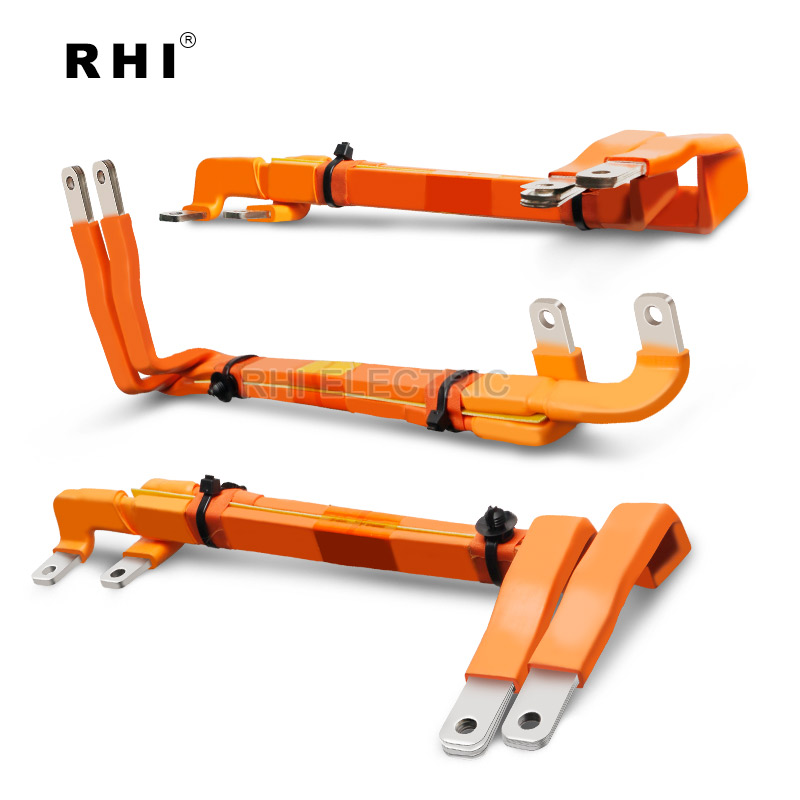
RHI masters copper-to-aluminium technology, using aluminium as the primary conductor and copper at both ends of the busbar. This copper-aluminium composite busbar offers excellent electrical conductivity and heat dissipation while reducing weight and material costs. It is particularly beneficial in cost-sensitive applications, such as new energy vehicle engineering, providing economic advantages.
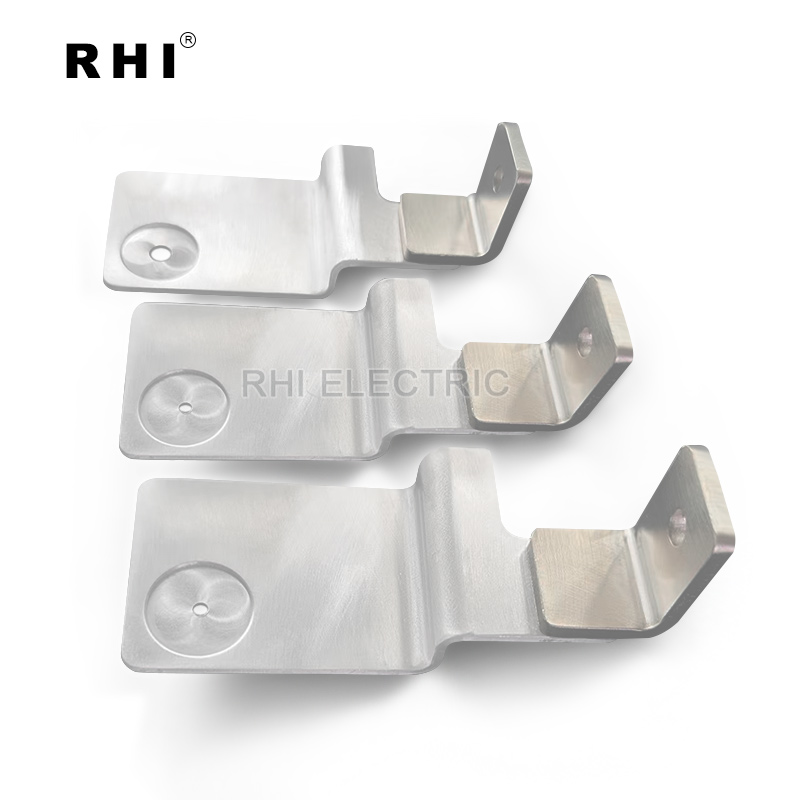
RHI specializes in injection-molded busbars, ideal for the power and new energy sectors. These busbars offer high customization and integrated molding, meeting complex design needs, reducing assembly time, and improving efficiency.
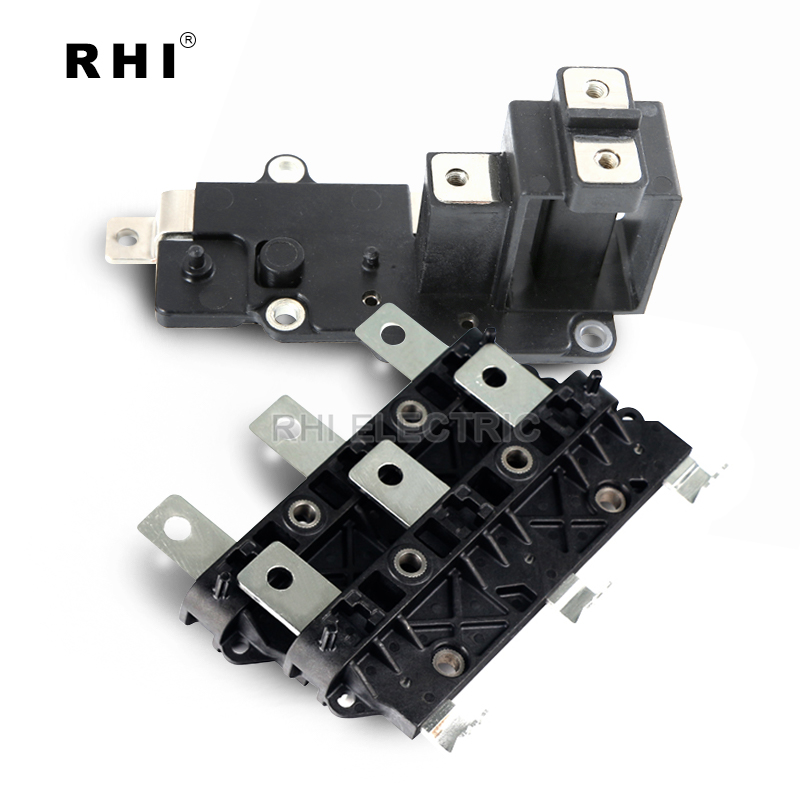
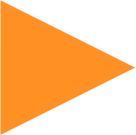

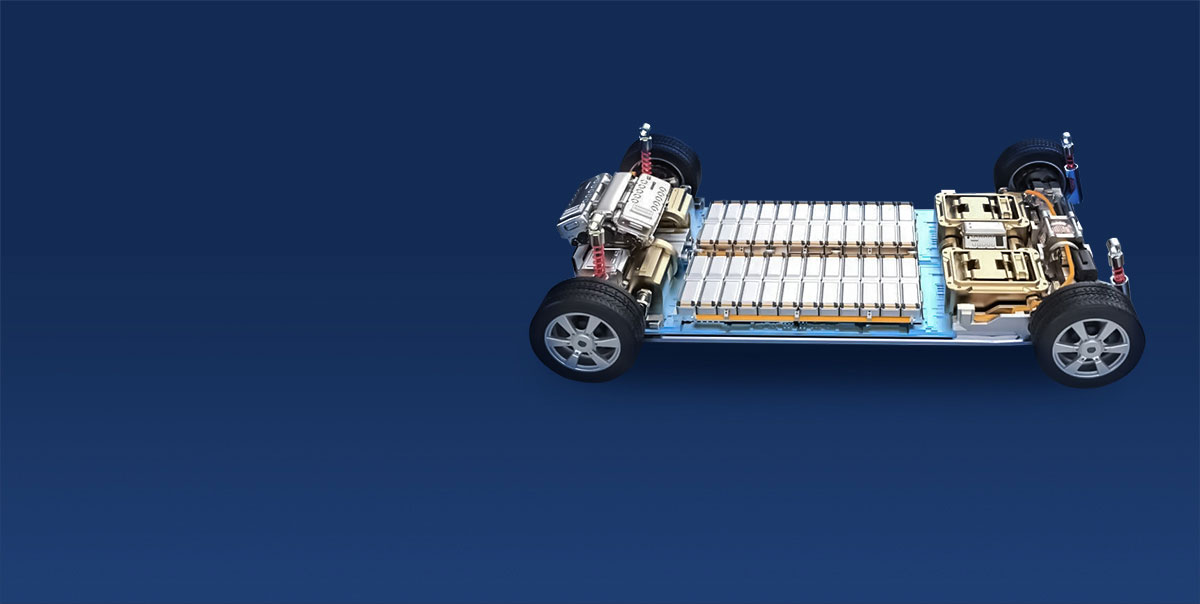
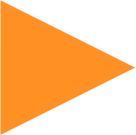
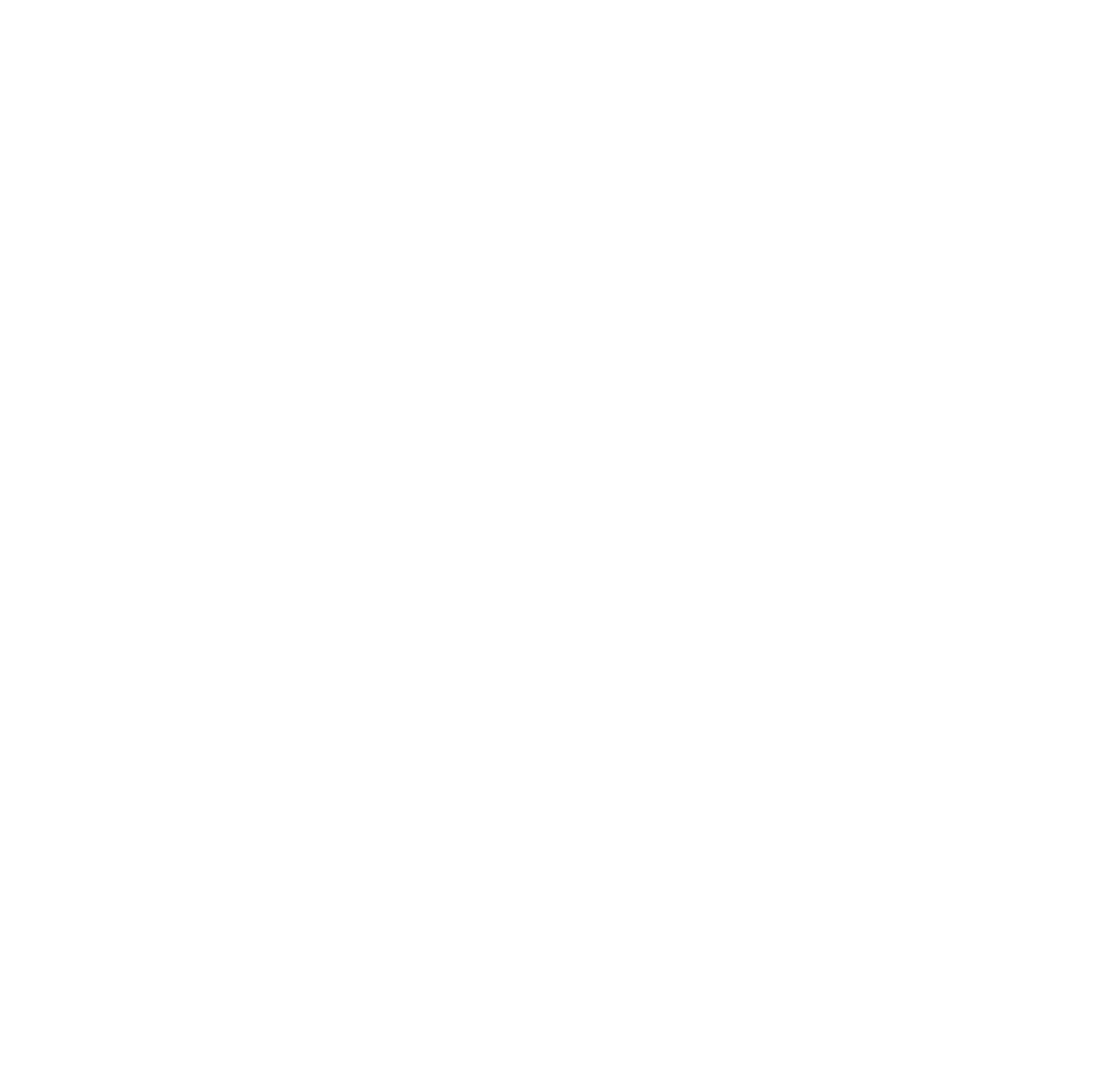
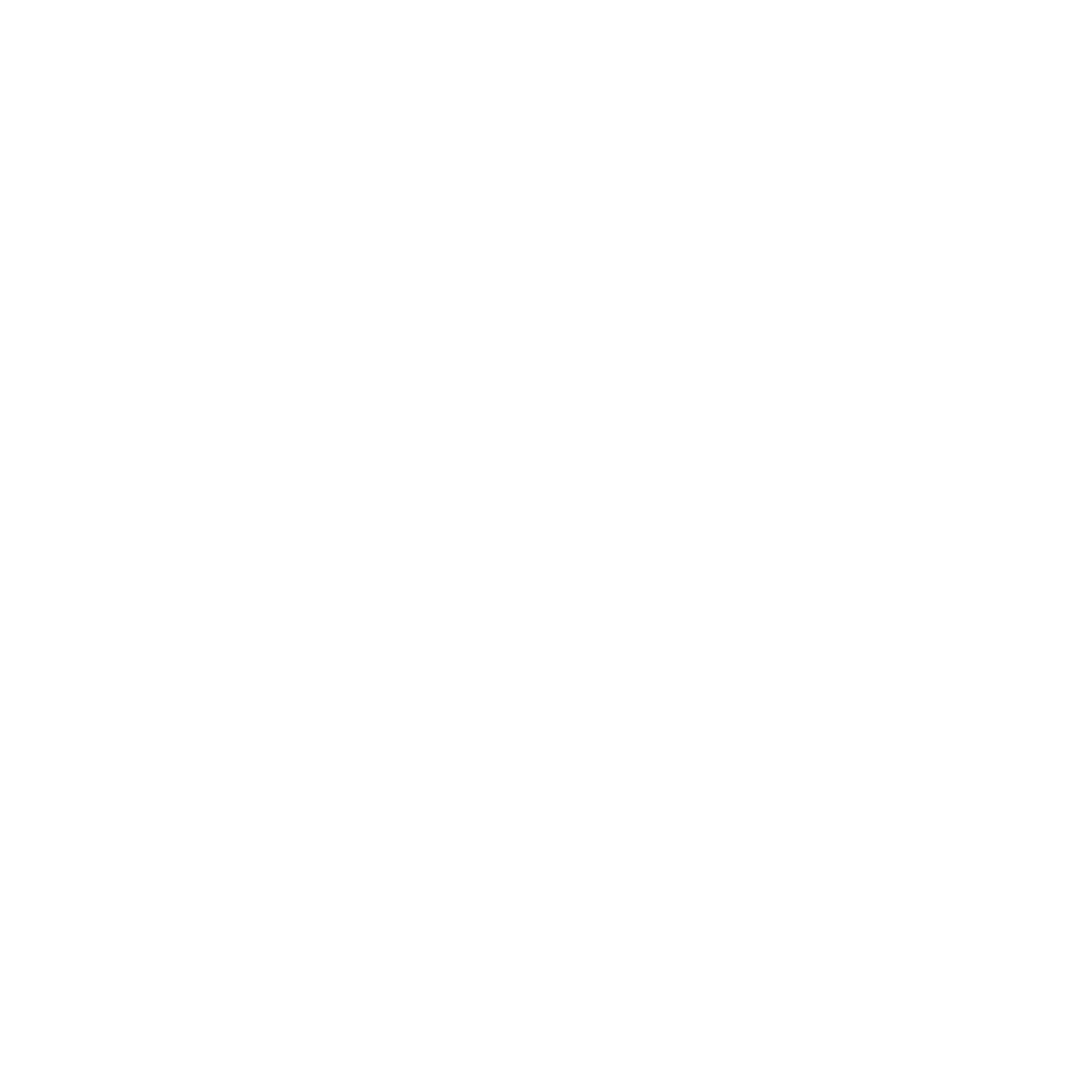
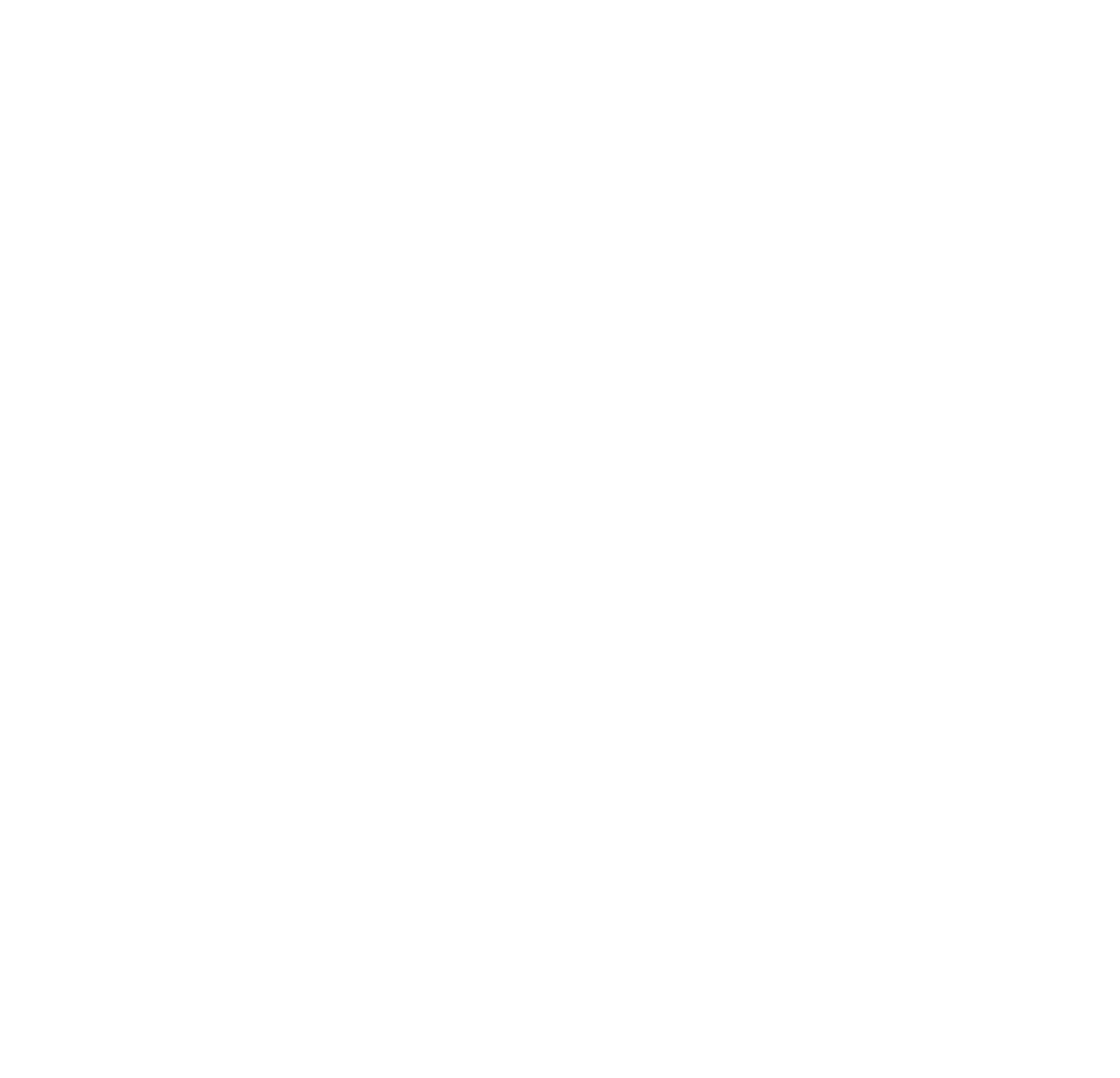
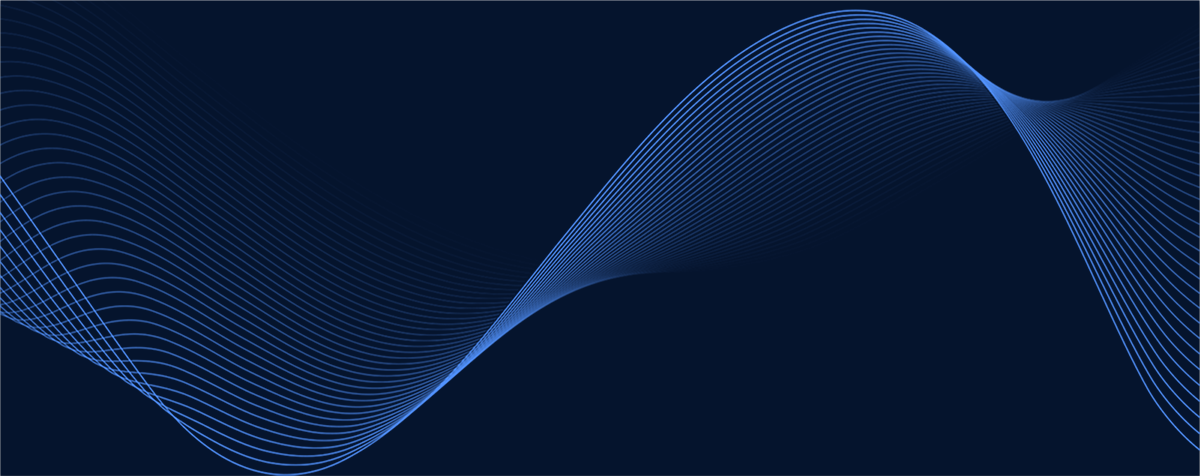
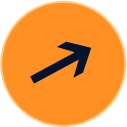
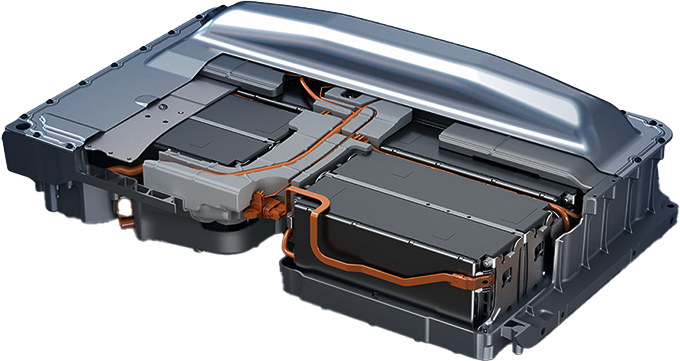
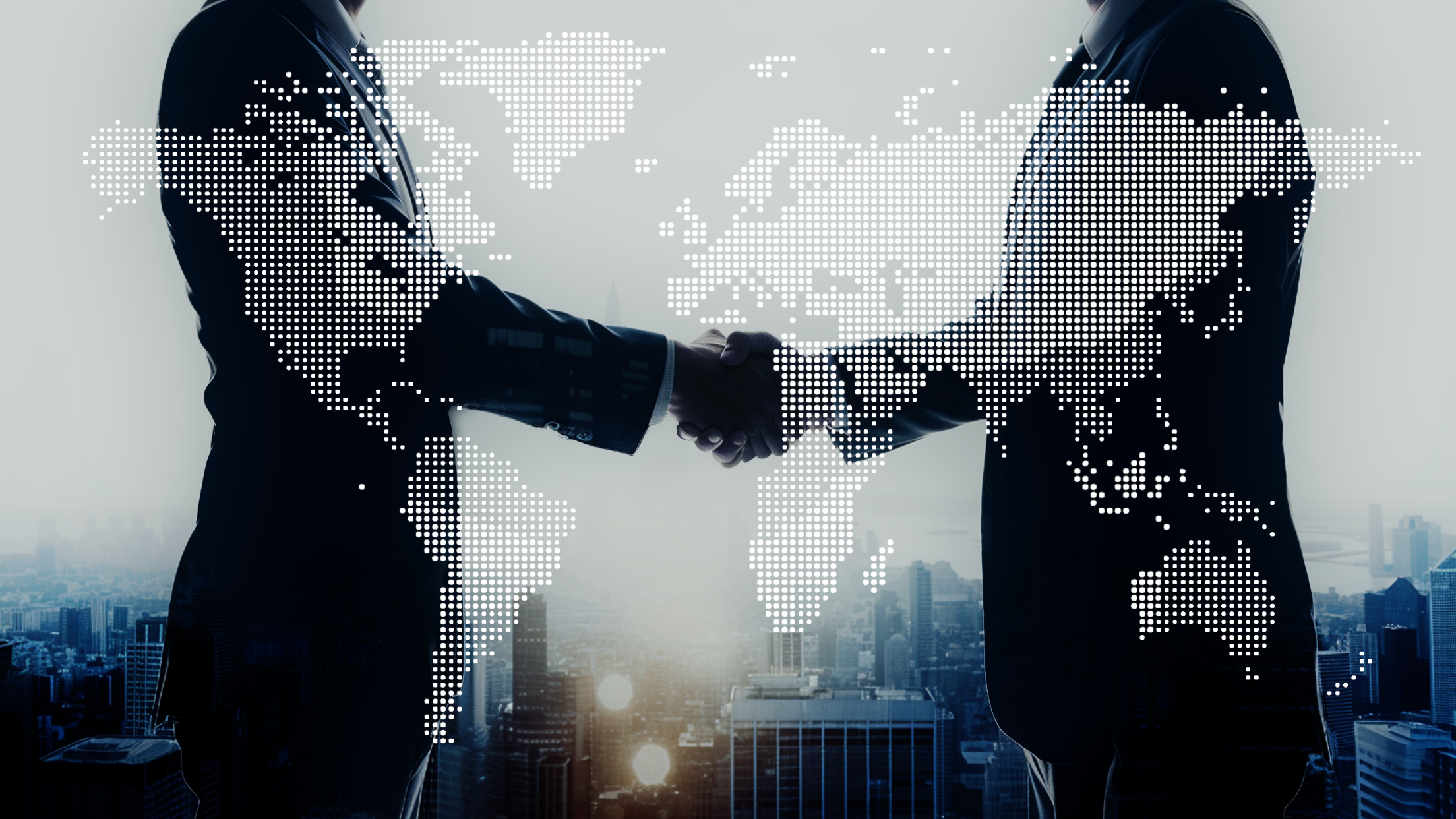
Yes, our experienced R&D team of over 70 professionals can provide customized busbar design services to meet your specific needs. RHI collaborates closely with you during the design process, offering optimization suggestions to improve heat dissipation and reduce electrical resistance, ensuring optimal busbar performance.
RHI maintains strict quality control through initial, in-process, and final inspections, including GP12 for stringent requirements. Additionally, RHI uses CCD visual inspection for precise mechanical checks, ensuring product quality meets international standards.
RHI holds ISO 9001, IATF 16949, ISO 45001, and ISO 14001 certifications, continually enhancing our production and management for compliance. Our busbar products also meet RoHS and REACH standards, backed by the relevant compliance certificates.
RHI provides an 8-year, 100,000-kilometer warranty to OEMs and comprehensive after-sales service. Our standard response time for any issues is within 48 hours.
RHI uses advanced equipment such as automated welding machines, 3D bending machines, extrusion machines, stamping machines, and automatic winding machines. Our capabilities include laser welding, diffusion brazing, and various surface treatments like nickel and tin plating, as well as multiple insulation techniques. All processes are strictly controlled to ensure high quality and adherence to design specifications.
RHI offers cost optimization solutions by replacing pure copper with copper-to-aluminium busbars, optimizing structural design to reduce material consumption, and enhancing surface treatments with tin or nickel plating. Our advanced automated welding and stamping technologies further lower manufacturing costs while preserving optimal electrical performance.
Yes, RHI performs comprehensive performance tests, including short-circuit withstand, contact resistance, EDM, pull-off strength, bending capability, and aging tests. All tests are compliant with industry standards and validated by independent laboratories.
RHI provides a detailed and transparent quotation covering all costs, including materials, processing, tooling, and other fees. Our goal is to offer competitive pricing while meeting your technical requirements.
Yes, our experienced R&D team of over 70 professionals can provide customized busbar design services to meet your specific needs. RHI collaborates closely with you during the design process, offering optimization suggestions to improve heat dissipation and reduce electrical resistance, ensuring optimal busbar performance.
RHI uses advanced equipment such as automated welding machines, 3D bending machines, extrusion machines, stamping machines, and automatic winding machines. Our capabilities include laser welding, diffusion brazing, and various surface treatments like nickel and tin plating, as well as multiple insulation techniques. All processes are strictly controlled to ensure high quality and adherence to design specifications.
RHI maintains strict quality control through initial, in-process, and final inspections, including GP12 for stringent requirements. Additionally, RHI uses CCD visual inspection for precise mechanical checks, ensuring product quality meets international standards.
RHI offers cost optimization solutions by replacing pure copper with copper-to-aluminium busbars, optimizing structural design to reduce material consumption, and enhancing surface treatments with tin or nickel plating. Our advanced automated welding and stamping technologies further lower manufacturing costs while preserving optimal electrical performance.
RHI holds ISO 9001, IATF 16949, ISO 45001, and ISO 14001 certifications, continually enhancing our production and management for compliance. Our busbar products also meet RoHS and REACH standards, backed by the relevant compliance certificates.
Yes, RHI performs comprehensive performance tests, including short-circuit withstand, contact resistance, EDM, pull-off strength, bending capability, and aging tests. All tests are compliant with industry standards and validated by independent laboratories.
RHI provides an 8-year, 100,000-kilometer warranty to OEMs and comprehensive after-sales service. Our standard response time for any issues is within 48 hours.
RHI provides a detailed and transparent quotation covering all costs, including materials, processing, tooling, and other fees. Our goal is to offer competitive pricing while meeting your technical requirements.
